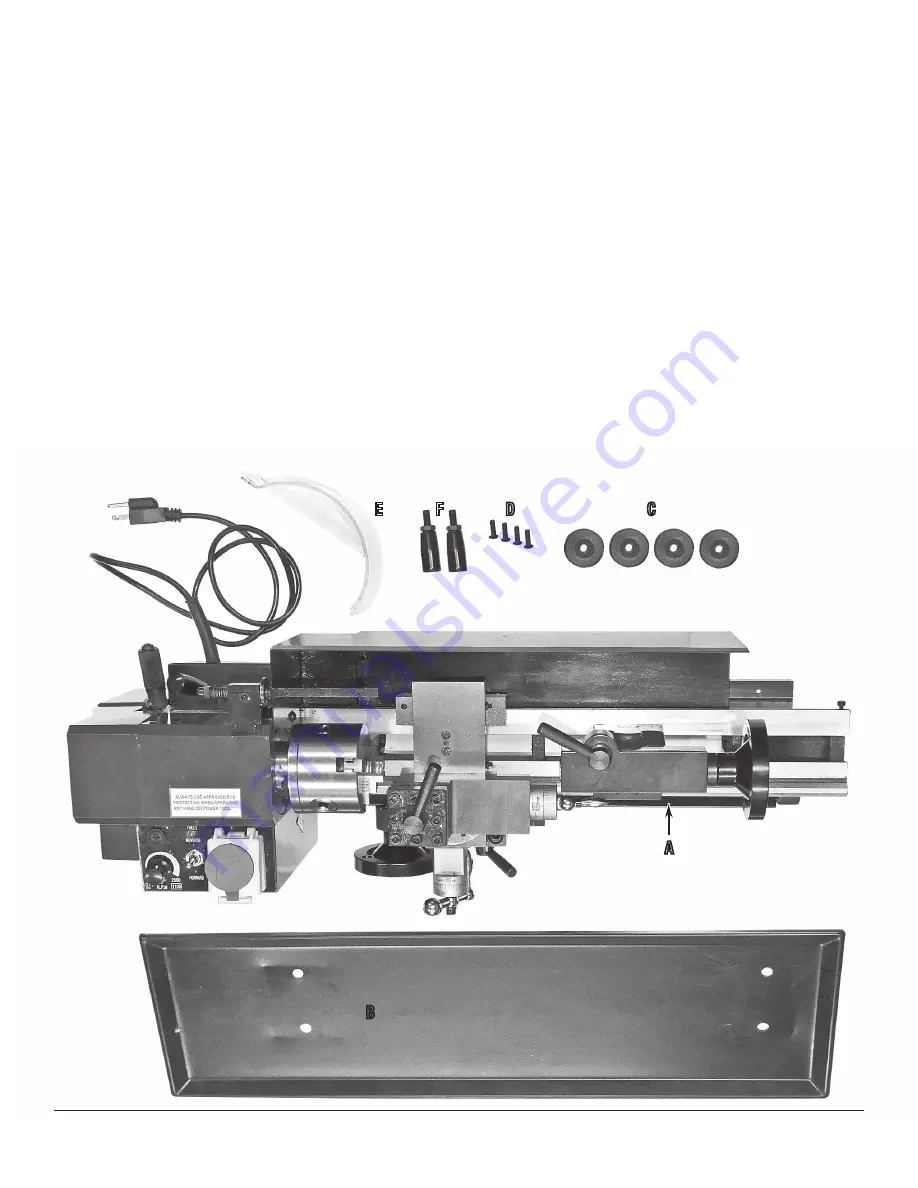
2
Eastwood Technical Assistance: 800.343.9353 >> [email protected]
The
EASTWOOD 7” X 12” MINI LATHE
is equipped with all the features found on large lathes in a compact, home workshop-friendly size. Auto-feed and
selectable gear train components allow complex threading operations with a high degree of precision. The included inside and outside 3-Jaw Chuck set will
accommodate a wide range of workpiece configurations for most turning and cutting operations.
CONTENTS
PARTS
(1)
Main Lathe Unit with 3-Jaw Chuck (installed)
[A]
(1)
Chip Tray
[B]
(4)
Rubber Mounting Feet
[C]
(4)
M6 Pan Head Mounting Screws
[D]
(1)
Clear Plastic Chuck Guard
[E]
(2
Handwheel Crank Handles
[F]
SPECIFICATIONS
Power Requirements:
120 VAC, 60hz.
Maximum Tool Size:
5/16” x 5/16” [8mm x 8mm]
Compound Travel:
2.75” [69.8mm]
Headstock Spindle Size:
3” [76.2mm]
Headstock Spindle Bore:
0.78” [19.8mm]
Swing Over Bed:
7” [177.8mm]
Distance Between Centers:
12” [304.8mm]
Headstock Spindle Taper:
Morse Taper 3
Spindle Speed Range:
0-2500 RPM
Spindle Bearings:
Sealed and Permanently Lubricated
Tailstock Spindle Quill Travel:
2.5” [63.5mm]
Tailstock Taper:
Morse Taper 2
Compound Slide Graduations:
0.001”
B
✓
A
E F D C