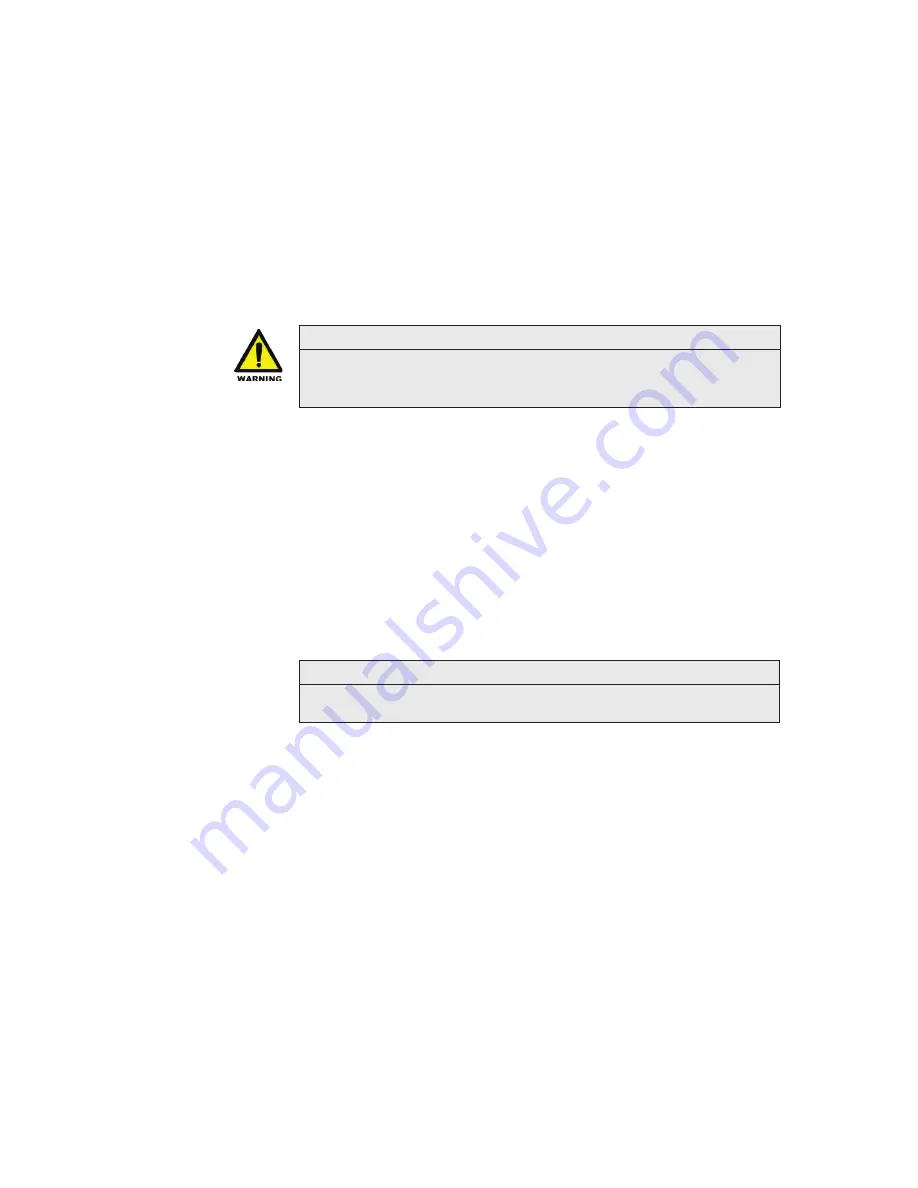
DRAFT - 11 December 2014
22
DRAFT - 11 December 2014
DRAFT - 11 December 2014
INM MTL4850_54 Rev4
5
MODULES
5.1 MTL4850/54 – installation
Place the module over its marked connector in the position on the backplane, press it
evenly and fully
onto the backplane before tightening the two (captive) mounting screws. All safe-area circuit and
power connections are made through this connector, so it must be seated properly on the backplane.
If the module does not operate correctly, the module mounting should be the first point to check.
5.2 Isolator modules (if used)
If the backplane accommodates isolators, refer to instruction manual INM4500/4600 for
information on wiring hazardous-area connectors for MTL4500 Series isolators.
Position each isolator module in its appropriate location on the backplane. Ensure that the
module is not tilted, which could damage the connector pins, then press it carefully to the
backplane. All safe-area circuit and power connections are made through this connector.
WARNING!
Personnel that carry out connection of wiring to or from hazardous areas must be
correctly trained. Unless this work is done correctly, it can endanger the lives of site
workers and seriously damage equipment.
Hazardous area wiring is terminated on the isolator modules using the blue terminals
provided on them. For full information on the wiring of MTL4500 isolators consult MTL
publication INM4500/4600.
5.3 MTL4850/54 module parameters
5.3.1
Setting and configuration
The speed for the RS485 interface is autodetected within the range 38400, 19200, 9600 or 1200 baud.
5.3.2
HART address
Up to 63 MTL4850 / 54 multiplexer modules can be connected to a single maintenance workstation.
Each multiplexer must have a unique address, which is set using the DIP switches located beside
the module on the circuit board. The address switches are binary coded and the address is set by
constructing the required number from the switch options provided, i.e. 1, 2, 4, 8, 16 and 32. For
example, address number 29 would be set by putting switches 16, 8, 4 and 1 in the ON position (16 + 8
+ 4 + 1 = 29).
NOTE
the HMP-HM64 can only be set to
even
numbers as the other module adopts the
odd
addresses. See Section 4.2.5.
5.3.3
Operation at power-up
The MTL4850/54 system is controlled by a host computer running instrument management
software. Although the software is needed to operate the system, some checks can be made on the
correct functioning of the hardware in isolation. These checks are made by observing the operation
of the LEDs on top of the module.
5.3.3.1
Correct operation
At power on, the power (PWR) LED should light and the multiplexer should start to build, or
rebuild, an internal scan list of the HART loops connected to it. This will be indicated by a regular
flashing sequence (equal on and off duration) of the Fault LED. At the end of this process the
Fault LED should go OFF to indicate that it is now in its “running” state.
5.3.3.2
Problems
If problems occurred during this power up sequence the Fault LED will either emit short and
long flashes to indicate that it could not find any HART loops, or it will adopt a steady ON state to
indicate that a fault was detected and the process of building the list was halted.
The MTL4850/54 is delivered with the default of “scanning disabled”. In either case the instrument
maintenance software can be used to change the multiplexer’s scanning mode.
5.3.3.3
Scan list
Each loop connected to an MTL4850/54 is added to the scan list if a HART device is detected on
power up or if the instrument maintenance software resets the module. Loops can be added
individually or removed from the scan list using the “loop rebuild“ facility in the instrument
maintenance software.
5.3.3.4
Scanning enabled
The MTL4850/54 scans continuously round all loops on the scan list.