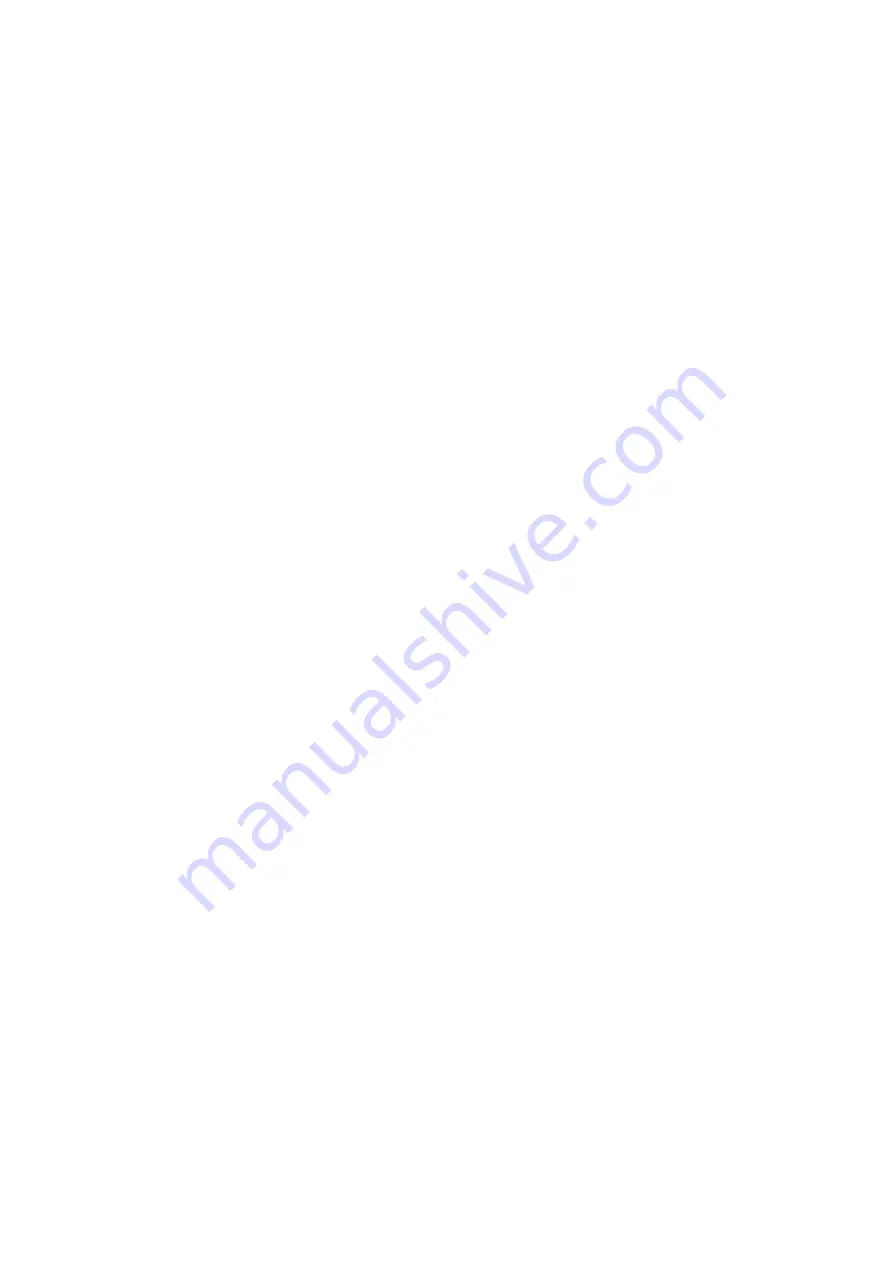
How we got there
How do you design a new legend?
Experiments, arguments, tests, more experiments, designs, prototypes …
You can’t reinvent the wheel. But you can change the spokes. In redesigning the Contour range, we changed a
lot of spokes.
We worked hard to retain the original’s DNA; its character. But we also wanted to provoke – so we gave our teams
free rein to experiment with different materials, different techniques and different designs.
That meant scaring ourselves a little sometimes. Like when we did some A/B listening tests on small voice coils
compared with our signature large ones. That’s a big step. This time, it proved to be a step too far – they just
didn’t sound as good as the technology we’ve been using for years – but we didn’t simply discount the idea. We
listened.
Then there’s the time when Malte Köhn, Lead Product Designer on the Contour, rocked up to a meeting with
armfuls of sketches (you can see some of them here). “I tried to work with non-traditional colour and material
combinations,” he says. “But I wanted to keep the Contour’s classic design, which is quite edgy and brutal. We
turned it into something that’s more elegant and technical.” Malte is really proud of his design – and he should be,
because that’s the one we all chose as a group.
Michael Rohde Böwadt, our brave VP of product management, was the one who took the leash off. “We went
very wide in the beginning,” he says. “I told them to just make the best drivers in the world. The best cabinets in
the world. To approach it all in a different way.”
No pressure, then.
“It backfired a bit! But it was also very interesting. We got some very interesting results, provoked a lot of
discussions, and were able to really zero in on what we wanted to do next.”
One of the things that came out of those discussions was using different driver materials. Ultimately we decided to
stick with our tried-and-true MSP – but we told Daniel, Andreas and Danny that we wanted it to sound even
better. Their Eureka! moment came when they started varying the material’s thickness across the diaphragm,
because it means the whole cone is optimised for the frequencies it’s been built to reproduce. And it works.
Michael insisted on keeping the metal baffle. It’s part of the Contour’s design heritage, after all, and there are some
incredibly good acoustic reasons for keeping it. It’s rigid, solid and extremely well-damped (which lets those fancy
new MSP drivers do their thing as exactly they should).
But now it’s made from aluminium instead of iron.
We decided on aluminium because we can shape it. You can see that from the drawings. It chamfer fits with the
gently curved cabinet edge, and its milled shape gives a modern feel to the Contour’s classic performance.
But it also meant we could bring other details to the party: the driver baskets themselves are chamfered, too. We
love how they look, but they also help to reduce diffractions. Good job all round, then (we even went so far as to
have more than one argument about whether the screws should be visible. The “yes” side won, and even our
minimalist contingent had to agree that it was the right choice).
In developing the new drivers and crossover, we turned to Daniel Emonts and Mark Thorup. (Mark started here as
an R&D engineer in 1983 and rose to the lofty heights of strategic product manager.) Between them they’re the
gurus of our design department.
They know everything. We took their findings to our R&D team and psychoacoustics guys, said “aim this way”,
How we got there
7