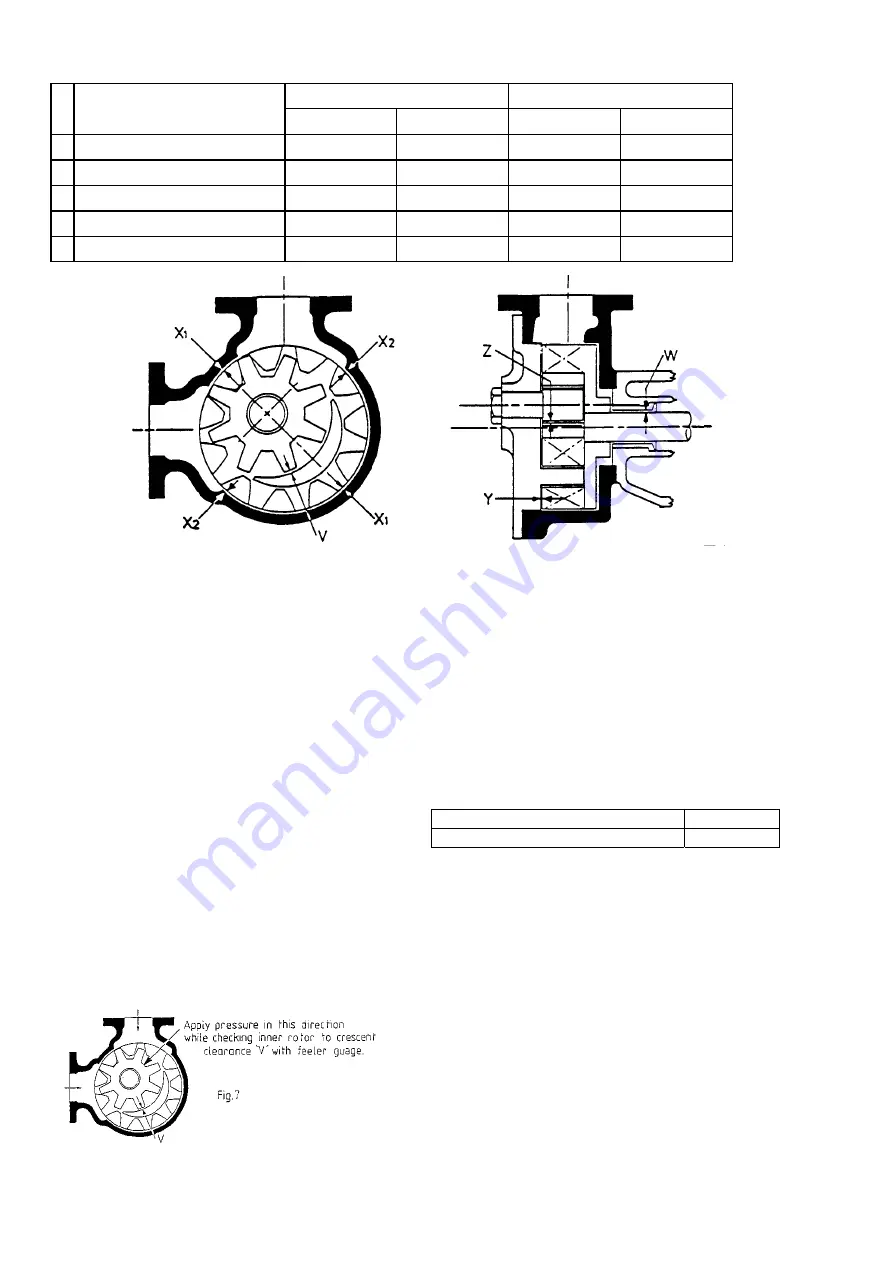
TABLE OF CLEARANCES
Metallic
Carbon
Running Clearances
'A'
CLEARANCE
'B'
CLEARANCE
'A'
CLEARANCE
'B'
CLEARANCE
Z
Diametral - Rotor Pin to Bearing
0.12-0.16 mm
0.12-0.16 mm
0.09-0.13mm
0.09-0.13mm
Y
Axial - Rotors to Cover
0.13-0.18 mm
0.17-0.22 mm
0.13-0.18 mm
0.17-0.22 mm
X
Diametral - Outer Rotor to Body
0.28-0.38 mm
0.40-0.53 mm
0.28-0.38 mm
0.40-0.53 mm
W Diametral - Shaft to Bearing
0.10-0.14 mm
0.13-0.16 mm
0.08-0.11mm
0.10-0.14mm
V
Radial - Inner Rotor to Crescent
0.03-0.08 mm
0.03-0.08 mm
0.02-0.06mm
0.02-0.06mm
Figure 6
6.
Carry out preliminary sizing checks:
a) Axial length of Inner Rotor, Outer Rotor teeth
and Cover crescent must be matched to within
+/- 0,02mm.
b) Outer Rotor in Body diametral clearance. Note:
If checking by feeler gauge method, allowance
or compensation must be made for eccentricity
caused by:
i) Weight of Rotor.
ii) Clearances between Shaft and Bracket
Bearing.
iii) Lack of Bearing support at drive end
6
To measure clearance, insert feeler gauge at
two opposite measurement points 'X
1
'. Add the
two clearances together. This will give the
diametral clearance 'X' for the two points.
Repeat this procedure for the other two
measurement points 'X
2
'.
c) To check clearance between Inner Rotor and
Cover crescent, Inner Rotor should be held
towards inlet plane. Refer Fig. 7
7.
Ensure all lubrication/cooling circulation
harness assemblies are clear of any
obstructions.
8.
EBSRAY recommend replacement of all
Gaskets, Seals and "O"rings at every overhaul,
to ensure positive sealing.
4.6
REASSEMBLY
(Refer Drg No. CMP051)
TORQUE SETTINGS
Cover to Body Studs and Nuts
203.4 Nm
Bracket to Body Setscrews:
203.4 Nm
During reassembly, lubrication is required in some
areas. All lubrication in areas where it may come into
contact with pumped product should be with a
product compatible lubricant. The Bracket Ball
Bearing and lockring Seals may be lubricated with
any high quality lithium base grease suitable for the
operating conditions.
1.
(For pumps fitted with SJ Cover Plate only)
Using a new Cover Gasket, locate the SJ Cover
Plate on the Cover with the Inner Rotor Pin bores in
alignment and temporarily fasten the two together
using bolts of the same diameter as the Cover
bolts. After fastening Inner Roror Pin (Step 4)
remove these temporary bolts.
2.
Fit Inner Rotor Pin Gasket to the Inner Rotor Pin
locating step.
Summary of Contents for HD600
Page 11: ...11 11 ...