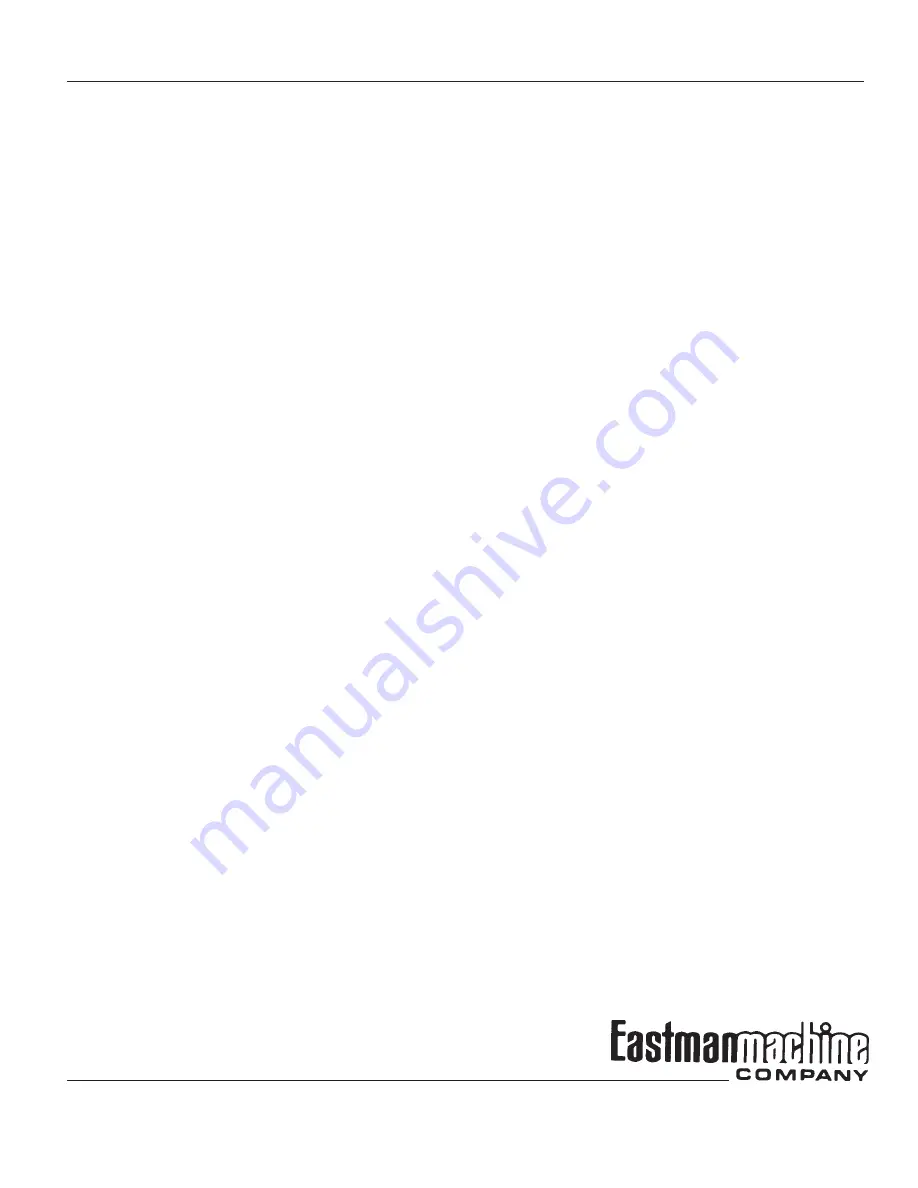
15
Edge Control Eye Adjustment
Factory set to be suitable for most fabrics.
Side edge accuracy adjustment:
If adjustment is required, raise the cradle to loading
position. Loosen two screws holding the bottom sensor
and move sensor eyes closer for more accuracy. If
sensor eyes are to close the edge control will not operate
properly and the eyes must be separated slightly.
Experimentation will yield the best setting for your fabric.
Edge sensitivity adjustment:
If adjustment is required the sensor must be removed for
adjustment. Each sensor has a countersunk adjusting
screw on the bottom surface. Turn screw clockwise to
increase sensitivity, counterclockwise to decrease sen-
sitivity. Replace sensors and set side edge adjustment.
Spreading Tension Adjustment
Spreading tension setting is set on the cradle control
panel. Turn clockwise to increase tension or counter-
clockwise to decrease tension. Experimentation will
yield the best setting for your fabric. (Each roll of material
possesses it's own unique tension and it is the operator's
responsibility to adjust the tension to meet the material
needs).
Machine Messages
Main Drive Circuit not Ready: Main drive circuit not
activated. Press Green main power button.
Speed Control Set On Zero: Spreading speed needs
adjustment. Press "Speed+" to set spreading speed.
Speed 0000000*: Displays speed of spreader.
The * displays the maximum spreading speed.
Out Of Cloth Switch Activated: Edge platform moved to
end limit (edge control eyes don't see fabric). Thread
fabric past edge control eyes.
Auto Mode Stop Release Handle To Center: Release
throttle handle.
Waiting For Machine Restart... :Machine waiting for cut
complete signal from knifebox.
Must be Programmed to set Load Position: Machine not
programmed, see programming.
Invalid Load Position, Wrong End: Move spreader to
opposite end of spread.
Load Setting within Programmed Ends: Move machine or
reprogram spread. Load position must be equal to or
greater than end marker location.
Service and Maintenance
Daily:
-Blow off entire machine and encoder rail using low
pressure compressed air (required twice a day de-
pending on material).
-Check safety cams for proper location.
-Check cradle belts for wear and proper tension.
-Check guide wheels for proper adjustment and wear.
-Check spreading machine area for any obstructions.
Weekly:
-Inspect encoder (pulley, belt, encoder spring, etc.)
-Check for any unusual wear and determine why.
Bi-Monthly:
-Remove covers, check all chains, tighten and lubri-
cate.
-Inspect all wheel, remove lint, etc.
-Check entire machine for loose nuts and bolts.
-Check table and track for loose or damaged parts.
Monthly:
-Clean Feed rail.
-Inspect trolley and power line.
-Check mast for loose nuts, bolts or worn parts.
-Check tension on all chains, tighten if necessary.
-Check oil level in gear reducer; fill if necessary.
Summary of Contents for CR 500
Page 8: ...8 EASTMAN Familiarization ...