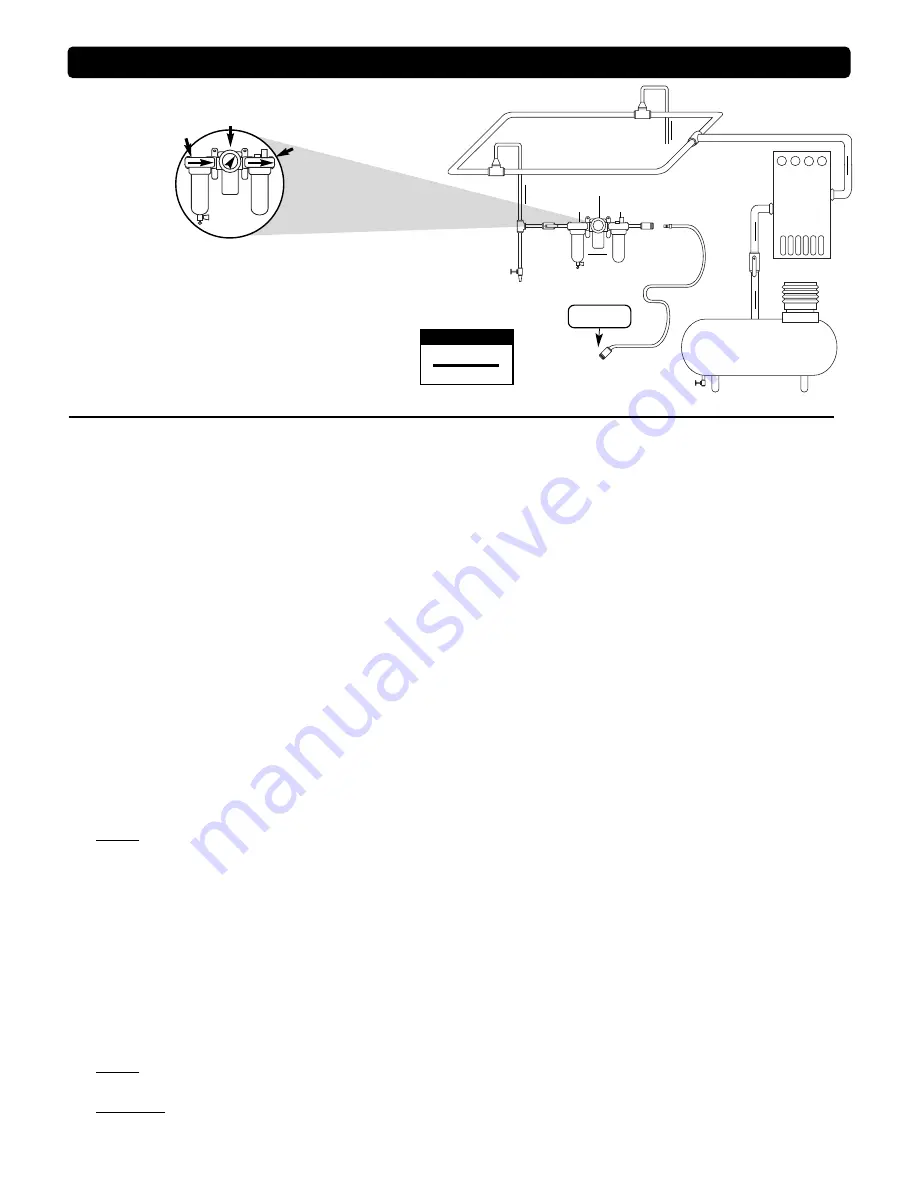
3
Maintenance Instructions
Important:
To keep tool safe a Preventative Maintenance Program is recommended whenever portable power tools are used. The program should include
inspection of air supply lines, air line pressure, proper lubrication and repair of tools. Refer to ANSI B186.1 for additional maintenance information.
•
Use only genuine Dynabrade replacement parts to ensure quality. To order replacement parts, specify
Model#
,
Serial#
and
RPM
of your air tool.
•
It is strongly recommended that all Dynabrade rotary vane air tools be used with a Filter-Regulator-Lubricator to minimize the possibility of misuse due to
unclean air, wet air or insufficient lubrication. Dynabrade recommends the following:
10681
Air Line Filter-Regulator-Lubricator — Provides accurate air
pressure regulation, two-stage filtration of water contaminants and micro-mist lubrication of pneumatic components. Delivers up to 55 SCFM/1,558 LPM
@ 145 PSIG/9.7 Bar (Max. Air Temperature of 140˚F/60˚ C)
Note:
Two (2) 3/8" NPT Reducer Bushings are included.
•
Dynabrade recommends one drop of air lube per minute for each 20 SCFM (example: if the tool specification states 40 SCFM, set the drip rate on the
filter-lubricator to 2 drops per minute). Dynabrade Air Lube (P/N
95842
: 1 pt 473 ml) is recommended.
•
Lubricate the planetary gears through the grease fitting located in the gear/planetary cover. Apply 2-3 plunges* for every 50 hours of use, to achieve
maximum gear life. (*order
95542
Grease and
95541
Gun)
Routine Preventative Maintenance:
•
Check free speed of tool regularly using a tachometer without the abrasive accessory mounted. After all tool repairs and whenever a .4 hp Vacuum Die
Grinder is issued for use, check tool RPM (speed) with tachometer with air pressure set at 90 PSIG while the tool is running. If tool is operating at a higher
speed than the RPM marked on the tool housing, operating improperly or demonstrates unusual vibration, the tool must be serviced and corrected before use.
•
Inspect accessories before mounting. Do not mount accessories that are damaged or nicked.
•
Check accessory - speed rating. Rating on accessory must be greater than the tool speed marked on the housing.
•
If accessory breakage occurs, investigate to determine the cause and correct before issuing tool for work.
•
Mineral spirits are recommended when cleaning the tool and parts. Do not clean tool or parts with any solvents or oils containing acids, esters, ketones,
chlorinated hydrocarbons or nitro carbons.
•
DO NOT clean or maintain tools with chemicals that have a low flash point (example: WD-40
®
).
•
Motor Tune-Up Kits (P/N
96174, 96049,
see back page) are available, they includes high wear and medium wear motor parts.
•
Air tool markings must be kept legible at all times, if not, reorder housing and replace. User is responsible for maintaining specification information
i.e.: Model #, S/N, and RPM. (See Assembly Breakdown)
•
Blow air supply hose out prior to initial use.
•
Visually inspect air hoses and fittings for frays, visible damage and signs of deterioration. Replace damaged or worn components.
•
Refer to Dynabrade's Warning/Safety Operating Instructions Tag (Reorder No.
95903
) for safety information.
After maintenance is performed on tool, add a few drops of Dynabrade Air Lube (P/N
95842
) to the air line and start the tool a few times to lubricate air motor.
Check for tool vibration before mounting abrasive wheel accessory.
Handling and Storage:
•
Use of tool rests, hangers and/or balancers is recommended.
•
Protect tool inlet from debris (see Notice on Page 6).
•
DO NOT carry tool by air hose or near the tool throttle lever.
•
Protect tool from exposure to water, solvents, high humidity, freezing temperature and extreme temperature changes.
•
DO NOT USE accessories that have been dropped or show signs of cracks, nicks or other defects.
•
Store accessories in protective racks or compartments to prevent damage.
Air System
Filter
Regulator
Lubricator
90 PSIG
(6.2 Bar)
To Tool Station
Closed Loop Pipe System
(Sloped in the direction of air flow)
Ball
Valve
Ball
Valve
Filter
Regulator
Lubricator
Air Flow
Drain
Valve
Drain
Valve
Air Tool
Air Compressor
and Receiver
Drain Valve
Air Hose
90 PSIG MAX
(6.2 Bar)
Air Flow
Refrigerated
Air Dryer
1
DROP/MIN.
20
SCFM
LUBRICATOR SETTING
➤
➤
➤
➤
➤
➤
•
Dynabrade Air Power Tools are designed to operate at
90 PSIG (6.2 Bar) maximum air pressure at the tool inlet,
when the tool is running. Use recommended regulator
to control air pressure.
•
Ideally the air supply should be free from moisture. To facili-
tate removing moisture from air supply, the installation of a
refrigerated air dryer after the compressor and the use of
drain valves at each tool station is recommended.