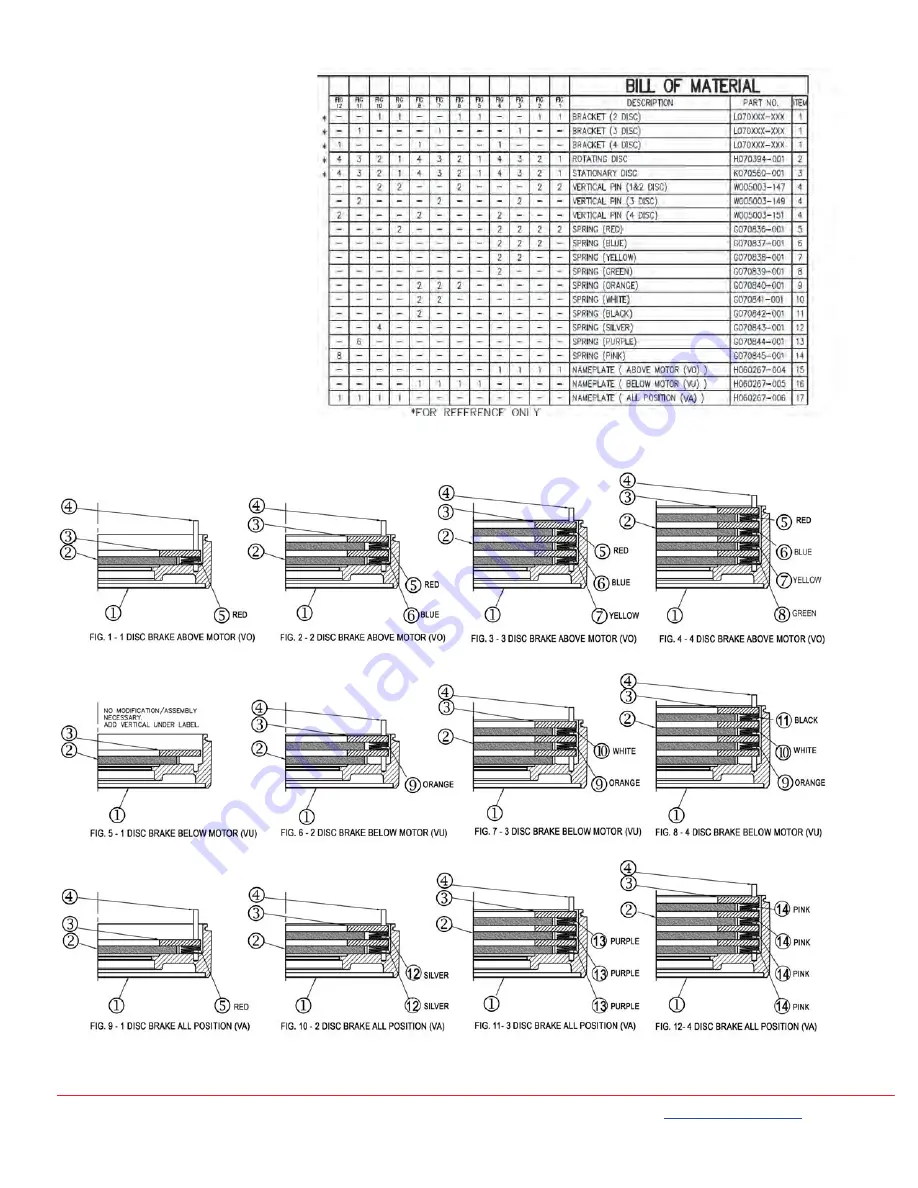
4740 W. ELECTRIC AVE. • MILWAUKEE, WISCONSIN 53219 • 414/672-7830 • FAX 414/672-5354 •
www.dingsbrakes.com
BK4773S-3 (6/2017)
8
VERTICAL MOUNTING
Installation and Adjustment
Installation and adjustment of the
vertically mounted brake is the same as
on the standard model.
Friction Disc Replacement
When replacing friction discs, follow
procedure outlined on page 3 with this
addition:
Care must be taken to insure proper
insertion of disc separating springs.
Springs are color coded for easy
identification, and reference is made to
spring color (See table to the right &
diagram below). Since the installation
order of the disc springs is dependent on
brake mounting position (above or below
motor), it is important to consult the
correct diagram for spring location.