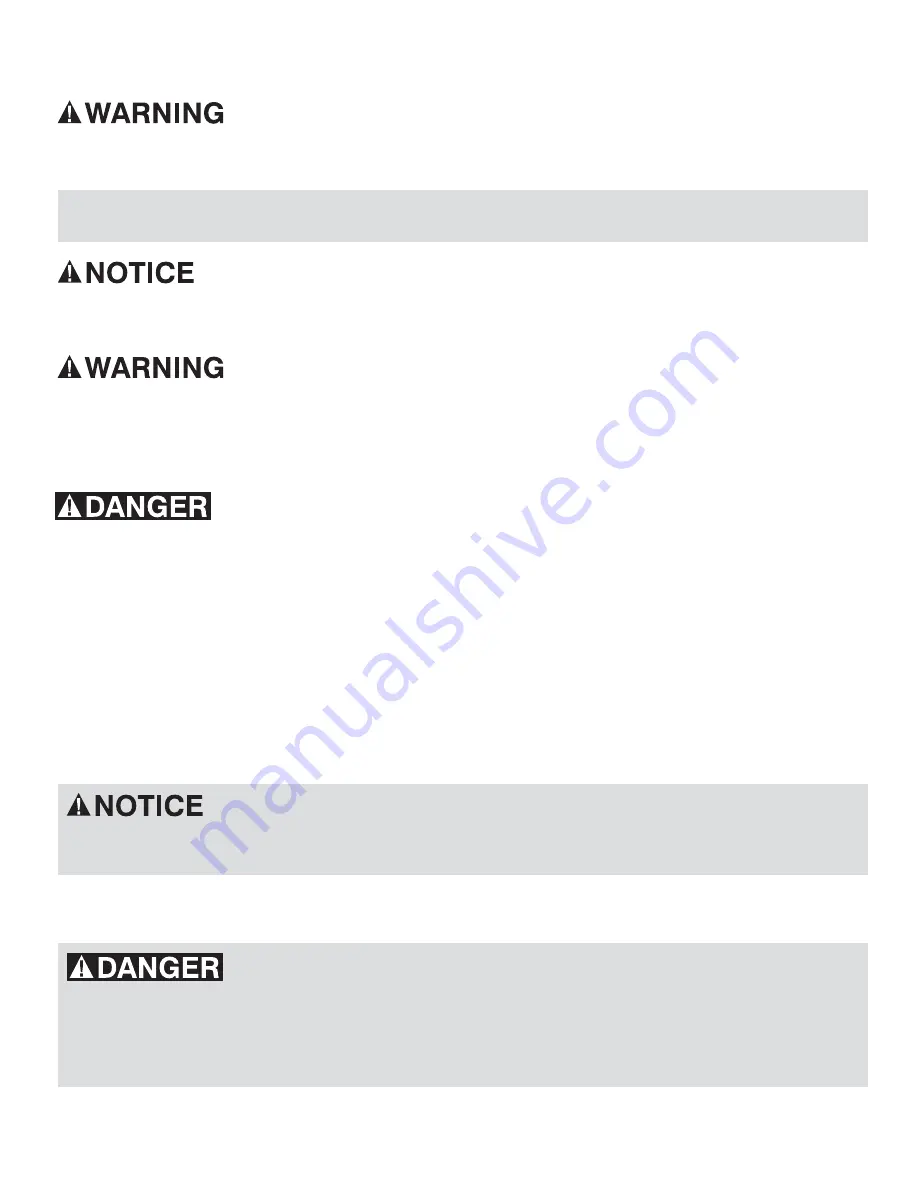
To order parts and supplies: 800.345.1178 >> eastwood.com
3
SAFETY INFORMATION
ARC WELDING CAN BE DANGEROUS.
THIS WELDING MACHINE MUST BE CONNECTED TO A POWER SOURCE IN ACCORDANCE WITH APPLIANCE ELECTRICAL CODES.
DISCONNECT FROM POWER SOURCE BEFORE ASSEMBLING, DISASSEMBLY OR MAINTENANCE OF
THE TORCH OR CONTACT TIP OR CHANGING WIRE SPOOLS.
FOR SAFETY TURN OFF AND UNPLUG MACHINE WHEN INSTALLING NEW WIRE SPOOL, ADJUSTING WIRE TENSION
ROLLER OR REPLACING CONTACT TIP.
THE GAS NOZZLE MUST ALWAYS BE INSTALLED WHEN WELDING-DO NOT WELD WITHOUT THE GAS NOZZLE IN PLACE.
THE CONTACT TIP IS ELECTRICALLY “HOT” AND IF IT CONTACTS THE GROUNDED WORK PIECE IT WILL CAUSE DAMAGE.
ALL INSTALLATION, MAINTENANCE, REPAIR OPERATION OF THIS EQUIPMENT SHOULD BE PREFORMED BY QUALIFIED
INDIVIDUALS IN ACCORDANCE WITH NATIONAL, STATE AND LOCAL CODES.
ELECTRIC SHOCK CAN KILL!
Improper use of an electric welder can cause electric shock, injury and death! Read all
precautions described in this manual to reduce the possibility of electric shock.
1.
The MIG135 power switch is to be in the OFF (“0”) position when installing the work cable and gun and while plugging
in the power cord.
2.
Always wear dry, protective clothing and leather welding gloves and insulated footwear.
3.
Always operate the welder in a clean, dry, well ventilated area. Do not operate the welder in humid, wet, rainy or poorly
ventilated areas.
4.
Be sure that the work piece is properly supported and grounded prior to beginning an electric welding operation.
5.
The electrode and work (or ground) circuits are electrically “hot” when the welder is on. Do not touch these “hot” parts
with your bare skin or wet clothing.
DISCONNECT FROM POWER SOURCE BEFORE ASSEMBLING, DISASSEMBLY OR MAINTENANCE OF
THE TORCH OR CONTACT TIP OR CHANGING WIRE SPOOLS.
Always attach the ground clamp to the piece to be welded and as close to the weld area as possible. This will give the least resistance
and best weld.
FUMES AND WELDING GASES CAN BE DANGEROUS.
Do not breathe fumes that are produced by the welding operation. These fumes are dangerous. Keep your head and face out of
welding fumes. Shielding gases used for welding can displace air and cause injury or death. Always work in a properly ventilated
area, we recommend wearing an OSHA-approved respirator when MIG welding!