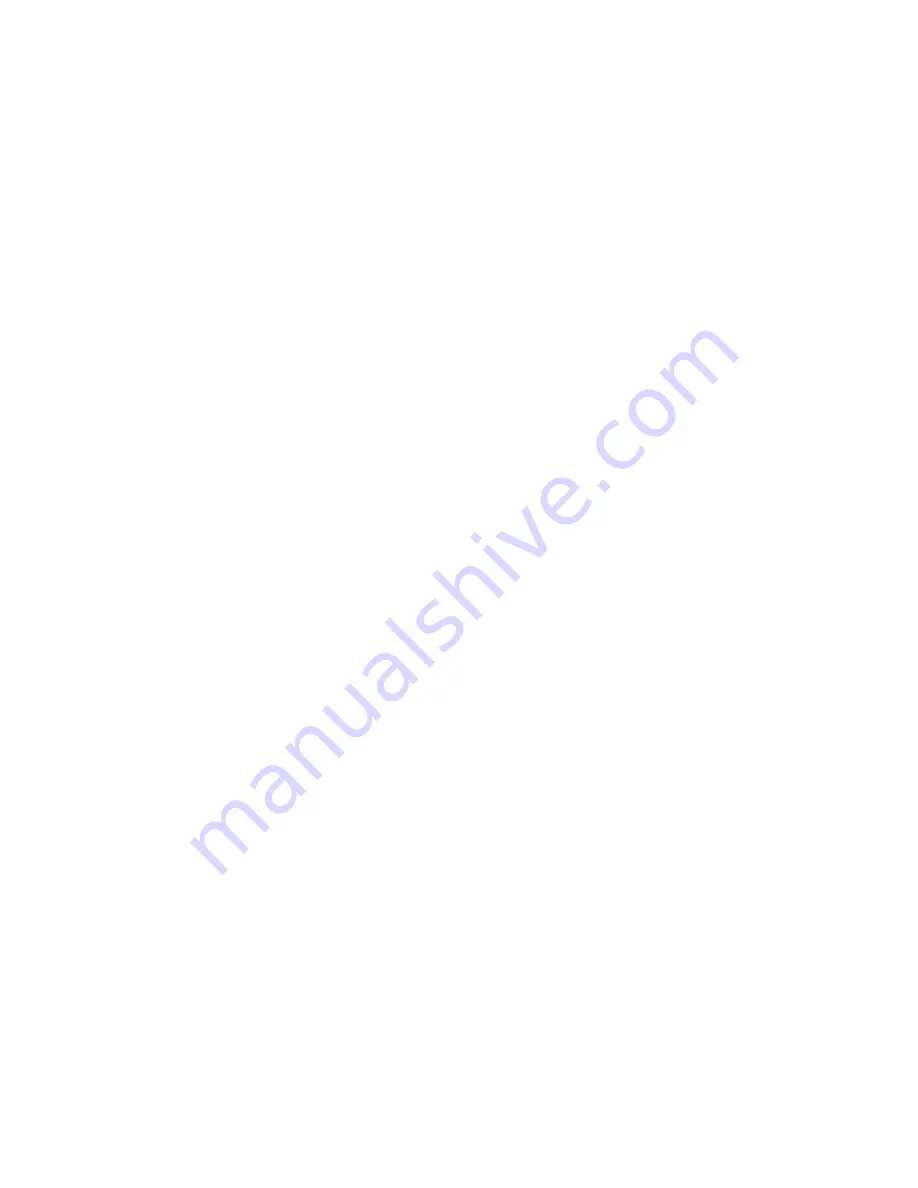
Disassembly Instructions - 1 Hp Dynastraight
I
mportant: Manufacturer’s warranty is void if tool is disassembled before warranty expires.
Disconnect tool from power source before tool repair.
Motor Disassembly:
1. Remove arbor assembly from front of tool.
2. Using 51989 Repair Collar or padded vise, secure front end of housing using machined flats on the silver ring.
3. Remove planetary gear casing from housing (twist counterclockwise).
4. Remove 04014 Set Screw(s) and pull planetary carrier assembly(s) from planetary gear casing.
5.
Press planetary carrier assembly from rear 02552 Bearing. Remove ring gear and gears from planetary carrier(s).
6. Secure planetary carrier in vise and remove 04032 Spindle Nut (twist counterclockwise).
7. Press planetary carrier from front 02552 Bearing.
Note: On double planetary models slide, bearing/carrier from 53694 Gear Casing. Then press planetary carrier through 02552
bearing. Press 53678 Gear Shaft from carrier assembly. Remove ring gear from the housing assembly.
8. Remove remaining tool assembly from vise.
9. Remove 96498 Wave Spring. (Single planetary models only.)
10. Pull motor assembly, and remove 53620 Motor Adapter with 95438 O-Ring.
11. Remove governor assembly by using a slotted screw driver. (LEFT HAND thread)
12. Secure 51925 Cylinder and place a 1/8" (3 mm) drift pin to the base of the internal thread and press the 51921 Rotor from
the 02057 Rear Bearing.
13. Slide 02057 Rear Bearing from 51923 Rear Bearing Plate.
14. Remove 51925 Cylinder and 51926 Blades.
15. Press rotor though 54520 Bearing, 51922 Front Bearing Plate and 51927 Rotor Spacer.
16. Slide 54520 Bearing and shims from 51922 Front Bearing Plate.
Motor Disassembly Complete.
Housing Disassembly:
1. Secure housing using 51989 Repair Collar (see back cover for Optional Accessories).
2. Remove 51937 Inlet Bushing (twist counterclockwise).
3. Remove 51943 Spring, 96442 O-Ring, 51940 Spacer and 51939 Silencer Plate from 51937 Inlet Bushing.
4. Remove 51941 Spring, 51942 Baffle, 51944 Tip Valve and 51945 Valve Seat.
5. Remove housing and 51989 Repair Collar and lay collar on bench with flange facing down so it is supporting throttle lever. Place a 3/32"
(2.4 mm) drift pin on 96444 Pin and tap thru housing.
6. Remove 51946 Valve Stem Assembly.
7. Remove 96443 O-Ring from 51946 Valve Stem Assembly.
Housing Disassembly Complete.
Assembly Instructions - 1 Hp Dynastraight
Motor Assembly:
Important: Be sure parts are clean and in good repair before assembling. Follow grease, oil and torque specifications.
1. Place rotor into padded vise with male thread or spline facing upwards.
2. Slip 51927 Rotor Spacer over rotor shaft and down against rotor body face.
3. Press 96441 Coiled Pin into 51922 Front Bearing Plate. Make certain, coiled pin does not protrude beyond
internal bearing surface.
4. Place a .002" shim into the base of 51922 Front Bearing Plate as an initial spacing and slide 54520 Bearing to the front plate
base. Note: 51951 Shim Pack contains .001" and .002" shims.
5. Press bearing/bearing plate assembly onto rotor.
6. Check clearance between rotor and front bearing plate by using a .001" feeler gauge. Clarence should be between .001" – .0015".
Adjust clarence by repeating steps 4 and 5 with different shims if necessary.
7. Once proper rotor gap clarence is achieved, install well lubricated 51926 Blades (4) into rotor slots. Dynabrade
recommends lubricating blades with 95842 Air Lube.
8. Install 51925 Cylinder over rotor and front plate raised boss. Align coiled pin on front to cylinder slot.
9. Press 96441 Coiled Pin into blind hole on 51923 Rear Bearing Plate. Press (2) 96445 Coiled Pins into the back side of
rear bearing plate.
10. Peel backing off 51924 Gasket and align it firmly in place onto 51923 Rear Bearing Plate.
11. Place 51923 Rear Bearing Plate over rotor mandrel and insert raised boss on rear bearing plate into cylinder diameter, while inserting
short coiled pin into cylinder slot. Be sure inlet slot on rear bearing plate line up with inlet slot on cylinder. To correct alignment flip
cylinder end to end and repeat step 8 for correct assembly.
(Continued on next page.)
5
Buy parts on line at https://Dynashop.co.uk/ for all things Dynabrade
Buy parts on line at https://Dynashop.co.uk/ for all things Dynabrade