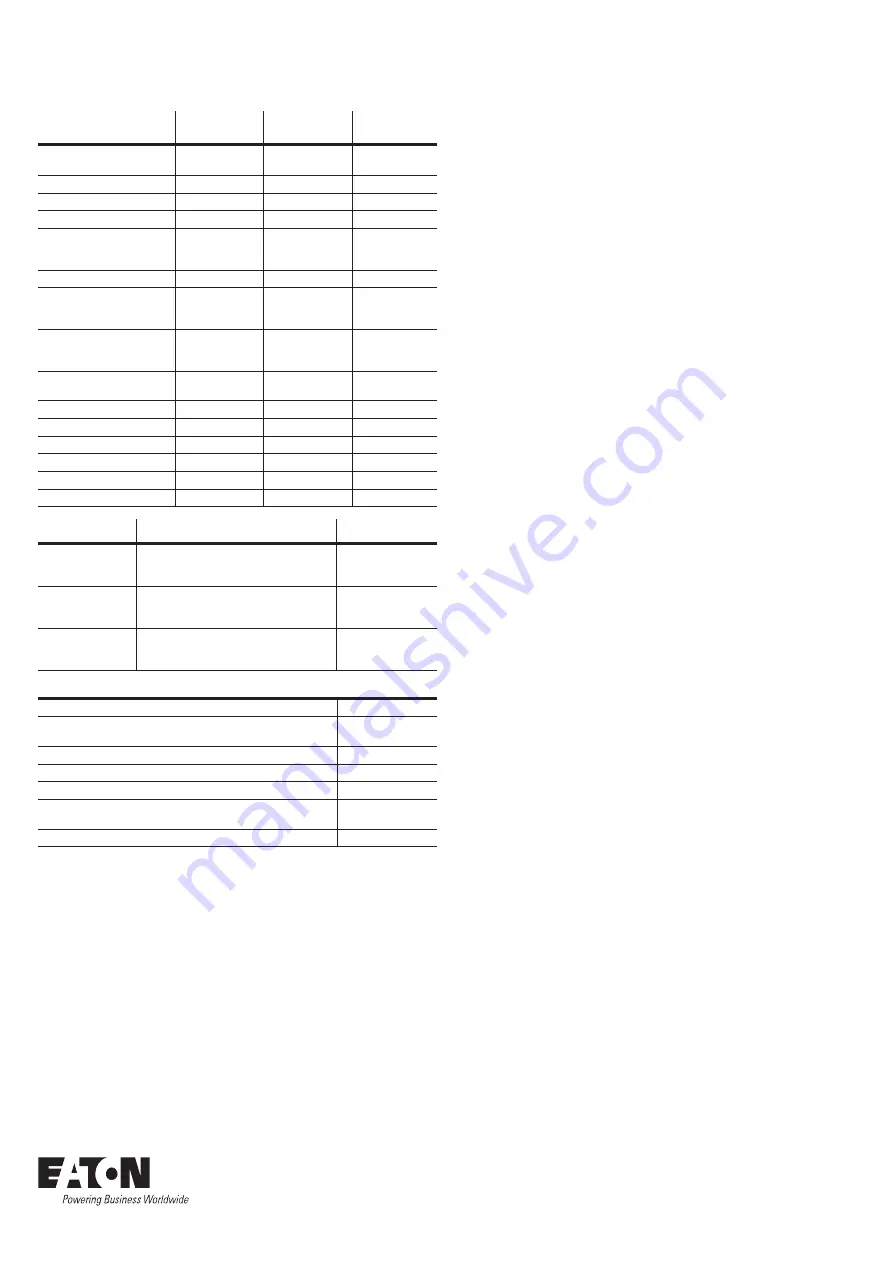
Technical Data
Effective April 2018
eaton
EMEA Headquarters
Route de la Longeraie 7
1110 Morges, Switzerland
Eaton Electrical Systems Ltd.
Wheatley Hall Road, Doncaster,
South Yorkshire, DN2 4NB,
United Kingdom
© 2018 Eaton
All Rights Reserved
Eaton is a registered trademark.
All trademarks are property
of their respective owners.
www.eaton.com
MAP820
FXN723
CAP320
MAH830
FXN725
CAH330
MAOH850
FXN722
CAPT340
Analogue addressable
Detector type
Photoelectric
Heat
Photo/Thermal
Operating voltage
18 to 30 Vdc
18 to 30 Vdc
18 to 30 Vdc
Standby current (max)
220μA
220μA
220μA
Alarm current (typ)
5mA
5mA
5mA
Ambient temperature (max)
60ºC
A1R 50ºC
BS 65°C
CS 80°C
50ºC
Ambient temperature (min)
-10ºC
-10ºC
-10ºC
Alarm temperature (static)
N/A
A1R 60ºC
BS 77°C
CS 90°C
60ºC
Heat detector class
–as defined by
EN54-5:2000
N/A
A1R, BS, CS
Control panel
selectable
A2S
Relative humidity
(non-condensing)
0 to 95%
0 to 95%
0 to 95%
Height (without base)
34mm
43mm
43mm
Height (with base)
47mm
56mm
56mm
Diameter (Base)
104mm
104mm
104mm
Weight (without base)
78g
78g
78g
Material
PC/ABS
PC/ABS
PC/ABS
Colour
White
White
White
Applicable standards
Declaration of
performance
MAP820
FXN723
CAP320
EN54-7: 2000 +A1: 2002 +A2: 2006
EN54-17: 2005
DoP0157
MAH830
FXN725
CAH330
EN54-5: 2000 +A1: 2002
EN54-17: 2005
DoP0156
MAOH850
FXN722
CAPT340
EN54-7: 2000 +A1: 2002 +A2: 2006
EN54-5:2000 +A1: 2002 Class A2S
EN54-17: 2005 CEA4021:2003
DoP0158
Short circuit isolation data (integral with each detector)
Total loop resistance for correct operation of short circuit isolator 80Ω (max)
Parallel fault resistance to be seen at the control panel for
isolators to open
200Ω (typ)
Continuous current allowable through isolator
700mA (max)
Isolator resistance in closed state
0.26Ω (max)
Leakage current into direct short circuit with isolator open
14mA (max)
Voltage at which isolator changes from open to closed or closed
to open state
3.8V to 11V
Maximum switching current of isolator
1.5A
Detector installation
•
Fit detector to mounting base and rotate clockwise until the
detector drops into place
•
Continue to rotate clockwise until the detector clicks and no further
rotation is possible
•
If the detectors are required to be locked into position, refer to the
mounting base installation instructions (see over leaf)
•
Smoke detectors are supplied fitted with dust covers for general
protection against airborne contaminates. These must be removed
from all detectors before the fire system is commissioned
•
NB. These dust covers do not provide adequate protection against
quantities of dust generated by building work, sanding etc.
Therefore, detectors should not be installed until this type of work
has been completed
Maintenance
Only minimal maintenance can be performed on this range of
detectors as they do not contain any site serviceable parts. The
frequency of maintenance will depend on the environment to which
the detector is exposed but should be at least annually. Dusty or
damp environments will demand more frequent maintenance.
•
Remove the detector from its mounting base
•
Use a vacuum cleaner to remove dust build up from around the
smoke entry apertures of a smoke detector, or from around
the heat sensing element of a heat detector
•
For smoke detectors, visually inspect the insect mesh for
blockages. If these can not be cleared by vacuuming, the
detector must be replaced
•
Re-fit detector to its mounting base and test as described above
•
Detectors that fail the testing procedure must be replaced
Each of the detectors in his range contain an integral short circuit
isolator, which operates between the -VE COM IN terminal and the
-VE COM OUT terminal (terminals 1 & 2; see base wiring diagram
overleaf). The isolator operates in conjunction with a compatible
addressable control panel when a low parallel resistance fault of
typically 200Ω is presented between the +VE and -VE of
the loop wiring.
Testing
All detectors must be tested following installation or routine service
and maintenance. It is recommended that these tests are carried out
by a competent person. Authorised personnel must be informed that
the fire system will be temporarily out of service before commencing
testing. To prevent unwanted alarms, ensure that the control panel
is in the ‘One Man Walk Test’ mode. When all tests are complete,
re-enable the previously disabled zones and notify authorised
personnel that the system is operational.
Smoke Detectors; Photo/Thermal Detector
•
Subject the detector to be tested to a controlled amount of an
approved synthetic smoke aerosol via a smoke detector test
pole. Suitable products are available for example, from No Climb
Products Ltd
•
Check that the red LED on the detector lights within 30 seconds
and the appropriate alarm address indication is displayed on the
control panel. If an optional remote LED is fitted, check that this
also lights
•
Ensure that the control panel activates into alarm
•
The control panel will automatically reset after a few seconds
•
This procedure will test the smoke sensing circuitry of the Photo/
Thermal Detector
Heat Detectors; Photo/Thermal Detector
•
Using a heat gun or hair dryer capable of generating temperatures
of up to 95°C, direct the heat source towards the heat sensing
elements, visible through the side of the outer cover, from a
distance of 15 to 30cm. Care should be taken not to allow the
plastic surface temperature to exceed 110°C otherwise damage
may occur
•
When the temperature reaches the ‘Alarm Temperature’ (see
Specifications above), check that the red LED on the detector lights
and the appropriate alarm address indication is displayed on the
control panel. If an optional remote LED is fitted, check that this
also lights
•
Ensure that the control panel activates into alarm
•
The control panel will automatically reset after a few seconds
•
This procedure will test the heat sensing circuitry of the Photo/
Thermal Detector