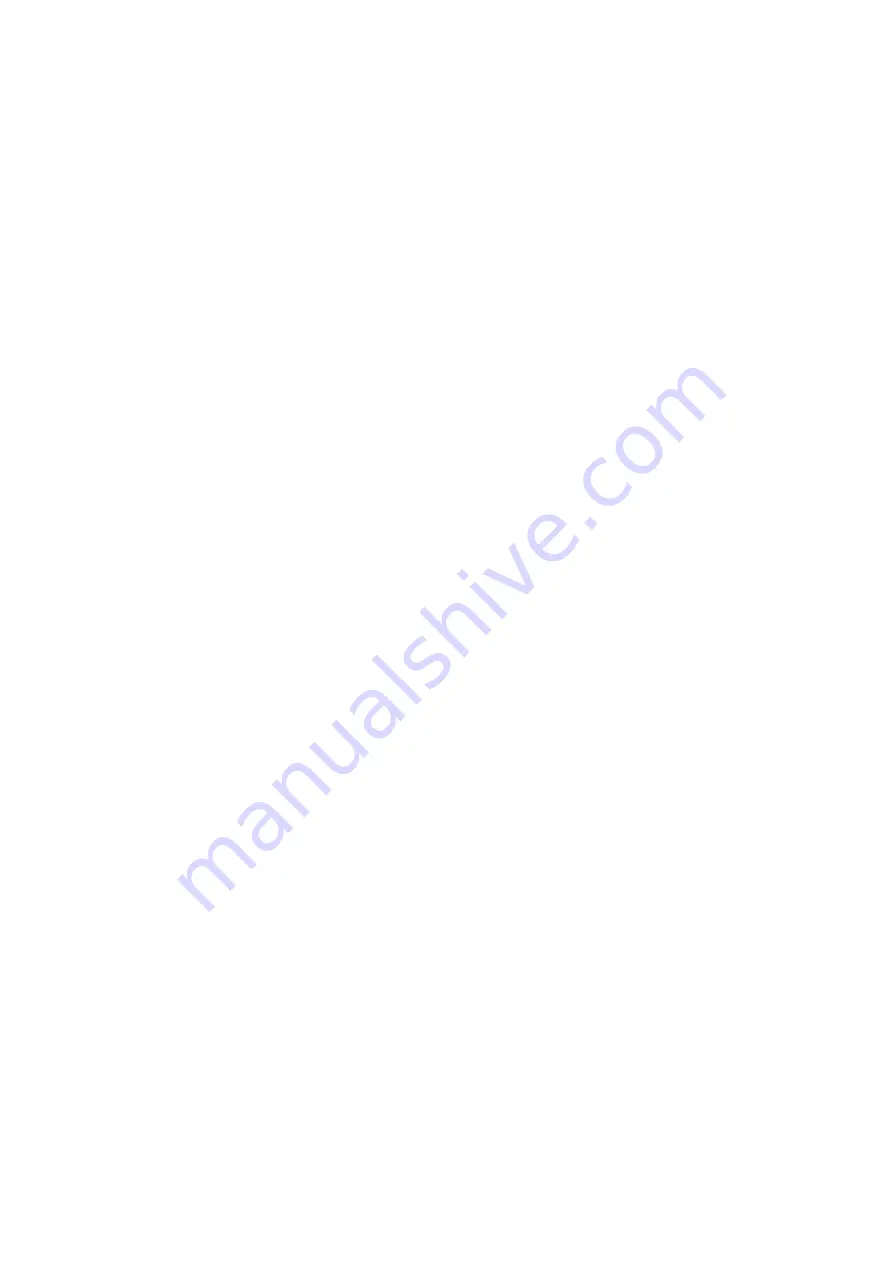
7 Startup
ESR5-VE3-42
07/20 MN049003EN
Eaton.com
11
7 Startup
▶
Apply the nominal input voltage U
N
(24
V
DC) at terminal blocks
A1/A2.
→
The
Power
LED lights up.
▶
Apply a 24 V DC voltage at input K1/K2.
→
Both relays are activated.
→
The LEDs light up and the contacts for enabling current paths
27-28, 37-38, 47-48, and 57-58 close.
→
Alarm contacts 15-16 and 65-66 open.
▶
Switch off the voltage at input K1/K2.
→
The enable contacts open and the alarm contacts close after the
set time has elapsed.
→
For additional connection examples, see
→
section 12, “Con-
nection Example”, page 16.