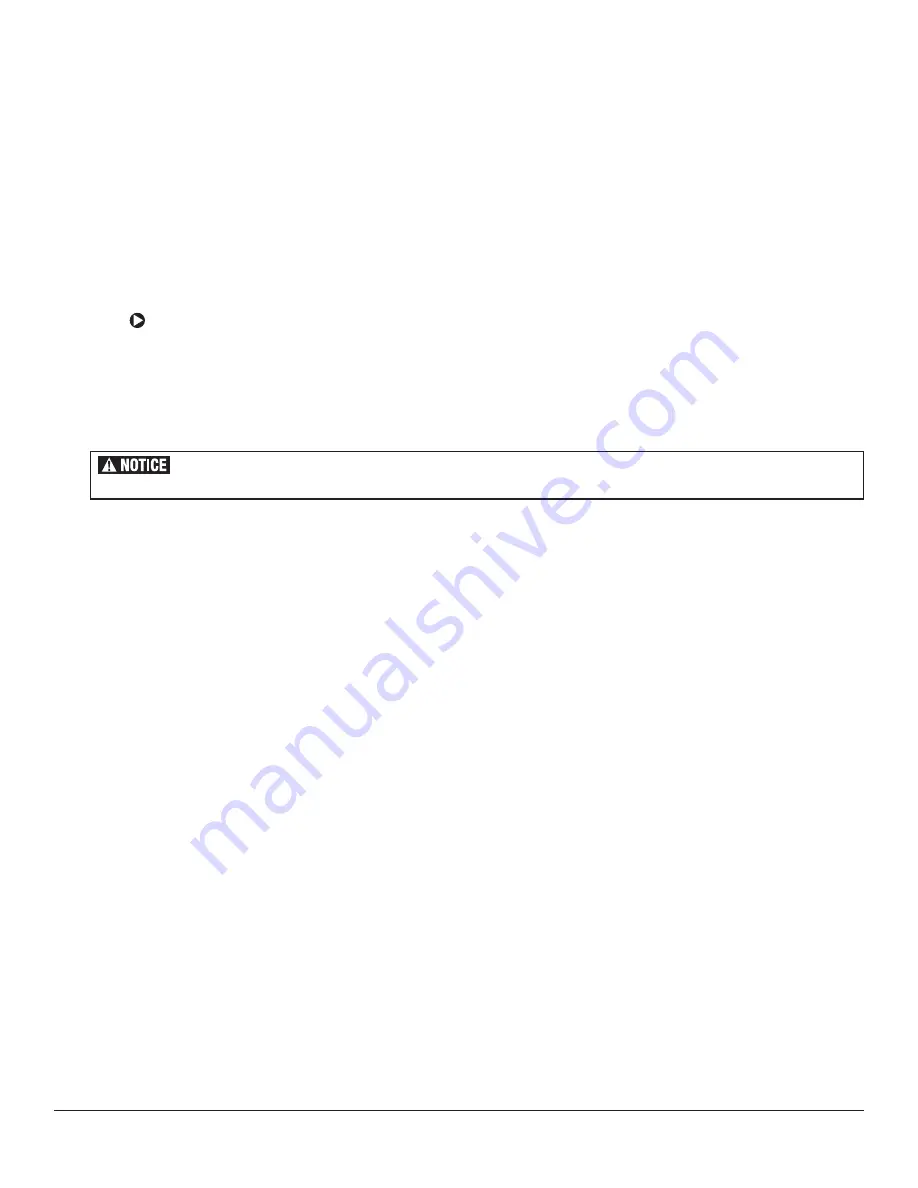
18
Eastwood Technical Assistance: 800.343.9353 >> [email protected]
WELDING TECHNIQUES
SHEET METAL WELDING TECHNIQUES
When welding sheet metal a different approach is usually taken to account for how thin the metal is and how susceptible it is to warping. The technique most
often used is called Stitch Welding and this process is described below:
• Clean the metal to be welded of any paint, rust, oil, grease, dirt, or any other contaminants that may be on the surface of the piece.
• Secure the pieces to be welded in place using clamps. Be sure to leave a small gap between the two pieces of sheet metal for the weld to flow into, this
will result in a lower bead height which will require minimal finishing.
• Consult the Suggested Settings Chart and set the Voltage and Wire Speed knobs appropriately.
• Get some pieces of scrap metal of the same thickness and verify that the settings will work for the specific weld you will be making.
• Once the settings have been fine-tuned tack weld your final pieces in place and remove the clamps if they are in the way of the weld.
• The Stitch Welding technique can now be utilized which is basically a series of connected “Tacks” To perform the technique, set the 2T/4T/Tack Selection
Button to select to the Tack Mode
(FIG 17)
. Triggering the gun produces an arc for approximately 1/2 second to form a tack weld. Continue to trigger
the gun on and off making a series of connected tack welds following along the path of the weld joint. Continue the series of tacks for an inch or so and
then move to a different section of the weld and perform the process there.
It is essential to keep moving around to spread out the heat making sure not to get one section too hot warping the metal.
• Once the entire weld has been completed allow the metal to cool. If necessary, follow up with a flap disc to grind the weld bead flush.
HEAVIER GAUGE METAL WELDING TECHNIQUES
When welding heavier gauge metal, a continuous bead is formed using a ‘push’ method. This process is described below:
• Clean the metal to be welded of any paint, rust, oil, grease, dirt or any other contaminants that may be on the surface of the piece.
• Secure the pieces to be welded in place using clamps. Be sure to leave a small gap between the two pieces of metal for the weld to flow into,
this will result in a lower bead height which will require minimal finishing.
• Consult the Suggested Settings Chart inside the Side Panel and set the Voltage and Wire Speed knobs appropriately.
• Get some pieces of scrap metal of the same thickness and verify that the settings will work for the specific weld you will be making.
• Once the settings have been fine-tuned, tack weld the final pieces in place and remove the clamps if they are in the way of the weld.
• When welding heavy gauge metal there are two basic approaches to creating the weld. The first is a continuous bead with steady gun movement along
the length of the joint. The second type of weld is a Stringer or Weave bead. This is accomplished by moving the MIG Gun in a circular or zig zag pattern.
Either of these techniques will create strong welds but in some cases the Stringer or Weave type will create a more aesthetically pleasing weld bead.
• Once the entire weld has been completed, allow the metal to cool. If necessary, follow up with a flap disc to grind the weld bead flush.
DO NOT attempt to weld material thicker than 3/16”.