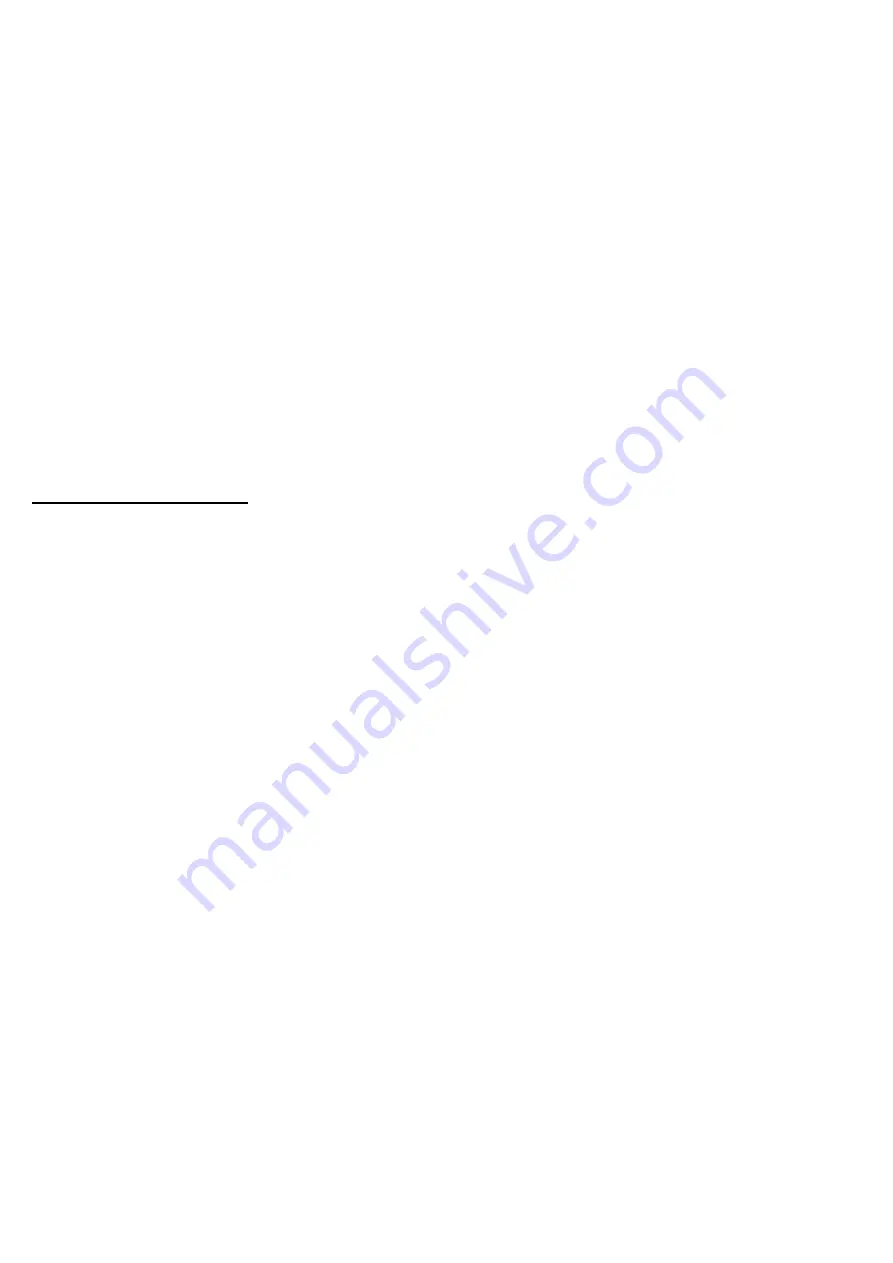
HINT: The typical average voltage under load of a Ni-Cd/Ni-MH cell is 1.0 volt. The typical average voltage under load of a Li-Po cell is 3.3 volts. This
means the typical average voltage under load of a 10 cell Ni-MH pack is approximately 10 volts and a 3 cell Li-Po pack is approximately 9.9 volts. Due to
variations in the performance of a given battery, the average voltage under load may be higher or lower. These however are good starting points for initial
calculations.
Model: 15-size 3D ARF (converted to electric)
Estimated Flying Weight w/Battery: 2.4 lbs
Total Input Watts Required for Desired Performance: 360 (minimum)
Motor: Power 15
Max Continuous Current: 34A*
Max Burst Current: 42A*
Cells (Li-Po): 3
3 Cells, Continuous Power Capability: 9.9 Volts (3 x 3.3) x 34 Amps = 336 Watts
3 Cells, Max Burst Power Capability: 9.9 Volts (3 x 3.3) x 42 Amps = 415 Watts
Per this example, the Power 15 motor (when using a 3S Li-Po pack) can handle up to 415 watts of input power, readily capable of powering the
15-size 3D model with the desired level of performance (requiring 360 watts minimum). You must however be sure that the battery chosen for power can
adequately supply the current requirements of the system for the required performance.
Battery Choices:
We recommend Thunder Power Li-Po batteries for the best performance and lowest weight (in some cases Ni-MH 1800-2200mAh high-discharge packs
also make good alternatives at the expense of weight and lower capacity). Some examples of the packs we recommend for use with the Power 15 motor
can be found below:
THP21003SPL
2100mAh 3-Cell 11.1V LIPO,16GA
THP42003S2PPL 4200mAh 3-Cell 11.1V LIPO, 13GA
Examples of Airplane Setups:
Please see our web site for the most up-to-date information and airplane setup examples.
NOTE: All data measured at full throttle. Actual performance may vary depending on battery and flight conditions.
15-size 3D ARF (converted to electric)
Option 1:
Motor: Power 15
ESC: E-flite 40A Brushless (V2) (EFLA312B)
Prop: APC 11x7E (APC1107E)
Battery: Thunder Power PRO LITE 2100mAh 11.1V 3-Cell (THP21003SPL)
Flying Weight w/Battery: 2.1 lbs
Amps
Volts
Watts
Input Watts/Pound
RPM
27.8
10.4
289
138
8200
Expect higher speeds and lower thrust for mild 3D aerobatics. Average duration is approximately 7-9 minutes depending on throttle management.
Option 2:
Motor: Power 15
ESC: E-flite 40A Brushless (V2) (EFLA312B)
Prop: APC 11x7E (APC11070E)
Battery: Thunder Power PRO LITE 4200mAh 3S2P 11.1V (THP42003S2PPL)
Flying Weight w/Battery: 2.4 lbs
Amps
Volts
Watts
Input Watts/Pound
RPM
31
11.1
344
143
8700
Expect average speeds and higher thrust -ideal for F3A and extreme power for 3D and artistic aerobatics. Longer duration is approximately 15-18 minutes
depending on throttle management.
Accessories:
See our web site at www.E-fliteRC.com or www.horizonhobby.com for our complete line of brushless motors. We have posted a specification comparison
sheet on our web site so you can compare the different motors we offer.
EFLA110
Power Meter (measures power output in amps, volts, watts, and capacity)
EFLA241
Gold Bullet Connector Set, 3.5mm (3)
EFLM1925
Prop Adapter w/ Collet, 5mm
EFLA312B
40-Amp Brushless ESC (V2)
EFLM40151
Shaft: Power 15 BL Outrunner
Reversing the Shaft:
This Outrunner motor has a shaft, which exits through the rotating part of the motor. If you want to reverse the shaft to exit through the fixed part of the
motor, follow these instructions carefully for changing the shaft installation.
NOTE:
The user assumes all liability for damage that may occur.
1.
Loosen the set screw on the shaft collar and remove the collar from its location against the bearing.
2.
Remove the small black donut washer that rests against the bearing.
3.
Loosen the two set screws in the rotating part of the motor.
4.
Slide the shaft through the motor. It may be necessary to use a small hammer to lightly tap the shaft. It is very important that you do not bend the
shaft in this process so use extreme caution to assure this does not happen.
5.
Re-install the donut washer against the bearing. Do not skip this step.
6.
Re-install the shaft collar back against the washer and bearing.
7.
Retighten all setscrews making sure you line up with the flat spot on the shaft.
Replacement shafts are available separately.