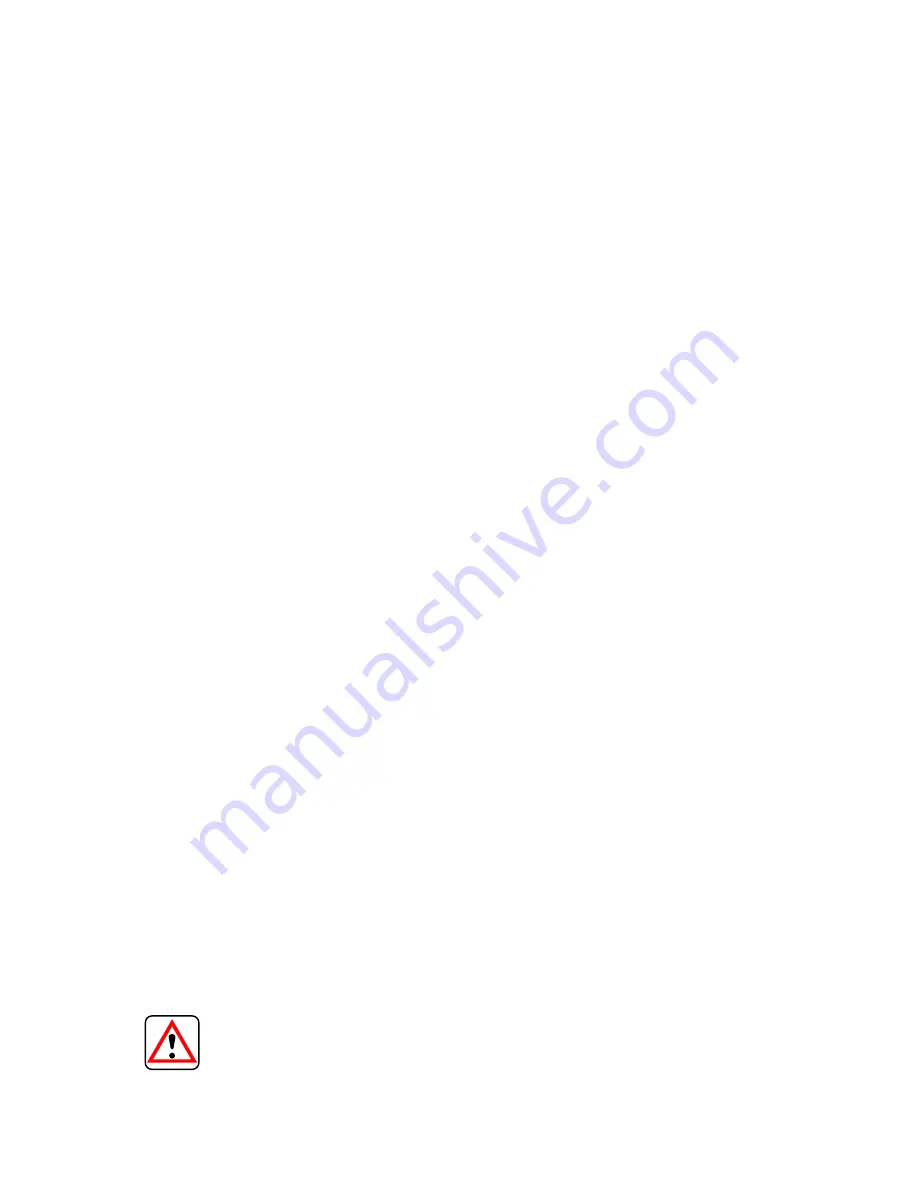
34
5. Remove spring (14), spacer (15) and washer (16)
from body bore.
NOTE
Some parts may not exist on your valve. Check the
omit codes on Figure 18. On “N” type pilot valves,
detent SA (16a) replaces washer (16). Remove the
detent S/A (16a) but DO NOT remove retaining ring
from the detent.
6. If the pilot valve is equipped with two solenoids,
remove parts (17 through 25 and 30 through 32) from
opposite end of body (38).
NOTE
Spring (30) and washer (32) do not exist on “N”
type pilot valves.
NOTE
The following step (7) pertains to spring offset “A”
and spring centered “B” pilot valves only.
7. Remove the four screws (17a) from end cover (18a)
and then remove the end cover. Remove and discard O-Ring
(19a) from end cover. Remove parts (30 through 32) from
body bore.
NOTE
Spacer (31) and washer (32) do not exist on spring
offset “A” models.
8. Remove the pilot spool (33) from body (38).
9. Secure the body and remove plugs (34 and 36) from
body (38). Remove O-Rings (35 and 37) from plugs and
discard.
F. Cleaning
All parts must be thoroughly cleaned and kept clean during
inspection and assembly. The close tolerance of the valve
bodies and spools make this requirement critical. Clean all
parts with a commercial solvent that is compatible with the
system fluid. Compressed air may be used to clean the
valve, but it must be filtered to remove water and contamina-
tion. Clean compressed air is particularly useful for cleaning
spool orifices, body passages and drying parts.
NOTE
If the spool shows and indication of damage due to
contamination, drain the fluid from the system.,
flush all lines and clean the reservoir. New filter
elements should be installed and new fluid should
be added to the reservoir.
G. Inspection, Repair and
Replacement
1. Check that all internal passages are clean and free
from obstruction. Examine all mating surfaces for nicks and
burrs. Minor nicks and burrs can be removed with crocus
cloth or an India stone.
CAUTION
DO NOT stone the edges of spool sealing lands. Re-
move minor burrs with #500 grit paper. Use the paper
very lightly on the outer diameter of each spool.
2. Inspect all screws for evidence of damaged threads.
If threads are damaged, replace the screws.
3. Inspect all springs for distortion or wear. The ends of
the springs shall be square and parallel to each other.
Replace springs that are damaged or distorted.
4. Check push pins, pole faces, washers and manual
plungers for burrs, cracks or mushrooming. Replace all parts
that show evidence of wear.
5. Visually inspect the internal coring (bore) of each
body for heavy scratches or erosion across the spool land
sealing areas. If such evidence is found, replace the valve. If
the body bore passes inspection, check bore to spool
clearance as follows:
a. Lubricate spools and body bores with clean
system fluid. Make sure the parts are clean.
b. Insert the spool into its body bore. Rotate the spool
360
°
while moving it back and forth. Observe the following:
If the spool does not move freely, the spool is sticking inside
the body bore. Remove the spool and recheck the spool and
body bore for scratches and/or burrs. Remove any minor
scratches or burrs with India stone or crocus cloth. Repeat
steps (a) and (b). (NOTE: An alternate test is to turn the
body on end and allow gravity to pull the spool from the body
into your hand. If the spool does not move under the
influence of gravity, the spool is sticking inside the body
bore.) If the spool binding persists, replace the valve.
Check the feel of the spool. If side movement of the spool
can be felt within the body bore, the body/spool clearances
are excessive. A new spool and body have a select fit of
approximately 0.0002-0.0003 inch. Body/spool clearances in
excess of this value may still work satisfactory in your
system; however, limitations are dependant on how much
leakage your system can tolerate. Normally, excessive
body/spool clearances dictate replacing the entire valve.
NOTE
If a new spool is installed into a new or used body, break
the feathered edges of the spool balancing grooves
with a three or four cornered India stone. See Figure
22. Lightly polish the spool with #500 grit paper. Wash
the spool in clean solvent. Repeat steps (a) and (b).
NOTE
The following step (6) pertains to detented “N” pilot
valves only.
6. Check the detent by moving the push pin through the
detent. A steady frictional force should be observed. If the
detent force is weak (less than 1 lb.), replace the detent
subassembly. The detent should be assembled on the
polished end of the spool (DG4S4-01*N-W-51) models.
7. Perform a continuity test on each solenoid coil S/A.
Resistance values will vary with the voltage rating of the coil.
Refer to Table 7. This test is superficial, but a more rigorous
test requires special equipment. If the coil seems to be
burned or extreme heat is encountered during operation, the
coil may be shorted. Make sure the correct voltage is being
applied to the coil.