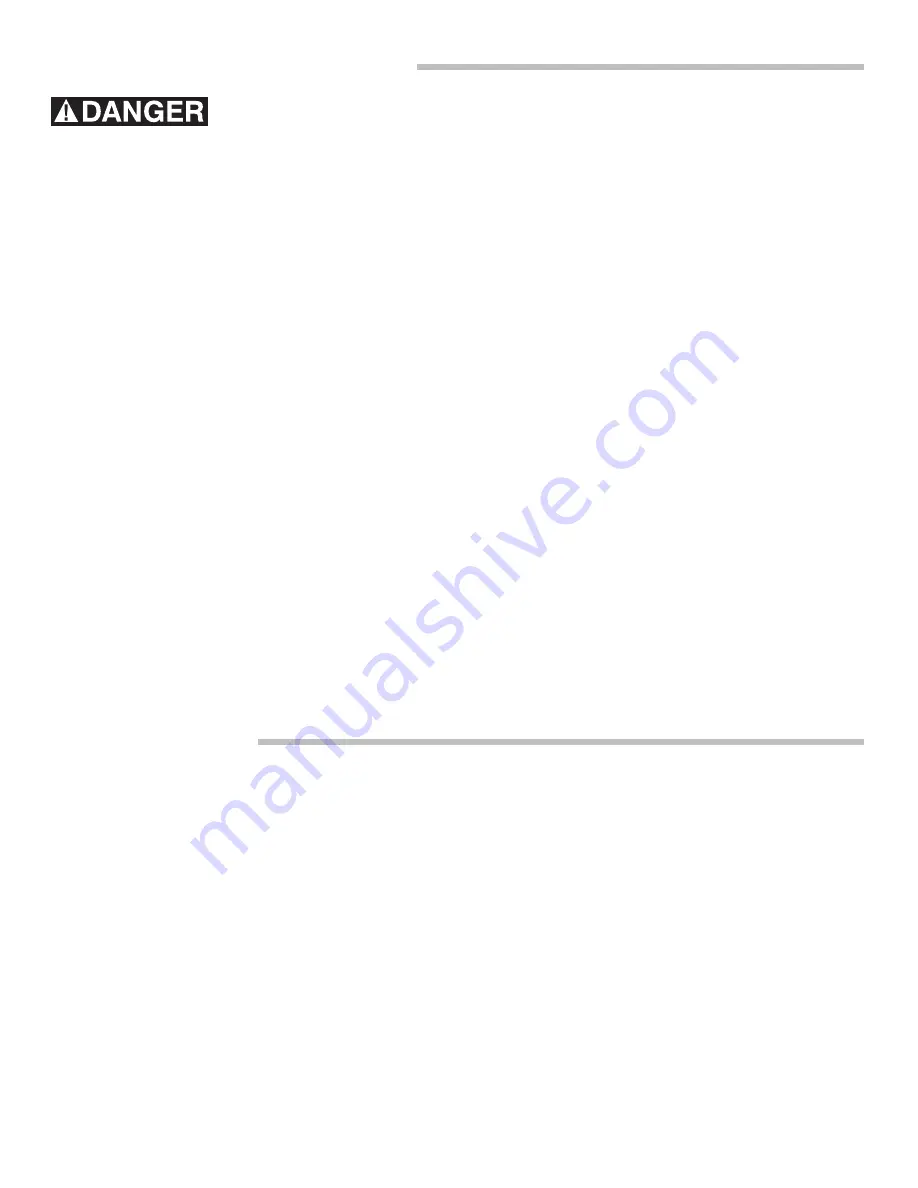
4
© Copyright 2010 Easthill Group, Inc.
SAFETY INFORMATION
FUMES AND WELDING GASES CAN BE DANGEROUS.
Do not breathe fumes that are produced by the welding operation. These fumes are dangerous. Keep
your head and face out of welding fumes. Shielding gases used for welding can displace air and cause
injury or death. Always work in a properly ventilated area.
WELDING SPARKS CAN CAUSE FIRE OR EXPLOSION.
Do not operate electric arc welder in areas where fl ammable or explosive vapors are present. Always keep
a fi re extinguisher nearby while welding. Use welding blankets to protect painted surfaces, dash boards
engines, etc.
ARC RAYS CAN BURN.
Use a shield with the proper fi lter ( a minimum of #11) to protect your eyes from sparks and the rays of the
arc when welding or when observing open arc welding. Use suitable clothing made from durable fl ame-re-
sistant leather material to protect your skin. Protect nearby individuals with a non-fl ammable barrier.
HOT METAL WILL BURN.
Electric welding operations cause sparks and heats metal to temperatures that will cause severe burns!
Use protective gloves and clothing when performing any welding operations. Always wear long pants,
long-sleeved shirts and leather welding gloves. Make sure that all persons in the welding area are pro-
tected from heat, sparks and ultraviolet rays. Use additional face shields and fl ame resistant barriers as
needed. Never touch work piece until it has completely cooled.
ELECTROMAGNETIC FIELDS MAY BE DANGEROUS.
The electromagnetic fi eld that is generated during arc welding may interfere with various electrical and
electronic devices such as cardiac pacemakers. Anyone using such devices should consult with their
physician prior to performing any electric welding operations. Exposure to electromagnetic fi elds while
welding may have other health effects which are not known.
UNPACKING
When unpacking, check to make sure all the parts listed below are included.
• Mig 175 Unit
• Spool Gun
• Torch Gun Cable Assembly
• Ground Cable Assembly
• Gas Flow Regulator
• Gas Flow Regulator Hose
• Hand-Held Shield
• Wire Brush
• 2 lb. Spool of 0.023” Mig Wire