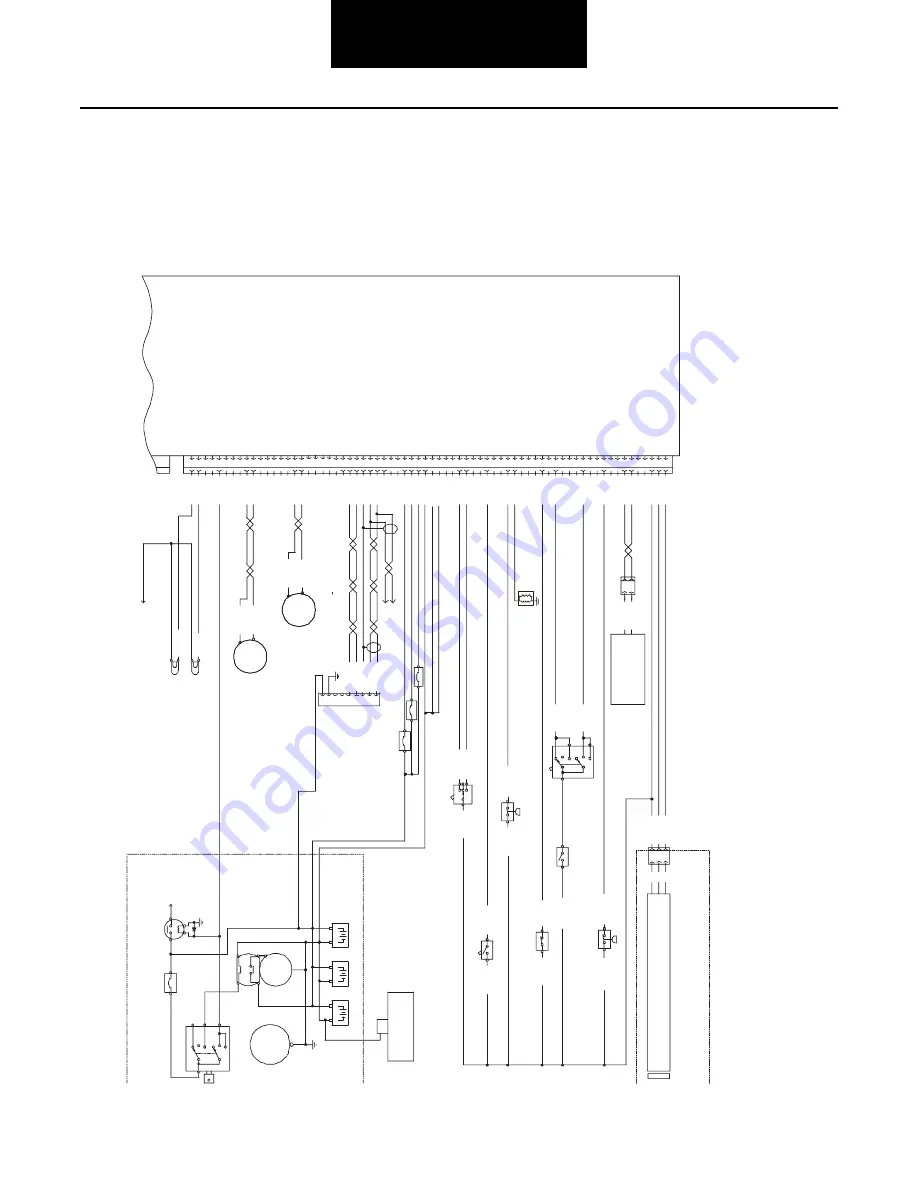
29
Appendix
Wiring Diagrams
Caterpillar
C11, C13, C15, and C18 OEM Diagrams (2003)
C977-BU
E716-GY
G879-OR
C983-WH
C984-YL
CLUTCH PEDAL POSITION SWITCH
100mA
100mA
INPUT #11 (NOTE L)
INPUT #15 POSITIVE
RETARDER SOLENOID LOW/HI SWITCH
+5V
ENGINE COOLANT LEVEL NORMAL (NOTE G)
ENGINE COOLANT LEVEL LOW (NOTE G)
RETARDER SOLENOID MED/HI SWITCH
INPUT #15 NEGATIVE
VEHICLE SPEED IN POSITIVE (NOTE F)
VEHICLE SPEED IN NEGATIVE
INPUT #8 (NOTE L)
14 AWG GXL
14 AWG GXL
14 AWG GXL
ACCELERATOR PEDAL SENSOR/SWITCH SENSOR COMMO
+8V
ACCELERATOR PEDAL POSITION
22
63
23
2
49
54
41
24
E971-GN
G834-PU
62
64
61
0.3A CURRENT LIMIT
0.3A CURRENT LIMIT
1
2
40
51
55
NOTE C: "SINGLE" WINDING MAGNETIC PICKUP SENSOR RECOMMENDED
NOTE B: FOR SPEEDOMETERS OR TACHOMETERS WITH A SINGLE SIGNAL INPUT
TERMINAL, EITHER ONE OF THE TWO SIGNAL OUTPUT LINES FROM
THE ECM CAN BE USED. LEAVE THE REMAINING LINE DISCONNECTED,
DO NOT CONNECT TO GROUND
5
4
66
25
32
33
69
68
VEHICLE HARNESS CONNECTOR
P2 J2
H795-PK
C985-BU
C986-BR
L994-YL
659-PK
K998-BU
G880-PK
J906-BR
G881-BU
G882-WH
SERVICE BRAKE PEDAL POSITION SWITCH
INPUT #7 (NOTE L)
45
C992-PU
INPUT SENSOR COMMON #1
INPUT #5 (NOTE L)
INPUT #6 (NOTE L)
18
47
6
46
L901-GY
G842-GY
G843-OR
G844-PK
C974-PU
C973-GN
E718-PK
E991-GY
G836-WH
CRUISE CONTROL ON/OFF SWITCH
INPUT #3 (NOTE L)
INPUT #4 (NOTE L)
59
60
7
C975-WH
K982-YL
G841-GN
SET
RESUME
INPUT #1 (NOTE L)
INPUT #2 (NOTE L)
35
44
56
58
C978-BR
C979-OR
K999-GN
K980-PK
P1 J1
G835-OR
G808-BU
G809-GN
G845-PU
J1587 DATA LINK NEGATIVE
J1587 DATA LINK POSITIVE
J1939 DATA LINK SHIELD (NOTE K & NOTE M)
J1939 DATA LINK NEGATIVE (NOTE K & NOTE M)
J1939 DATA LINK POSITIVE (NOTE K & NOTE M)
UNSWBATTERY (NOTE D)
UNSWBATTERY (NOTE D)
-BATTERY
INPUT #9
INPUT #10
INPUT SENSOR COMMON #2
INPUT #14
52
53
65
67
27
26
3
17
E717-GN
101-RD
101-RD
229-BK
G933-YL
C453-YL
993-BR
F713-OR
9
8
42
34
50
1
14
48
TACHOMETER POSITIVE
TACHOMETER NEGATIVE
38
39
57
450-YL
451-BR
SPEEDOMETER POSITIVE
SPEEDOMETER NEGATIVE
OUTPUT #2
OUTPUT #3
OUTPUT #4
36
37
10
12
13
15
16
28
29
30
31
70
+/- 5 VOLTS
CHECK ENGINE LAMP
WARNING LAMP
OUTPUT #1
OUTPUT #9
IGNITION KEY SWITCH
INPUT #12
INPUT #13
E793-BU
E794-YL
A249-BK
K990-GN
K900-YL
SPEEDOMETER
NOTE E
NOTE H
NOTE B
ACCELERATOR PEDAL
POSITION SENSOR
40mA
5mA
BK
RD
WH
J403 P403
ACCELERATOR PEDAL SENSOR/SWITCH SENSOR COMMON
+8 V
ACCELERATOR PEDAL POSITION
B
A
C
H795-PK
H795-PK
A/C HIGH PRESS. SWITCH N/C
E971-GN
450-YL
451-BR
SIGNAL-
NOTE B
TACHOMETER
NOTE E
NOTE H
E793-BU
E794-YL
10A
PASSIVE
MAGNETIC
VEHICLE SPEED
SENSOR
G808-BU
G809-GN
H795-PK
H795-PK
E717-GN
E716-GY
SET/RESUME
NOTE J
NOTE D
NOTE D
ENGINE
BLOCK
COMPONENTS WITHIN THIS AREA ARE CATERPILLAR PROVIDED
CLUTCH PEDAL POSITION N/C
SERVICE BRAKE PEDAL POSITION N/C
(PEDAL RELEASED POSITION)
6.5mA NOTE H
CRUISE CONTROL ON/OFF
6.5mA
6.5mA
6.5mA
6.5mA
6.5mA
CHECK ENGINE LAMP
WARNING LAMP
+BATTERY
-BATTERY
J1587 D
LINK NEGATIVEATA
J1587 D
LINK POSITIVEATA
J1939 DATA LINK Positive
J1939 DATA LINK Shield
J1939 DATA LINK Negative
D
H795-PK
G
C
F
SAE J1939/13 OFF-BOARD
DIAGNOSTIC CONNECTOR
B
A
TO VEHICLE
COMPONENTS
CIRCUITS WITHIN THIS AREA ARE RECOMMENDATIONS
SIGNAL-
START
ON
OFF
B
S
C
R
H795-PK
45.5mA MAX
G
S
MTR
BAT
STARTER
MOTOR
(12V)
BATTERY 2
N/O
RELAY
H795-PK
C985-BU
C986-BR
C978-BR
C979-OR
C977-BU
C992-PU
C975-WH
C973-GN
C974-PU
KEY SWITCH
659-PK
GROUND
L994-YL
ALTERNATOR
-
12V
+
-
12V
++
12V
-
BATTERY 3
BATTERY 1
NOTE F: IF AN ELECTRONIC SIGNAL IS PROVIDED IN PLACE OF A PASSIVE
MAGNETIC SENSOR, CONNECT THE ELECTRONIC SIGNAL INPUT TO
THE +SIGNAL PIN, THE -SIGNAL PIN SHOULD NOT BE CONNECTED
OR GROUNDED WITH ELECTRONIC SIGNAL INPUTS
NOTE D: THESE CONNECTIONS ARE UNSWITCHED, DIRECT CONNECTION
T
O
THE BATTERY I
S
N
O
T RE
QU
IR
E
NOTE C
NOTE F
LO
MED
HI
ENGINE RETARDER
SOLENOID SELECTOR SWITCH
NOTE H
NOTE E: THE ECM SPEEDOMETER AND TACHOMETER OUTPUT SIGNAL LINE
VOLTAGES ARE ZERO-CROSSING SQUARE WAVES. THE SPEEDOMETER
SIGNALS AT J1-37 AND J1-36 ARE COMPLEMENTS OF EACH OTHER.
THE TACHOMETER SIGNALS AT J1-38 AND J1-39 ARE COMPLEMENTS
OF EACH OTHER. MAXIMUM SIGNAL AMPLITUDE OF J1-36, J1-37,
J1-38, AND J1-39 IS +/-
10 VOLTS. AMPLITUDE WILL BE
OR GREATER IF LOAD CURRENT IS LESS THAN 4mA.
(PEDAL RELEASED POSITION)
HI
TO +BATTERY
MED
LO
RETARDER SOLENOID ON/OFF SWITCH
13mA
COOLING FAN SOLENOID
OUTPUT #5
OUTPUT #6
OUTPUT #7
OUTPUT #8
11
19
20
21
G837-YL
G838-BR
G839-BU
G840-PU
229-BK
-BATTERY
J
H
E
A249-BK
K990-GN
K900-YL
43
14 AWG GXL
TO CHASSIS J1939 DATA LINK
229-BK
14 AWG GXL
101-RD
-BATTERY
UNSWBATTERY (NOTE D)
14 AWG GXL
14 AWG GXL
10A
10A