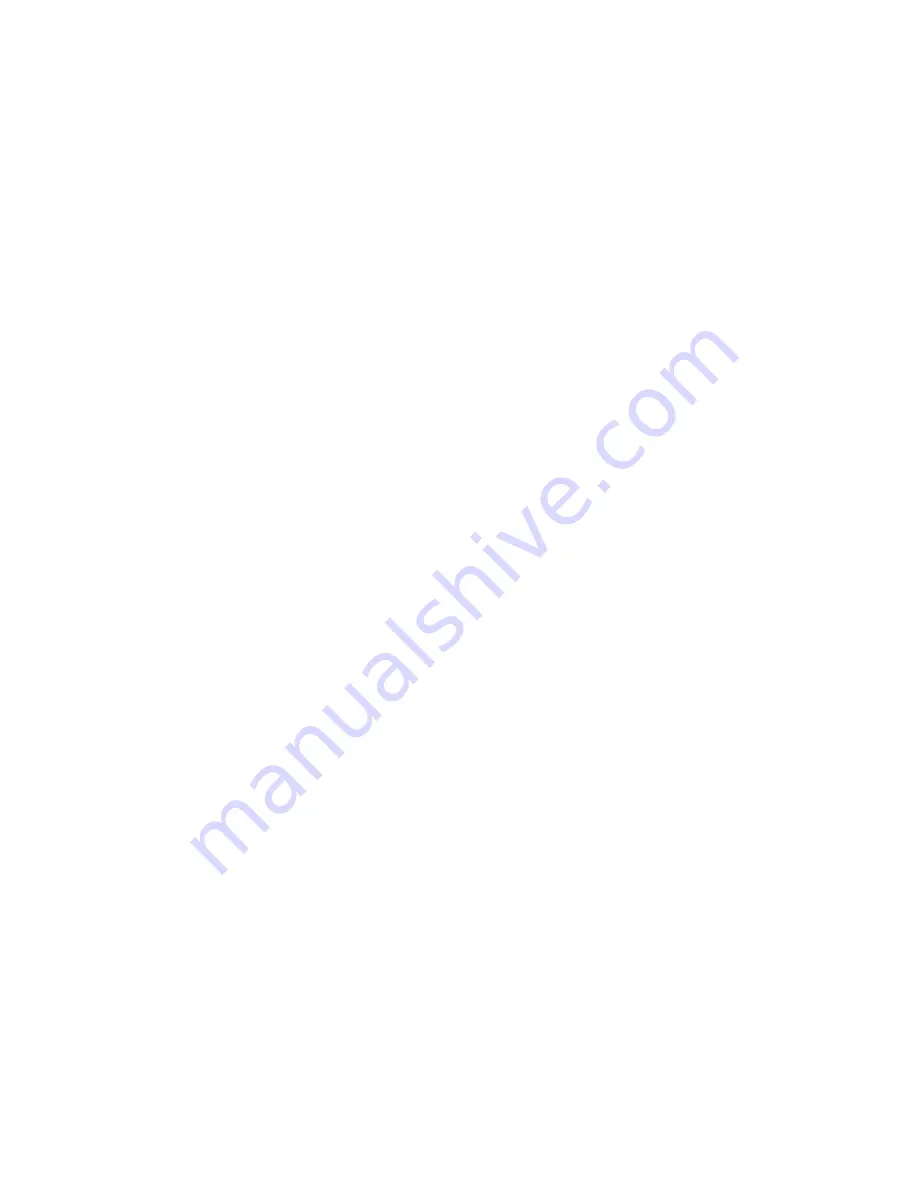
Disassembly/Assembly Instructions - Mini-Dynorbital
®
Supreme
Important: Manufacturer’s warranty is void if tool is disassembled before warranty expires.
A Motor Repair Kit (57525) is available which contains special tools for disassembly/assembly. Please refer to parts breakdown for part identification.
Motor Disassembly:
1.
Disconnect tool from power source.
2.
Invert machine and secure in vise, using
57092
Collar (supplied in
57525
Repair Kit) or padded jaws. Remove sanding pad.
3.
Insert
56058
Lock Ring Tool (supplied in
57525
Repair Kit) into corresponding tabs of lock ring and unscrew. Motor may now be lifted out for service.
4.
Remove lock ring, washer, front ring and rear ring from motor. Remove
95626
Retaining Ring, upper motor may now be disassembled.
5.
Remove the rear plate and the cylinder assembly by securing the cylinder in a bearing separator gripped on the cylinder exhaust and extra pocket area.
Push the motor shaft through the bearing.
6.
Remove the rotor, vanes and key from the motor shaft. Remove the front plate using a small (#2) arbor press. Support the edges of the
front plate while pressing on the small end of the motor shaft.
a.)
If, during step 7, the front plate and bearing remain together, press bearing out of the front plate using
57091
Press Tool (supplied in
57525
Repair Kit).
b.)
If, during step 7, the front plate and
57088
Bearing remains on the motor shaft, it can be removed with a bearing separator.
7.
Remove
01206
Bearing from the rear plate by using a bearing press tool.
8.
Disassemble the head assembly as follows:
a.)
Place head assembly into a soft jaw vise. Using a thin screwdriver, pick out the end of retaining ring and peel out.
b.)
Screw threaded portion of the
54121
Bearing Puller (supplied in
57525
Repair Kit) onto the balancer shaft and using the slider weight, pull out.
c.)
Remove
95558
Retaining Ring. Press off
57022
Bearings and remove loose parts.
9.
If during step 8, the
57022
Bearings remain in the head assembly, they can be removed by heating the counterweight and using either an inside
bearing puller or a blind hole bearing puller.
Motor Disassembly Complete.
To Assemble:
Important:
Be certain all parts are clean and in good repair before assembling.
1.
Assemble the balancer assembly as follows:
a.)
Install
95613
Retaining Ring onto
54145
Roloc Sub Assembly. Install
95612
Shield with convex face toward head of
54145
Roloc Sub Assembly.
b.)
Remove three of the four bearing seals from the
50722
Bearings. Press fit
50722
Bearings onto
54145
Roloc Sub Assembly with the remaining
bearing seal facing
95612
Shield. Install
95558
Retaining Ring.
2.
Place
54036
Counterweight into a soft jaw vise with the large end up.
3.
Apply a slight amount #271 Loctite
®
(or equivalent) in several places around the outside diameter of the
50722
Bearings and slide into the
54036
Counterweight until
50722
Bearings are firmly seated at bottom. Squeeze
95613
Retaining Ring into groove to complete the assembly. Remove from vise.
4.
Press
57088
Bearing onto the Motor Shaft down to the shoulder.
5.
Press
57057
Front Bearing Plate onto
57088
Bearing and check for smooth rotation.
6.
Place the
57113
Rotor and
56047
Key on the
57528
Motor Shaft. Place the vanes into the rotor slots.
Note:
Vanes should be lightly lubricated with Dynabrade Air Lube P/N
95842
(or equivalent) before installation into rotor slots.
7.
Place
57058
Cylinder Assembly over rotor. The “short” line-up pin goes toward the front plate.
8.
Place
57056
Rear Bearing Plate (with
01206
Rear Bearing pressed into place) over shaft and “long” end of line-up pin and press fit in place.
9.
Place
95626
Retaining Ring in groove.
10.
Place
57054
Rear Ring over the rear plate and line-up pin. Turn the motor over and place
57055
Front Ring over the front plate making sure that the
“legs and fingers” on the front and rear rings line-up. Also the small cut-outs on both rings should line-up with the square holes in the cylinder/endplate
assembly. Place
95973
Washer and
57059
Lock Ring onto the front ring with 1 drop of pneumatic tool oil spread between the washer and lock ring.
11.
Secure motor housing in vise, using
57092
Collar or padded jaws. Spread 2-3 drops of pneumatic tool oil around the housing bore and slide motor
assembly in housing.
Note:
Be certain line-up pin enters the pocket in bottom of the housing and the “legs” of the rings stay in line.
12.
Tighten lock ring with
56058
Lock Ring Tool torque to 28 N•m/250 in. - lbs.
Motor Assembly Complete. Please allow 30 minutes for adhesives to cure before operating tool.
Valve and Speed Regulator Assemblies:
1.
Secure housing in vice using
57092
Collar or padded jaws.
2.
Remove inlet bushing,
01468
Spring, valve and seal from housing.
3.
Remove
95697
Retaining Ring. Press the spread regulator and valve stem out of the housing. Remove the
01025
O-Rings (2).
4.
Place new
01025
O-Rings (2) on the speed regulator and place in housing with valve stem. Install new
95967
Retaining Ring.
5.
Place seal in housing. Using tweezers or needle nose pliers, place the valve in the housing so that its pin goes into the valve stem hole. Place
01468
Spring into the housing so the small end is toward the tip valve.
6.
Spread 1 drop of #271 Loctite
®
(or equivalent) around the threads of the inlet bushing and tighten into housing torque to 23 N•m/200 in. - lbs.
Tool Assembly Complete. Please allow 30 minutes for adhesives to cure before operating tool.
Note:
5,000 RPM Motors should operate at between 4,500 and 5,000 RPM at 6.2 bar (90 PSIG) and for 7,500 RPM Models between 7,500 and 8,250 RPM at
6.2 bar (90 PSIG). RPM should be checked with a tachometer or a magnetic tach such as Dynabrade’s P/N
96368
. Before operating, we recommend that 2-3
drops of Dynabrade Air Lube P/N
95842
(or equivalent) be placed directly into the air inlet with throttle lever depressed. Operate the machine for approximately
30 seconds before application to work piece to determine if machine is working properly and safely and to allow lubrication oils to properly dispense
through machine.
Loctite
®
is a registered trademark of the Loctite Corp.
3