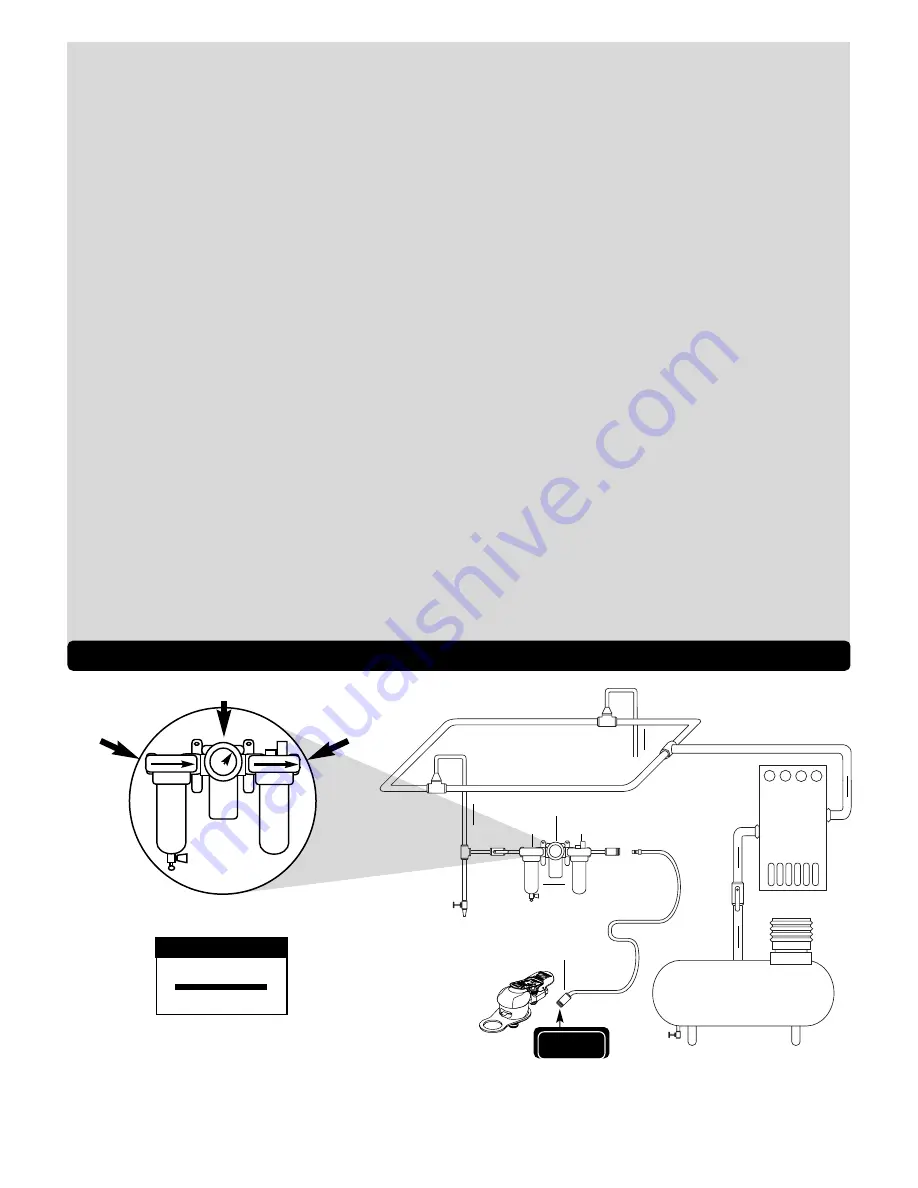
To Tool Station
Closed Loop Pipe System
(Sloped in the direction of air flow)
Ball
Valve
Ball
Valve
Filter
Coupler
Regulator
Lubricator
Air Flow
Drain
Valve
Drain
Valve
Air Tool
Air Compressor
and Receiver
Drain
Valve
Air Hose
Air Flow
Refrigerated
Air Dryer
2
Filter
Regulator
Lubricator
90 PSIG
(6.2 Bar)
SAFETY/OPERATING INSTRUCTIONS
Warnings:
• Always wear eye protection. Operator of tool is responsible for following: accepted eye, face, respiratory, hearing and body protection.
• Working end of the air tool has potential hazard of cutting.
• Be sure that any loose clothing, hair and all jewelry is properly restrained.
• Tool RPM must never exceed abrasive/accessory RPM rating. Check accessory manufacturer for details on maximum operating speed or special mounting instructions.
• Make sure that work area is uncluttered, and visitors are at a safe range from the tools and debris.
• Potentially explosive atmospheres can be caused by dust and fumes resulting from work. Always use dust extraction or suppression systems which are suitable for the
material being processed.
• Use only appropriately sized abrasive sanding discs properly secured and centered to the backing pad provided with the air sander.
• Do not free spin the tool away from the work surface with an abrasive sanding disc attached. The sanding disc may detach from the back-up pad causing injury.
• Always start the tool with the sanding abrasive against the work. Stop the air flow to the tool as it is removed from the work.
• Air tools are not intended for use in explosive atmospheres and are not insulated for contact with electric power sources.
• Work may generate hazardous dust.
• Ensure that sparks and debris resulting from work do not create a hazard.
Cautions
• Hand, wrist and arm injury may result from repetitive work, motion and overexposure to vibration.
• After installing the accessory, before testing or use and/or after assembling tool, the tool must be started at a reduced speed to check for good balance. Gradually increase
tool speed. DO NOT USE if tool vibration is excessive. Correct cause, and retest to insure safe operation.
• Release the throttle lever in case of an interruption of the energy supply.
Additional Information:
• Install air fitting into inlet bushing of tool. Important: Secure inlet bushing of tool with a wrench before attempting to install the air fitting to avoid damaging
valve body housing.
• BEFORE MOUNTING AN ACCESSORY, after all tool repairs and whenever a Mini-Dynorbital
®
Silver Supreme Sander is issued for use, check the free speed (RPM) with the
back-up pad securely fastened without any type of sanding accessory attached to the back-up pad. The air pressure must be set to 90 PSIG with the tool
running. Checking the RPM requires either a strobe or a magnetic tachometer. If tool is operating at a higher speed than the RPM marked on the tool housing, or operating
improperly, the tool must be serviced and corrected before use.
• Use only Dynabrade weight-mated pads to maintain low vibration levels.
• Connect air tool to power source. Be careful NOT to depress throttle lever in the process.
• Do not expose air tool to inlet pressure above 90 PSIG or (6.2 Bars).
• Keep hand and clothing away from working end of the air tool.
• Proceed with caution in unfamiliar surroundings. Hidden hazards may exist, such as electricity or other utility lines.
• Always be aware of bystanders in work areas.
• Use a vise or clamping device to hold work piece firmly in place.
• Do not apply excessive force on tool or apply “rough” treatment to it.
• When applying the sander to a work surface
start-on
and
stop-off
when completed.
• Always work with a firm footing, posture and proper lighting.
• Disconnect tool from air supply when changing recommended accessories.
• This tool is rear exhaust. Exhaust may contain lubricants, vane material, bearing grease, and other materials flushed thru the tool.
Report to your supervisor any condition of the tool, accessories, or operation you consider unsafe.
Air System
1
DROP/MIN.
20
SCFM
LUBRICATOR SETTING
•
Ideally the air supply should be free of moisture.
To facilitate removing moisture from air supply, the
installation of a refrigerated air dryer after the
compressor and the use of drain valves at each
tool station is recommended.
•
Dynabrade Air Power Tools are designed to
operate at 90 PSIG (6.2 Bar/620 kPa) maximum
air pressure at the tool inlet, when the tool is
running. Use recommended regulator to control
air pressure.
➤
➤
➤
➤
➤
➤
90 PSIG MAX
(6.2 Bar)