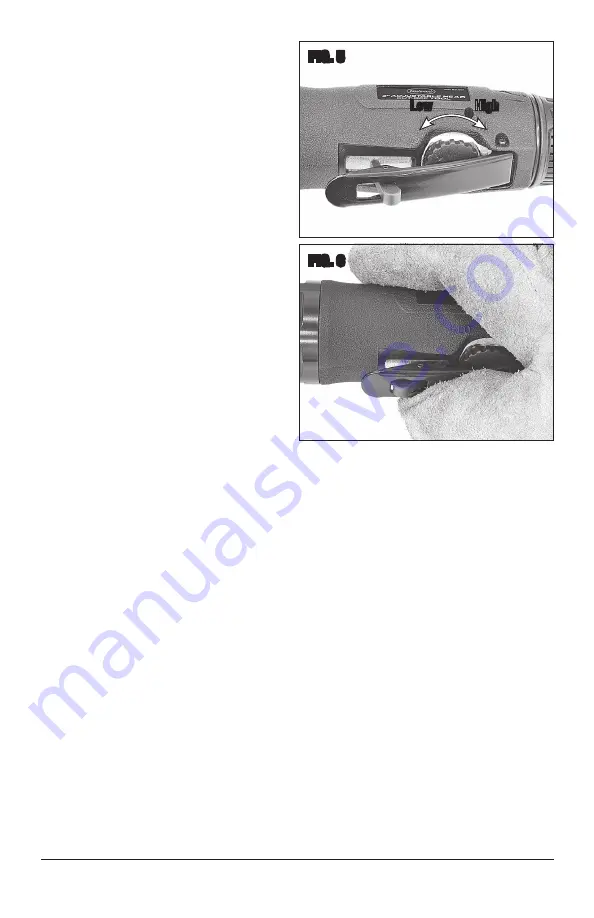
6
Eastwood Technical Assistance: 800.343.9353 >> [email protected]
SET-UP & CONNECTION
• Be sure that the air supply to the tool
is clean and dry. Moisture in the sup-
ply line will quickly damage the motor
and valves.
• A minimum 3/8” I.D. air line should
be used for optimal performance.
• Thread a suitable 1/4” Male Quick-
Disconnect Fitting (included) into the
air inlet of the tool using TFE thread
sealing tape (not included).
OPERATION
• Rotate the Knob located at the rear of
the tool handle and under the Throttle
Paddle to regulate motor speed
(FIG
5)
. This Knob offers 30° of travel.
Note that rotating in a Clockwise
direction will result in higher speed
while Counter-clockwise will
decrease speed.
• Flip the Safety Lever forward and
Depress Throttle Paddle inward to
operate tool
(FIG 6)
.
• Always maintain a firm grip while
operating tool, do not force but allow
the rotational speed of the Cut-Off
Wheel to do the work.
• Be sure that the workpiece is
clamped down or held securely to
minimize the danger of injury while
operating tool.
FIG. 5
FIG. 6
Low High