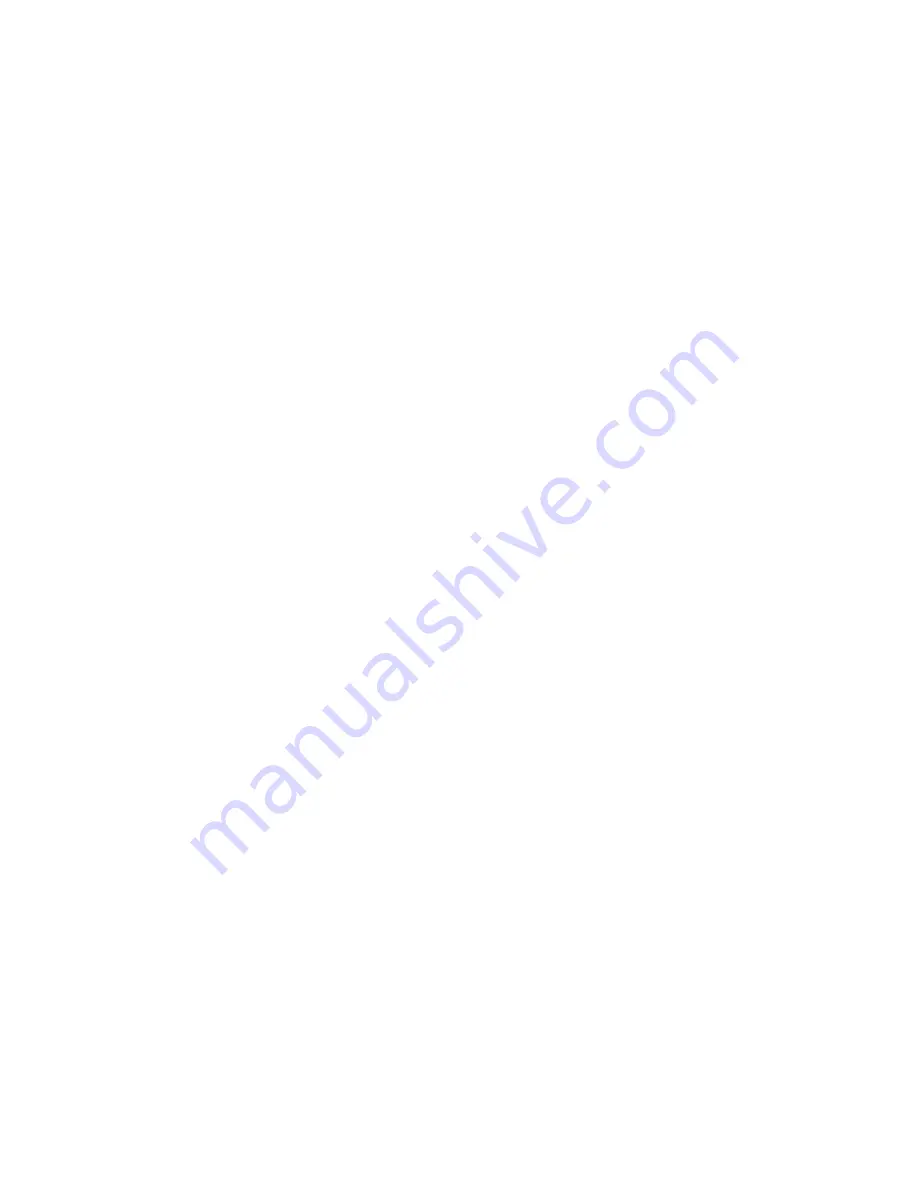
Disassembly/Assembly Instructions
Important: Manufacturer’s warranty is void if tool is disassembled before warranty expires.
A Motor Tune-Up Kit is available (P/N 96011) to help maintain motor in peek operating condition.
Tool Disassembly:
1.
Disconnect tool from power source.
2.
Remove any abrasive belt from machine.
3.
Roll
07136
Handle Grip away from
07086
Adapter to expose wrench flats.
4.
Remove
07086
Adapter from housing (right hand thread). Separate
07167
Throttle Valve Assembly from machine assembly.
5.
Insert
01697
Inlet Bushing securely into vise.
6.
Remove
02631
Nut by using a 32 mm wrench.
7.
Remove
01794
Drive Wheel with a 19 mm wrench.
8.
Remove
95221
Screws (4) and disconnect
07102
Motor Assembly from machine housing.
9.
Place
07102
Motor Assembly housing in soft jaw vise.
Important:
Be careful not to over tighten vise to prevent damage.
10.
Remove
01790
Screws (4) and
01791
Washers (4) from
07122
Housing Cap. Remove housing cap and
07129
Gasket.
Motor Disassembly:
1.
Fasten a 2 in. bearing separator around the rear portion of the
07118
Cylinder and using a #2 arbor press (P/N
96232
available) place the separator on
the table of the arbor press so that the motor spindle points toward the floor.
2.
Use a 3/16 in. Dia. flat nose drive punch as a press tool and push against the rear shaft of the rotor to remove rear bearing/plate assembly.
3.
Hold the body of the
07103
Rotor in a soft (aluminum or bronze) jaw vise and remove
02553
Adapter.
4.
Remove
07119
Front Bearing Plate,
01036
Front Bearing from
07103
Rotor.
Note:
Bearing, front bearing plate are a slip fit onto rotor.
5.
Push
01036
Bearing Plate and remove shims from front bearing plate.
Motor Disassembly Complete.
Motor Assembly:
Important:
Be certain all parts are cleaned and in good repair before assembling.
1.
Place
07103
Rotor in soft (aluminum or bronze) jaw vise with threaded spindle pointing upwards.
2.
Place .002" shim into front bearing plate as initial spacing and slip
01036
Bearing into plate.
Note: 01277
Shim Pack contains .001" and .003" shims.
3.
Install bearing/bearing plate assembly onto rotor.
4.
Install
02553
Adapter onto assembly.
5.
Tighten
02553
Adapter onto rotor, torque 23 N•m/200 in. - lbs.
6.
Check clearance between rotor and bearing plate by using a .001" feeler gauge. Clearance should be at .001" to .0015". Adjust clearance by repeating
steps 1-5 with different shims if necessary.
7.
Once proper rotor/gap clearance is achieved, install lubricated
07107
Blades (5) into rotor slots. Dynabrade Air Lube P/N
95842
(or equivalent) is
recommended for lubrication before installation in rotor slots.
8.
Install cylinder over rotor.
9.
Press the
01007
Rear Bearing into
07114
Rear Bearing Plate. Press bearing/bearing plate assembly onto rotor. Be sure that pin and air inlet line-up
with pin hole and air inlet in cylinder.
10.
Place
95584
O-Ring
01674
Silencer and
07153
Exhaust Ring into housing.
11.
Slide motor assembly into motor housing.
12.
Install
07129
Gasket and
07122
Housing Cap with
01790
Screws (4) and
01791
Washers (4), tighten screws to 9 N•m/80 in. - lbs.
13.
Motor adjustment can now be checked. With motor housing still mounted in vise, pull end of rotor and twist (10-15 lbs. force), rotor should turn
freely without drag. If drag or rub is felt, then increase preload or remove shim. Also, push end of rotor and twist (10-15 lbs. force), rotor should
turn freely without drag. If drag or rub is felt, then deload or add a shim.
14.
Install
95221
Screws (4) to connect
07102
Motor Assembly onto machine housing.
15.
Apply 2 drops of #271 Loctite
®
(or equivalent) to threads of
02626
Adjustment Bushing before tightening.
16.
Slip
02626
Adjustment Bushing through
02631
Nut and
02658
Packing, and secure into
07886
Adapter.
17.
Apply Loctite
®
#271 (or equivalent) and tighten
02626
Adjustment Bushing into housing torque to 50 N•m/450 in. - lbs.
18.
Apply Loctite
®
#567 (or equivalent) to threads of
07141
Valve Body, and fasten
02631
Nut and
01746
O-Ring onto valve body. Swivel
07141
Valve Body
to desired throttle lever position.
19.
Tighten
02631
Nut to 45 N•m/400 in. - lbs. Roll
07136
Grip back into place.
Tool Assembly Complete. Please allow 30 minutes for adhesives to cure before operating tool.
Important:
Motor should now be tested for proper operation at 90 PSIG. If motor does not operate properly or operates at a higher RPM than marked on the
tool, the tool should be serviced to correct the cause before use. Before operating, place 2-3 drops of Dynabrade Air Lube (P/N
95842
) directly into air inlet
with throttle lever depressed. Operate tool for thirty seconds to determine if tool is operating properly and to allow lubricating oils to properly penetrate motor.
Loctite
®
is a registered trademark of Loctite Corp.
6