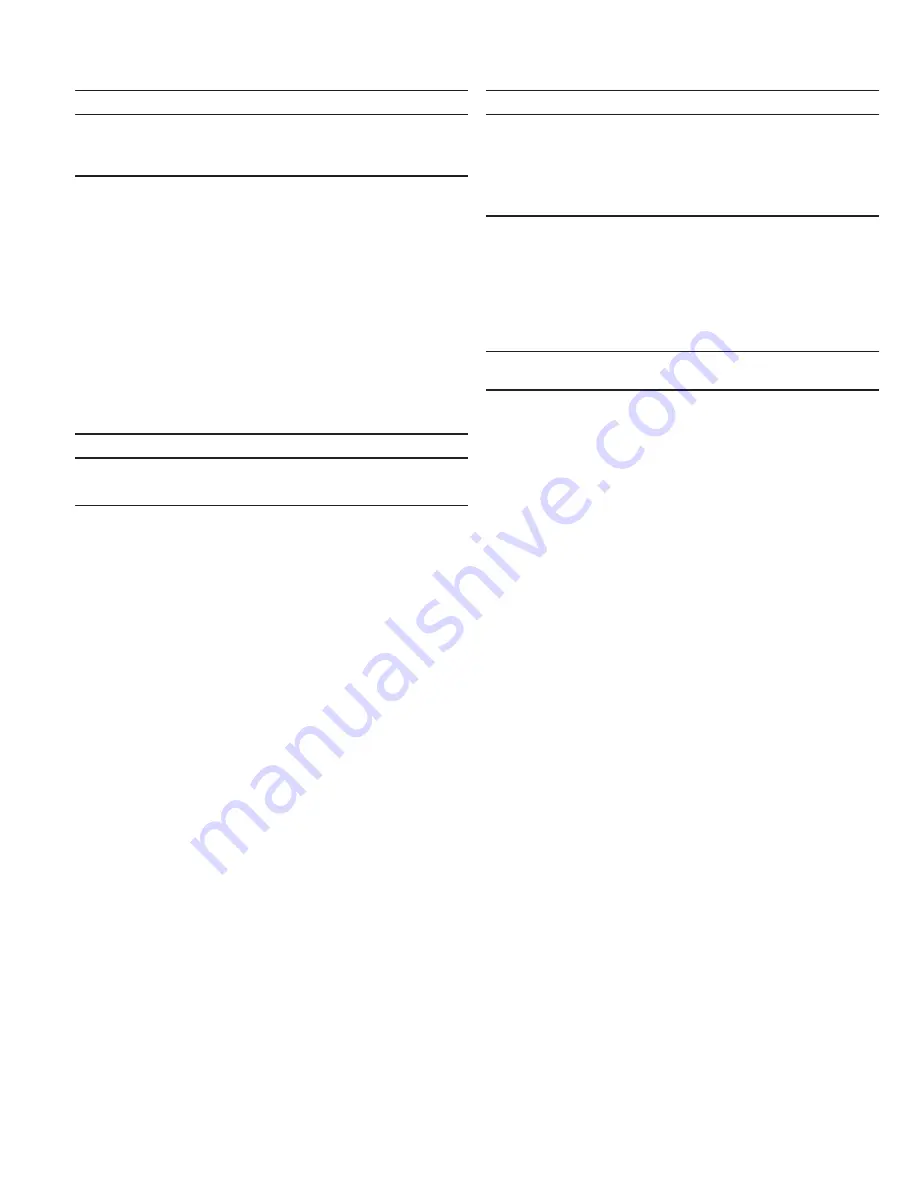
15
Instruction Book IB182942EN May 2019 www.eaton.com
DST-2-VR
+
VR-Series
+
Replacement Circuit Breaker
DANGER
FAILURE TO REPLACE THE VACUUM INTERRUPTER ASSEMBLY WHEN
INDICATED BY THE CONTACT EROSION INDICATOR COULD CAUSE THE
CIRCUIT BREAKER TO FAIL, LEADING TO DEATH, SEVERE PERSONAL
INJURY, EQUIPMENT DAMAGE AND/OR IMPROPER OPERATION.
4.1.3 CONTACT WIPE AND STROKE
The circuit breaker mechanism provides a fixed amount of motion
to the operating rods connected to the moving stem of the vacuum
interrupter. The first portion of the motion, the stroke, is used to
close the vacuum interrupter contacts; the remainder of that motion,
the wipe, is used to further compress the pre-loaded wipe spring.
Contact stroke and wipe are related; contact wipe is the indication
of the force holding the vacuum interrupter contacts closed as well
as the energy available to hammer the contacts open with sufficient
speed for interruption. Stroke is the gap between the stationary and
moving contact of the vacuum interrupter when the circuit breaker
is open. As the stroke increases due to contact erosion inside the
vacuum interrupter, the wipe decreases. Although these changes are
taking place as operations accumulate on the vacuum interrupter,
field adjustment of the wipe or stroke are not necessary during the
lifetime of the vacuum interrupter.
WARNING
THERE IS NO PROVISION FOR IN-SERVICE ADJUSTMENTS OF CONTACT
WIPE AND STROKE. ALL SUCH ADJUSTMENTS ARE FACTORY SET AND
SHOULD NOT BE ATTEMPTED IN THE FIELD.
4.2 LINE AND LOAD CONDUCTOR ASSEMBLIES
Multiple finger type primary disconnecting contacts at the ends of
the conductors provide means for connecting and disconnecting
the circuit breaker to the bus terminals in the circuit breaker
compartment of the metal-clad switchgear.
4.3 STORED ENERGY MECHANISM
The spring-type stored energy operating mechanism is mounted
on the circuit breaker frame and in the front of the circuit breaker.
Manual closing and opening controls are at the front cover (Figure
Set 3.3). They are accessible while the circuit breaker is in any of its
basic installation positions. (See Section 5 in this manual)
The mechanism stores the closing energy by charging the closing
springs. Spring charging is automatically accomplished when control
power is applied to the circuit breaker secondary disconnect contact.
When released, the stored energy closes the circuit breaker, charges
the wipe and resets the opening springs. The mechanism may rest
in any one of the four positions shown in Figure 4.8 as follows:
a. Circuit Breaker open, closing springs discharged.
b. Circuit Breaker open, closing springs charged.
c. Circuit Breaker closed, closing springs discharged.
d. Circuit Breaker closed, closing springs charged.
The mechanism is a mechanically “trip-free” design. Trip-free is
defined in Section 4.3.4 (Trip-Free Operation).
In normal operation the closing spring is charged by the spring
charging motor, and the circuit breaker is closed electrically by the
switchgear control circuit signal to energize the spring release coil.
Tripping is caused by energizing the trip coil through the control
circuit.
For maintenance inspection purposes the closing springs can be
charged manually by using the maintenance tool and the circuit
breaker can be closed and tripped by pushing the “Push to Close”
and “Push to Open” operators on the front cover.
DANGER
KEEP HANDS AND FINGERS AWAY FROM CIRCUIT BREAKER’S INTERNAL
PARTS WHILE THE CIRCUIT BREAKER CONTACTS ARE CLOSED OR THE
CLOSING SPRINGS ARE CHARGED. THE CIRCUIT BREAKER CONTACTS
MAY OPEN OR THE CLOSING SPRINGS DISCHARGE CAUSING CRUSHING
INJURY. DISCHARGE THE SPRINGS AND OPEN THE CIRCUIT BREAKER
BEFORE PERFORMING ANY MAINTENANCE, INSPECTION OR REPAIR ON
THE CIRCUIT BREAKER.
THE DESIGN OF THIS CIRCUIT BREAKER ALLOWS MECHANICAL CLOSING
AND TRIPPING OF THE CIRCUIT BREAKER WHILE IT IS IN THE ‘CONNECT’
POSITION. HOWEVER, THE CIRCUIT BREAKER SHOULD BE CLOSED
MECHANICALLY ONLY IF THERE IS POSITIVE VERIFICATION THAT LOAD
SIDE CONDITIONS PERMIT. IT IS RECOMMENDED THAT CLOSING THE
CIRCUIT BREAKER IN THE ‘CONNECT’ POSITION ALWAYS BE DONE WITH
THE CUBICLE DOOR CLOSED. FAILURE TO FOLLOW THESE DIRECTIONS
MAY CAUSE DEATH, SEVERE PERSONAL INJURY, EQUIPMENT DAMAGE
AND/OR IMPROPER OPERATION.
ELECTRICAL TRIPPING CAN BE VERIFIED WHEN THE CIRCUIT BREAKER IS
IN THE ‘DISCONNECT / TEST’ POSITION.
4.3.1 CLOSING SPRING CHARGING
Figure 4.7 shows schematic section views of the spring charging
parts of the stored energy mechanism.
The major component of the mechanism is a cam shaft assembly
which consists of a shaft to which are attached two closing spring
cranks (one on each end), the closing cam, drive plate, and a free-
wheeling ratchet wheel.
The ratchet wheel (6) is actuated by an oscillating ratchet lever
(12) and drive pawl (10) driven by the motor eccentric cam. As the
ratchet wheel rotates, it pushes the drive plates which in turn rotate
the closing spring cranks and the closing cam on the cam shaft.
The motor will continue to run until the limit switch “LS” contact
disconnects the motor.
The closing spring cranks have spring ends connected to them,
which are in turn coupled to the closing springs. As the cranks
rotate, the closing springs get charged.
The closing springs are completely charged, when the spring cranks
go over dead center and the closing stop roller (9) comes against the
spring release latch (1). The closing springs are now held in the fully
charged position.
The closing springs may also be charged manually as follows: Insert
the end of the maintenance tool into the manual charge socket
opening and charge the closing springs by moving the handle up
and down the full range of motion. When charging is complete the
ratchet will no longer advance and the spring charged / discharged
indicator displays ‘Charged’. (Figure Set 3.3). Any further motion of
the maintenance tool will not result into advance of charging.
4.3.2 CLOSING OPERATION
Figure 4.8 shows the positions of the closing cam and tripping
linkage for four different operational states. In Figure 4.8.a the
circuit breaker is open and the closing springs are not charged. In
this state, the trip latch (8) is disengaged from the trip “D” shaft (9)
(unlatched). After the closing springs become charged, the trip latch
snaps into the fully reset or latched position (Figure 4.8.b)
When the spring release clapper (Figure 4.7, Item 13) moves into the
face of the spring release coil (electrically or manually), the lower
portion of the clapper pushes the spring release latch (1) downward.
When the spring release latch moves, the cam shaft assembly is
free to rotate. The force of the closing cam (Figure 4.8.b, Item 5),
moving the main link (2), rotating the pole shaft (4) (which charges
the opening spring). This moves the three operating rods (3), closes
the main contacts and charges the contact loading springs (not
shown). The operational state immediately after the main contacts
close but before the spring charging motor recharges the closing
springs is illustrated in Figure 4.8.c. Interference of the trip “D” shaft
with the trip latch prevents the linkage from collapsing, and holds
the circuit breaker closed.