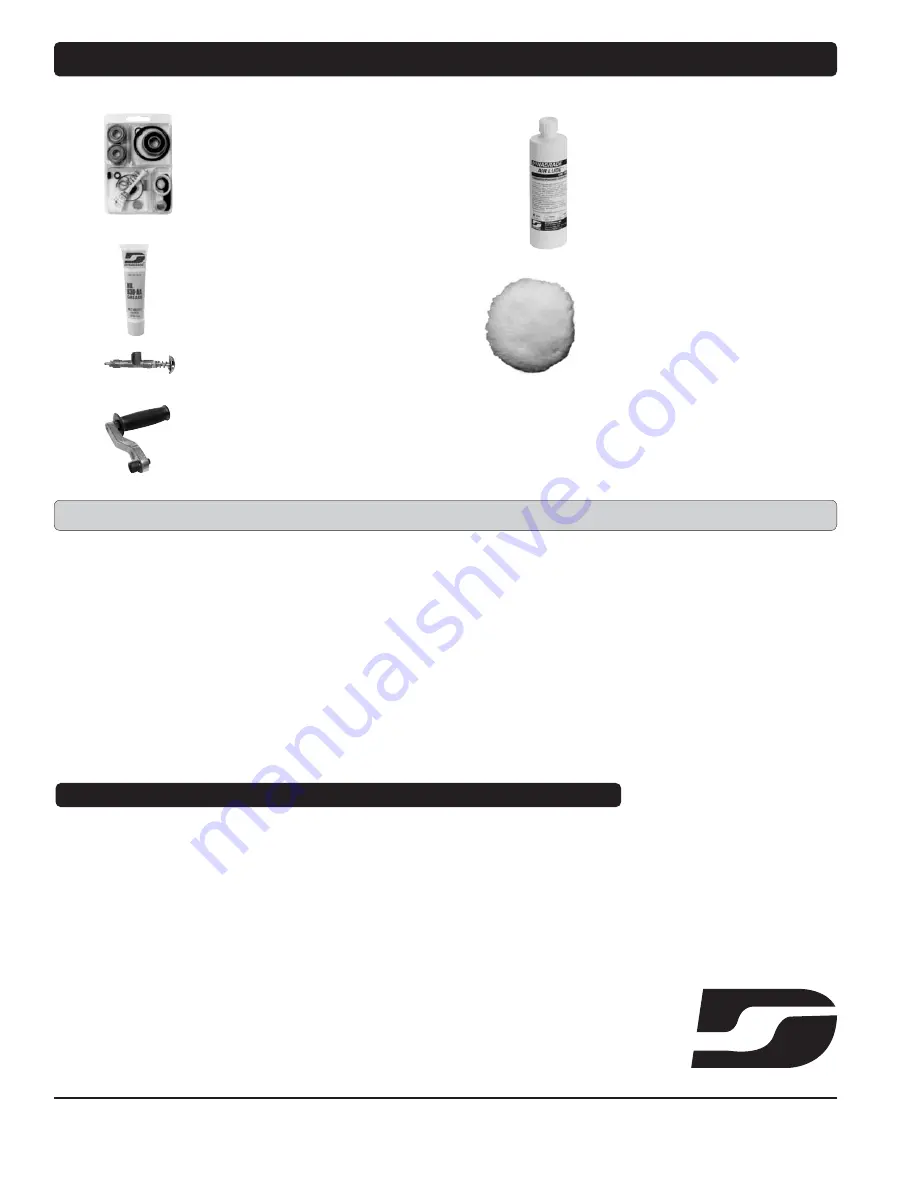
DYNABRADE
®
DYNABRADE, INC.,
8989 Sheridan Drive
•
Clarence, NY 14031-1490
•
Phone: (716) 631-0100
•
Fax: 716-631-2073
•
International Fax: 716-631-2524
DYNABRADE EUROPE S.àr.l.,
Zone Artisanale
•
L-5485 Wormeldange—Haut, Luxembourg
•
Telephone: 352 76 84 94 1
•
Fax: 352 76 84 95 1
© DYNABRADE, INC., 2008
PRINTED IN USA
Visit Our Web Site:
www.dynabrade.com
Email:
98224 Motor Tune-Up Kit
•
Includes assorted parts to
help maintain and repair motor.
53147 Top Mount Handle Assembly
•
Allows side handle to be centered over the
top of the working end of the tool.
90082 Natural Sheepskin Polishing Pad
Dynabrade Air Lube
•
Formulated for pneumatic equipment.
•
Absorbs up to 10% of its weight in water.
•
Prevents rust and formation of sludge.
•
Keeps pneumatic tools operating longer
with greater power and less down time.
95842:
1pt. (473 ml)
95843:
1gal. (3.8 L)
Note:
Not Shown, Mentioned In Assembly/Disassembly Instructions
96242
Bearing Press Tool
96232
(#2) Arbor Press
96346
(2”) Bearing Separator
96213
Bearing Removal Tool
96240
Bearing Press Tool
96231
Tool Plate
95331
4mm Hex
Optional Accessories
Special Repair Tools
95542 Grease 10 oz.
•
Multi-purpose grease for all types of
bearings, cams, gears.
•
High film strength; excellent resistance
to water, steam, etc.
•
Workable range 0˚ F to 300˚ F.
95541 Push-type Grease Gun
•
One-hand operation.
FIND THE MOST CURRENT OFFERING OF SUPPORT DOCUMENTS AND ACCESSORIES @ WWW.DYNABRADE.COM
Reference Contact Information
1. American National Safety Institute – ANSI
25 West 43
rd
Street
Forth Floor
New York, NY 10036
Tel: 1 (212) 642-4900
Fax: 1 (212) 398-0023
2. Government Printing Office – GPO
Superintendent of Documents
Attn. New Orders
P.O. Box 371954
Pittsburgh, PA 15250-7954
Tel: 1 (202) 512-1803
3. European Committee for Standardization
Rue de Stassart 36
B - 1050 Brussels, Belgium