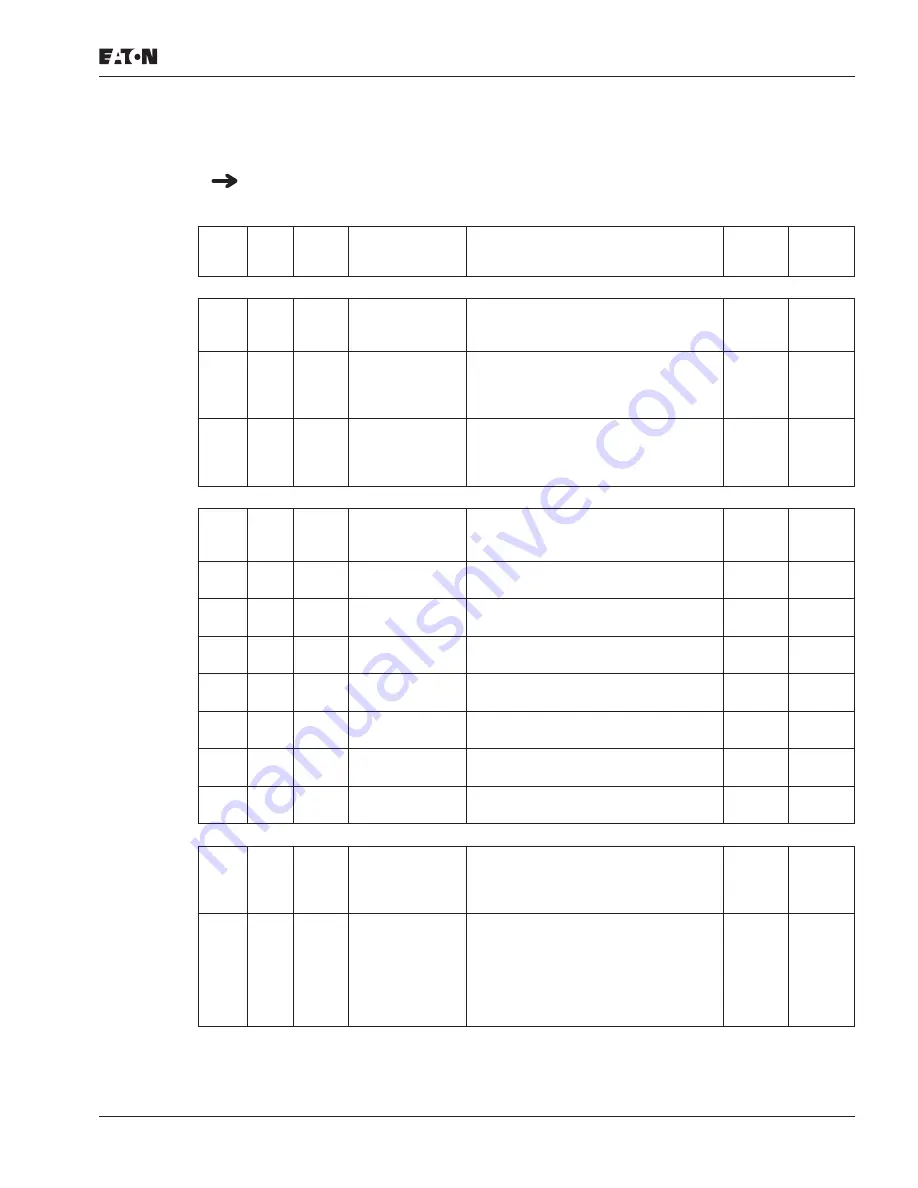
M-Max Series adjustable frequency drive
MN04020002E
For more information visit:
www.eaton.com
33
February 2010
All Parameters
Table 11: All Parameters
When first switching on or after activating the default settings (S4.2 = 1) parameter P1.1
must be set to 0 for access to all parameters.
PNU
ID
Access
Right
RUN
Designation
Value Range
Factory
Setting
User
Setting
Parameter Selection
P1.1
115
✓
Parameter range 0 = All parameters
1 = Only quick configuration
parameters
1
P1.2
540
—
Application
0 = Basic
1 = Pump drive
2 = Fan drive
3 = High starting torque
0
P1.3
1472
—
Factory setting
(WE),
Country-specific
(enabled and visible only in the quick
start wizard)
0 = EU (50 Hz-based defaults)
1 = USA (60 Hz-based defaults)
0
Analog Input
P2.1
379
✓
AI1, Signal range (DIP switch S2)
0 = 0V/0 mA
1 = 2V/4 mA
0
P2.2
380
✓
AI1, minimum
value
–100.00 – 100.00%
0
P2.3
381
✓
AI1, maximum
value
–100.00 – 100.00%
100
P2.4
378
✓
AI1, filter time
constant
0.0 – 10.0s
0.1
P2.5
390
✓
AI2, Signal range (DIP switch S3)
Like P2.1
3
P2.6
391
✓
AI2, minimum
value
–100.00 – 100.00%
0
P2.7
392
✓
AI2, maximum
value
–100.00 – 100.00%
100
P2.8
389
✓
AI2, filter time
constant
0.0 – 10.0s
0.1
Digital Input
P3.1
300
✓
Start/stop logic
0 = DI1 (FWD), DI2 (REV)
1 = DI1 (START), DI2 (REVERSE)
2 = DI1 (Start pulse), DI2 (Stop pulse)
3 = DI1 (FWD), DI2 (REV) and REAF
3
P3.2
403
✓
Start signal
0 = Deactivated
1 = DI1
2 = DI2
3 = DI3
4 = DI4
5 = DI5
6 = DI6
1