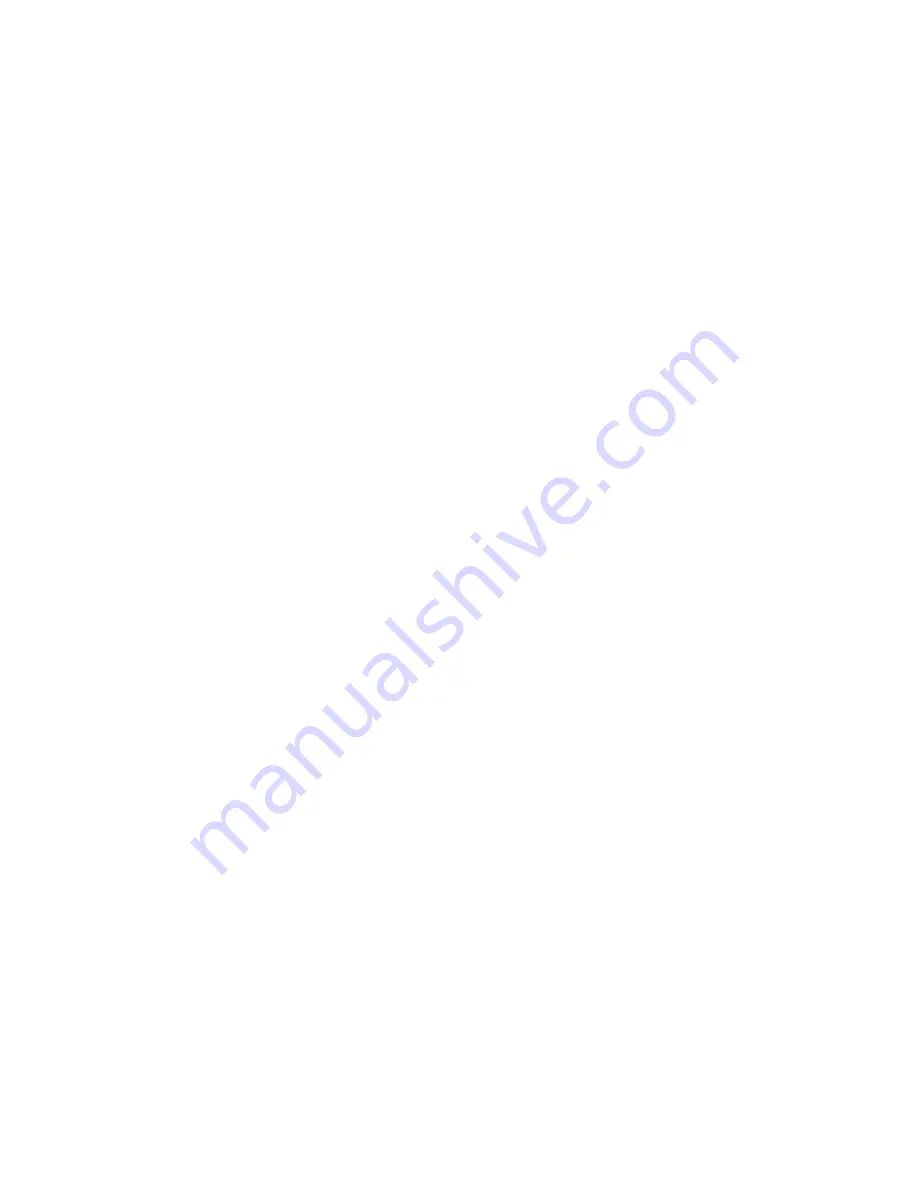
Disassembly Instructions - 1 Hp Cut-Off Tool
I
mportant: Manufacturer’s warranty is void if tool is disassembled before warranty expires.
Disconnect tool from power source before tool repair.
Motor Disassembly:
1. Remove 50269 Flange (2) and 53654 Wheel Guard.
2. Secure front end of housing in a soft (aluminum or bronze jaw) vice, align the vise jaws with machined flat on the silver ring.
3. Using 50971 Pin Wrench (order separately) or an adjustable pin wrench, remove 51961 Housing Cover.
4. Remove remaining assembly from vise.
5. Remove 96498 Wave Spring.
6. Pull Motor Assembly from housing assembly, and remove 53620 Motor Adapter with 95438 O-Ring.
7. Remove Governor Assembly by using a slotted screw driver. (LEFT HAND thread)
8. Secure 51925 Cylinder and place a 1/8" (3 mm) drift pin to the base of the internal thread and press the 51921 Rotor from
the 02057 Rear Bearing.
9. Slide 02057 Rear Bearing from 51923 Rear Bearing Plate.
10. Remove 51925 Cylinder and 51926 Blades.
11. Secure 51921 Rotor in a soft (aluminum or bronze jaw) vise and remove 51986 Rotor Nut (twist counterclockwise).
12. Slide 51922 Front Bearing Plate and 51927 Rotor Spacer from 51921 Rotor.
13. Slide 54520 Bearing and shims from 51922 Front Bearing Plate.
Motor Disassembly Complete.
Housing Disassembly:
1. Secure housing using 51989 Repair Collar (order separately–see back cover for Optional Accessories).
2. Remove 51937 Inlet Bushing (twist counterclockwise).
3. Remove 51943 Spring, 96442 O-Ring, 51940 Spacer and 51939 Silencer Plate from 51937 Inlet Bushing.
4. Remove 51941 Spring, 51942 Baffle, 51944 Tip Valve and 51945 Valve Seat.
Disassembly Complete.
Assembly Instructions - 1 Hp Cut-Off Tool
Motor Assembly:
Important: Be sure parts are clean and in good repair before assembling. Follow grease, oil and torque specifications.
1. Place 51921 Rotor into a padded vise with male thread facing upwards.
2. Slip 51927 Rotor Spacer over rotor shaft and down against rotor body face.
3. Press 96441 Coiled Pin into 51922 Front Bearing Plate. Make certain, coiled pin does not protrude beyond internal
bearing surface.
4. Place a .002" Shim into the base of 51922 Front Bearing Plate as an initial spacing and slide 54520 Bearing to the
front plate base.
Note: 51951 Shim Pack contains .001" and .002" Shims.
5. Slip bearing/bearing plate assembly onto rotor, torque 51986 Rotor Nut onto rotor shaft to 17 N•m (150 lb.-in.).
6. Check clearance between rotor and front bearing plate by using a .001" feeler gauge. Clearance should be between
.001" - .0015". Adjust clearance by repeating steps 4 and 5 with different shims if necessary.
7. Once proper rotor gap clearance is achieved, install well lubricated 51926 Blades (4) into rotor slots. Dynabrade
recommends lubricating blades with 95842 Air Lube.
Important: Make certain beveled edge of blade follows rotor outside diameter.
8. Install 51925 Cylinder over rotor and front plate raised boss. Align coiled pin on front plate to cylinder slot.
9. Press 96441 Coiled Pin into blind hole on 51923 Rear Bearing Plate. Press (2) 96445 Coiled Pins into the back side of rear
bearing plate.
10. Peel backing off 51924 Gasket and align it firmly in place onto 51923 Rear Bearing Plate.
11. Place 51923 Rear Bearing Plate over rotor mandrel and insert raised boss on rear bearing plate into cylinder diameter, while
inserting short coiled pin into cylinder slot. Be sure inlet slot on rear bearing plate line up with inlet slot on cylinder. Flip
cylinder end to end and repeat step 8 for correct assembly.
(Continued on next page)