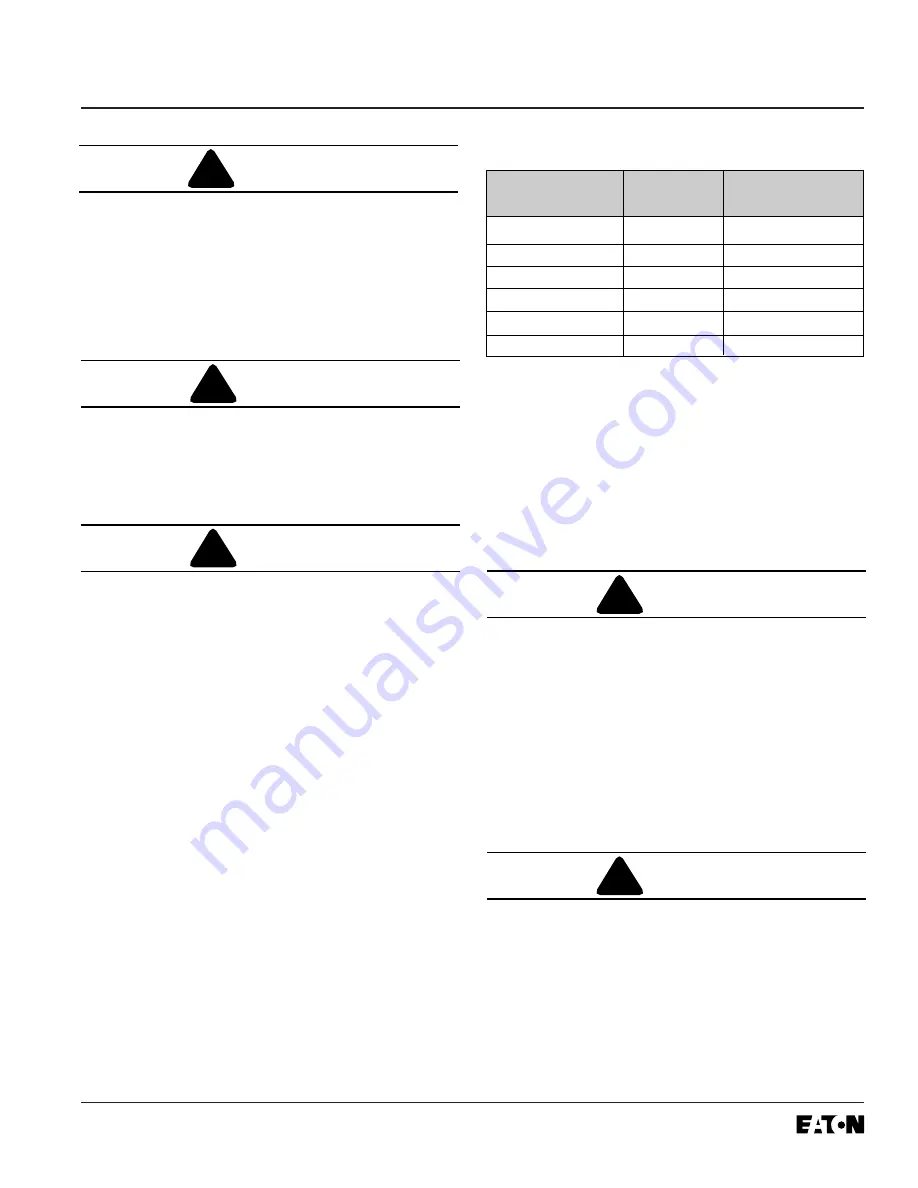
I.B. ATS-AG03
Page 15
Effective 7/00
USE OF CABLE LUGS NOT DESIGNED FOR THE
TRANSFER SWITCH MAY CAUSE HEATING PROB-
LEMS. BREAKER LUGS ONLY MOUNT TO THE
BREAKER,WHILE TRANSFER SWITCH LUGS
MOUNT TO BOTH THE BREAKER AND THE BUS
BAR BEHIND THE BREAKER. FOR INSTALLATION
INSTRUCTIONS, REFER TO THE INSTRUCTION
LEAFLET SUPPLIED FOR THE SPECIFIC LUGS.
TO HELP PREVENT COMPONENT DAMAGE OR
FUTURE MALFUNCTIONS, USE EXTREME CARE TO
KEEP CONTAMINANTS OUT OF THE TRANSFER
SWITCH EQUIPMENT WHEN MAKING POWER
CABLE CONNECTIONS.
RUN POWER CABLE THROUGH THE GUTTER
SPACE PROVIDED TO THE RIGHT OF POWER
PANEL. DO NOT ROUTE THE POWER CABLES
BEHIND OR TO THE LEFT OF THE POWER PANEL.
RUNNING THE CABLES BEHIND OR TO THE LEFT
OF THE POWER PANEL COULD INTERFERE WITH
THE PROPER OPERATION OF THE TRANSFER
SWITCH.
Test all power cables prior to connection to the unit to
ensure that conductors or cable insulation have not
been damaged while being pulled into position.
Power cables are to be connected to solderless screw
type lugs located on the transfer switch switching
devices. Refer to the separate Customer Wiring Booklet
supplied with the transfer switch equipment for power
termination Verify that the lugs supplied will accommo-
date the power cables being used. Also verify that the
cables comply with local electrical codes. Standard
transfer switch equipment, as supplied from the factory,
will accommodate the wire sizes shown in Table 4.2.
Carefully strip insulation from the power cables to avoid
nicking or ringing of the conductor strands. Prepare the
stripped conductor termination end by cleaning it with a
wire brush. If aluminum conductors are used, apply an
appropriate joint compound to the clean conductor sur-
face area.
IMPROPER POWER CABLE CONNECTIONS CAN
CAUSE EXCESSIVE HEAT AND SUBSEQUENT
EQUIPMENT FAILURE.
Tighten cable lugs to the torque identified on the label
affixed to the unit immediately adjacent to the lugs.
4.6 WIRING
POWER CONDUCTORS AND CONTROL WIRING
MAY HAVE VOLTAGE PRESENT THAT CAN CAUSE
SEVERE PERSONAL INJURY OR DEATH.
DE-ENERGIZE ALL POWER OR CONTROL CIRCUIT
CONDUCTORS BEFORE BEGINNING TO PERFORM
ANY WIRING ACTIVITY TO OR WITHIN THE TRANS-
FER SWITCH EQUIPMENT.
Power sources, load conductors and control wiring
should be connected to locations as indicated in the
Customer Wiring Booklet supplied with the transfer
switch equipment.
CHECK THE TRANSFER SWITCH EQUIPMENT
NAMEPLATE FOR RATED VOLTAGE. IT SHOULD
BE THE SAME AS THE NORMAL AND EMERGENCY
LINE VOLTAGES. OPERATING THE EQUIPMENT ON
IMPROPER VOLTAGE CAN CAUSE EQUIPMENT
DAMAGE.
!
CAUTION
!
CAUTION
!
CAUTION
Table 4.2 Transfer Switch Equipment Wire Sizes
Transfer Switch
Wire Size
Number of Cables
Ampere Rating
Ranges
per Phase
30-100
#14-3/0
1
150-200
#6-300MCM
1
300
#3-350MCM
1
400
#3-350MCM
2
400 (optional)
#1-500MCM
2
600
#1-500MCM
2
!
WARNING
!
CAUTION