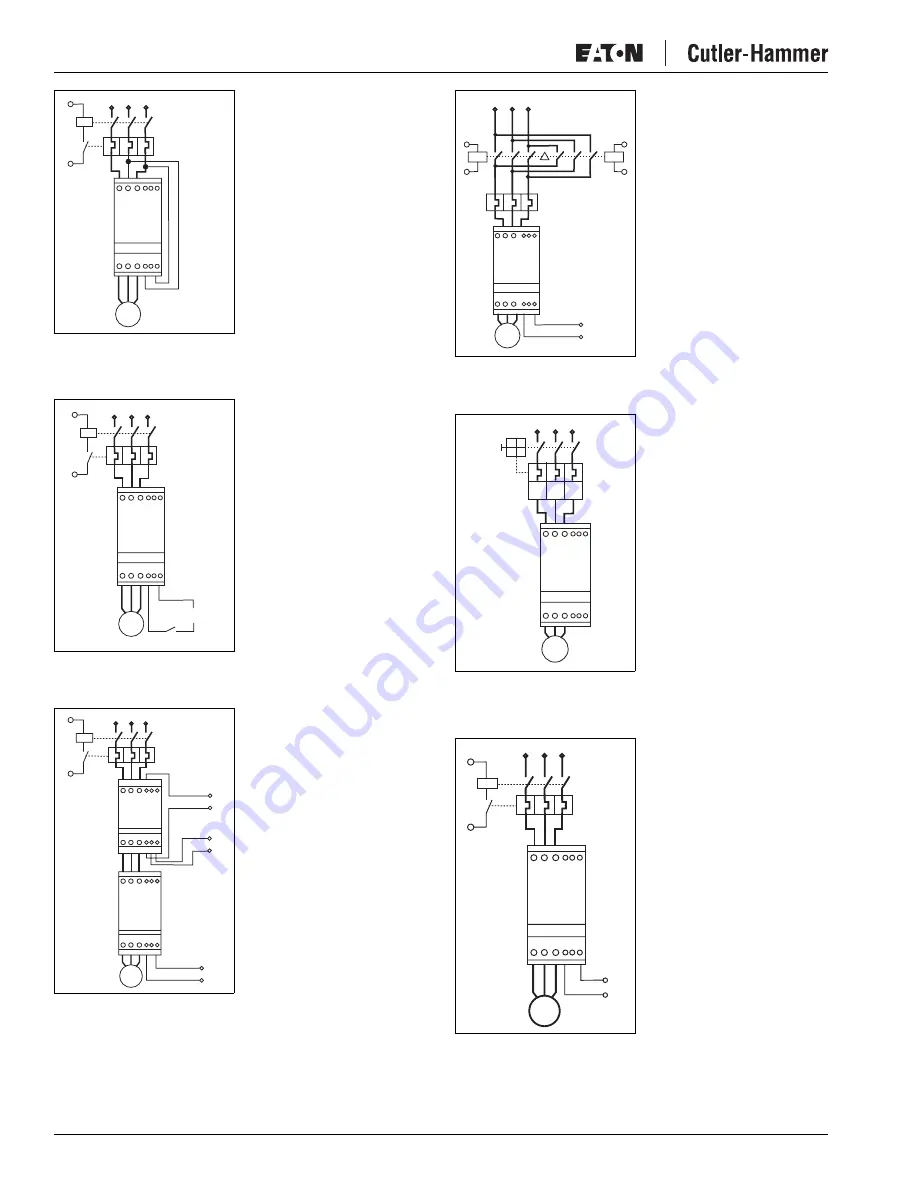
Pub 49440
Effective 01/02
4
Using Line Voltage to
Control S701
When the contactor C1 is
switched to the ON state, the
motor controller will soft start
the motor according to the set-
tings of the ramp-up time and
initial torque adjustments.
When the contactor C1 is
switched to the OFF state, the
motor will be switched off
instantaneously.
In this application, the contac-
tor will have no load during
making operation.
The contactor will carry and
break the nominal motor cur-
rent. Maximum voltage in this
application is 300V AC.
Separate Input Signal to
S701
When the control input is
switched to the ON state
(S closed), the motor control-
ler will soft start the motor
according to the settings of the
ramp-up time and initial torque
adjustments.
When the control input is
switched to the OFF state
(S open), the motor will be
switched off instantaneously
only if the ramp-down time is
adjusted to 0.
With any other setting, the
motor will be soft stopped
according to the settings of the
ramp-down time adjustment.
Soft Reversing of
Motors up to 5 hp/4 kW
A soft reversing of a motor can
easily be achieved by con-
necting a reversing relay to
the soft starter.
The reversing contactor type
S511 will determine the direc-
tion of rotation forward or
reverse and the soft start type
S701 will perform soft-starting
and soft-stopping of the motor.
If soft stop is not required, the
application can be simplified
by connecting the control cir-
cuit of the soft start controller
to the main terminals as
shown in
Figure 6
. A delay of
approximately 0.5 seconds
between forward and reverse
control signal must be
allowed to avoid influence from the voltage generated by the
motor during turnoff.
Reversing of Motors
Up to 15 hp/11 kW
A soft-reversing of motors can
easily be achieved when the
motor load exceeds 5 hp/4 kW
by connecting a mechanical
reversing contactor to the soft
start controller.
The reversing contactor will
determine the direction of
rotation forward or reverse
and the soft start type S701
will perform soft-starting and
soft-stopping of the motor.
Overload Protection with
Manual Starter
Overload protection of the
motor is easily achieved by
installing a manual motor
starter on the supply side of
the motor.
The manual motor starter pro-
vides means for padlocking
and the necessary clearance
for use as a circuit isolator
according to EN60204-1.
Adjust the current on the man-
ual motor starter according to
the rated nominal current of
the motor.
Overload Protection with
Mechanical Starter
Overload protection of the
motor is easily achieved by
installing a mechanical starter
on the supply side of the soft
start controller.
The overload provides the
necessary motor protection for
an overload condition.
A short circuit protective
device is required to meet UL
requirements.
S701
24-300V
L1 L2 L3
T1 T2 T3
A1 A2
L1
L2
L3
M
C1
Figure 6.
Line Controlled
Soft Start *
S701
Control Voltage
24 - 300 V
L1 L2 L3
T1 T2 T3
A1 A2
L1
L2
L3
M
S
C1
Figure 7.
Input Controlled
Soft Start *
Run / Stop
Reverse
Forward
S511
S701
L1
L2
L3
M
L1 L2 L3
T1 T2 T3
A1 A2
L1 L2 L3
T1 T2 T3
A2 A3 A4
C1
A1
Figure 8.
Soft Reversing of
Motors*
S701
Run / Stop
T1 T2 T3
A1 A2
L1
L2
L3
FWD
REV
A1
L1 L2 L3
M
Figure 9.
Reversing of
Motors *
S701
L1 L2 L3
T1 T2 T3
A1 A2
I>
I>
I>
L1
L2
L3
M
Figure 10.
Overload
Protection with Manual Motor
Starter *
S701
Run / Stop
L1 L2 L3
T1 T2 T3
A1 A2
M
L1
L2
L3
C1
Figure 11.
Overload
Protection with Mechanical
Starter *
*
Use specified backup fuse or circuit breaker.