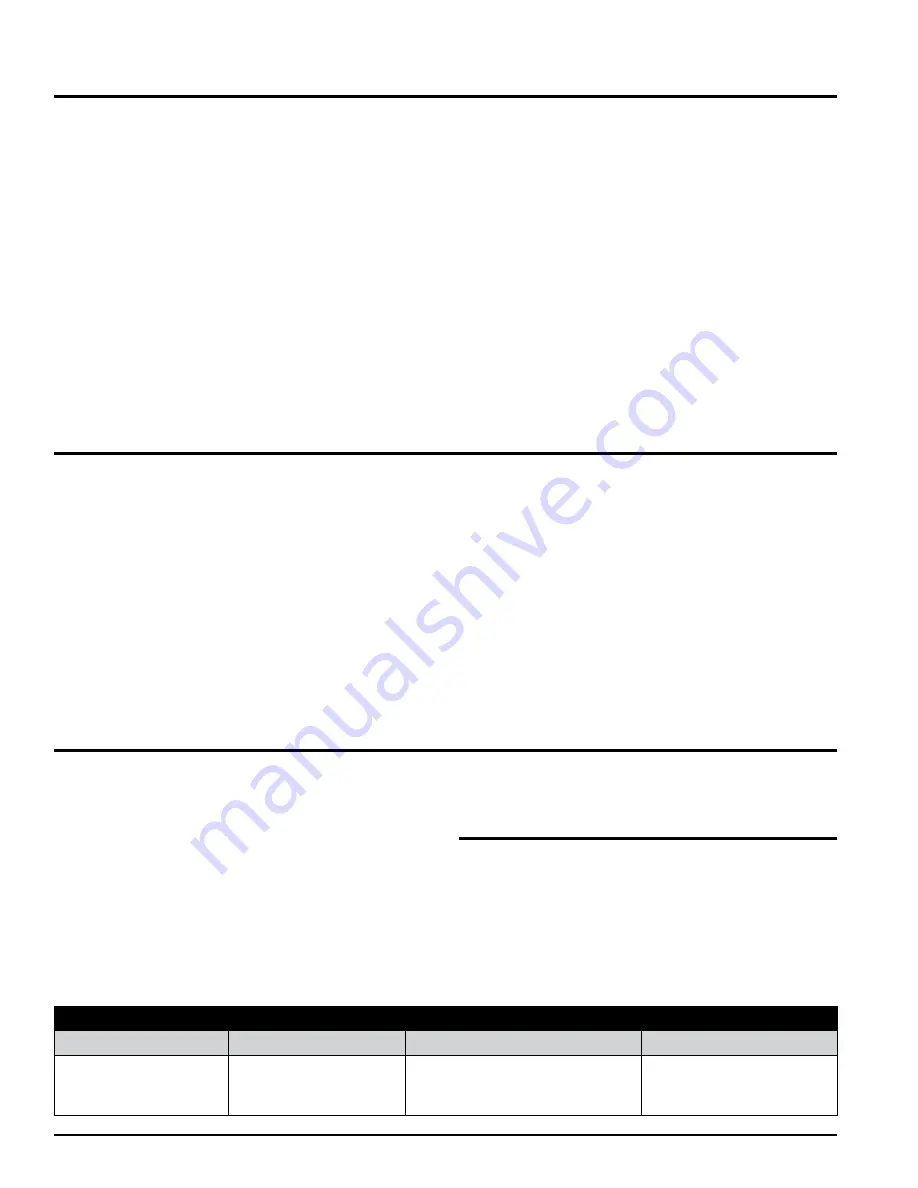
Before You Begin
DEAR ECHO Bear Cat
®
CUSTOMER
Thank you for purchasing an ECHO Bear Cat product. The ECHO Bear Cat line is designed, tested, and manufactured
to give years of dependable performance. To keep your machine operating at peak efficiency, it is necessary to adjust
it correctly and make regular inspections. The following pages will assist you in the operation and maintenance of your
machine. Please read and understand this manual before operating your machine.
If you have any questions or comments about this manual, please call us toll-free at 888.625.4520.
If you have any questions or problems with your machine, please call or write your local authorized ECHO Bear Cat
dealer.
This document is based on information available at the time of its publication. ECHO Bear Cat is continually making
improvements and developing new equipment. In doing so, we reserve the right to make changes or add improvements
to our product without obligation for equipment previously sold.
PLEASE SEND US YOUR WARRANTY CARD
A warranty card is included in your owner’s kit packaged with your machine. Please take the time to fill in the information
requested on the card. When you send your completed card to us, we will register your machine and start your coverage
under our limited warranty or go to bearcatproducts.com/Product-Support/Product-Registration.
SERIAL NUMBER OR VIN
© 2013, CRARY
®
INDUSTRIES, ALL RIGHTS RESERVED. PRODUCED AND PRINTED IN THE U.S.A.
IDENTIFICATION NUMBER LOCATION
Your machine will have either a serial number or vehicle
identification number (VIN). VINs are located on the left
side of the trailer frame near the hitch. They are 17-digit
numbers of the format: 5VJAA001XXWXXXXXX. Serial
numbers are located on the machine body. They are
6-digit numbers.
Record your identification number in the space provided
and on the warranty registration card.
FOR MACHINE SERVICE OR PARTS
For service assistance, contact your nearest authorized
ECHO Bear Cat dealer or the factory. For parts, contact
your authorized dealer. The parts manual for your
machine is available at bearcatproducts.com/Product-
Support/Find-A-Product-Manual. Your dealer will need to
know the serial number of your machine to provide the
most efficient service. See below for information on how
to identify and record the serial number for your machine.
FOR ENGINE SERVICE OR PARTS
For engine service or parts, contact your nearest
authorized engine dealer. ECHO Bear Cat does not
handle any parts, repairs or warranties for engines.
ORDERING PARTS
Only genuine ECHO Bear Cat replacement parts should
be used to repair the machine. Replacement parts
manufactured by others could present safety hazards,
even though they may fit on this machine. Replacement
parts are available from your ECHO Bear Cat dealer.
Provide the following when ordering parts:
The SERIAL NUMBER or VIN of your machine.
The PART NUMBER of the part.
The PART DESCRIPTION.
The QUANTITY needed.
HOW TO CONTACT ECHO Bear Cat
ADDRESS
PHONE
HOURS
237 NW 12th Street
P.O. Box 849
West Fargo, ND 58078
888.625.4520
701.282.5520
Fax: 701.282.9522
Monday - Friday
8 a.m. to 5 p.m.
Central Time