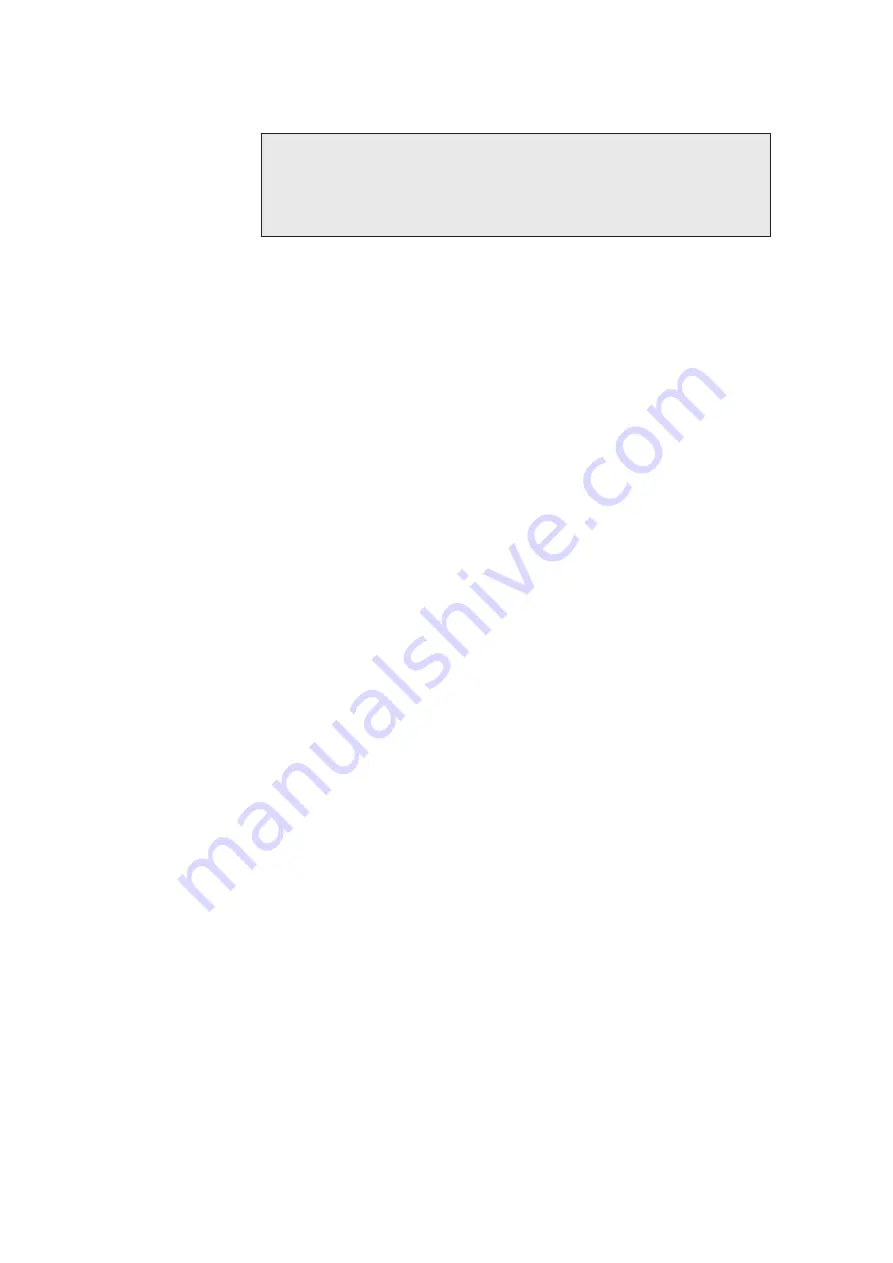
10
INM MTL 130-0186 Rev 8
5
CALIBRATION
CAUTION
Various procedures associated with calibration maintenance affect the outputs of the
instrument. Any of these outputs that are being used for control (or the associated control
loop) should be disabled before commencing.
5.1 Calibration overview
The Z230 is a very stable analyser with a drift rate of better than 2% of reading per month.
How often the calibration is checked or verified depends on the quality regime being operated
at the installation site. Typically monthly checks are found to be adequate.
It is preferable to use a calibration technique that starts by checking or verifying the response
of the analyser and only altering the calibration of the analyser if the errors are significant. The
readings may be verified by introducing a gas mixture of known concentration (calibration gas),
and checking that the reading is correct after allowing the system to stabilise.
A full calibration requires two standard gases to set two points that are equivalent to zero
and span. (See section 8 for a technical description of the sensor and how it works). The
gas calibration points are referred to as high(H) and low(L). It is usual, mainly because of
convenience, to use air as the “high” gas. The “low” gas should ideally have approximately the
same oxygen concentration as the normal sample.
As with most instruments of this type it is important to have a reasonable concentration
difference between the two calibration points. For the Z230 the recommended difference is
0.25 decades, i.e. LOG (H concentration/ L concentration) > ±0.25.
Because the most common high level gas is air, in order to maintain an adequate difference in
concentration, the instrument will not accept a “low” level calibration gas between 10% and 40%.
5.2 Calibration gases
Because the sensor operates at high temperature, the calibration gases must not contain
any flammable or reactive components. Typically this means using mixtures of oxygen with
nitrogen. Refer to section 3.3 for sample connection and handling precautions.
Instrument grade compressed air (i.e. clean, dry and oil free) is frequently the most convenient
gas to use for the upper concentration. Clean dry air has an oxygen content of 20.95%. If
moist air is used then its water content must be allowed for. For example air at 20°C and 70%
relative humidity (typical room air) contains 1.6% water. This will lower the oxygen content of
the air by dilution to 20.6%.
It is important that the analyser IS NOT ZEROED in the conventional manner using a
‘zero’ grade gas. This is because the notion of zero oxygen has no real meaning for
sensors of the type used in this analyser (See Section 7 – Technical description of sensor).
We recommend that the standard gas contains at least 5ppm oxygen and only ppb levels
of combustibles.