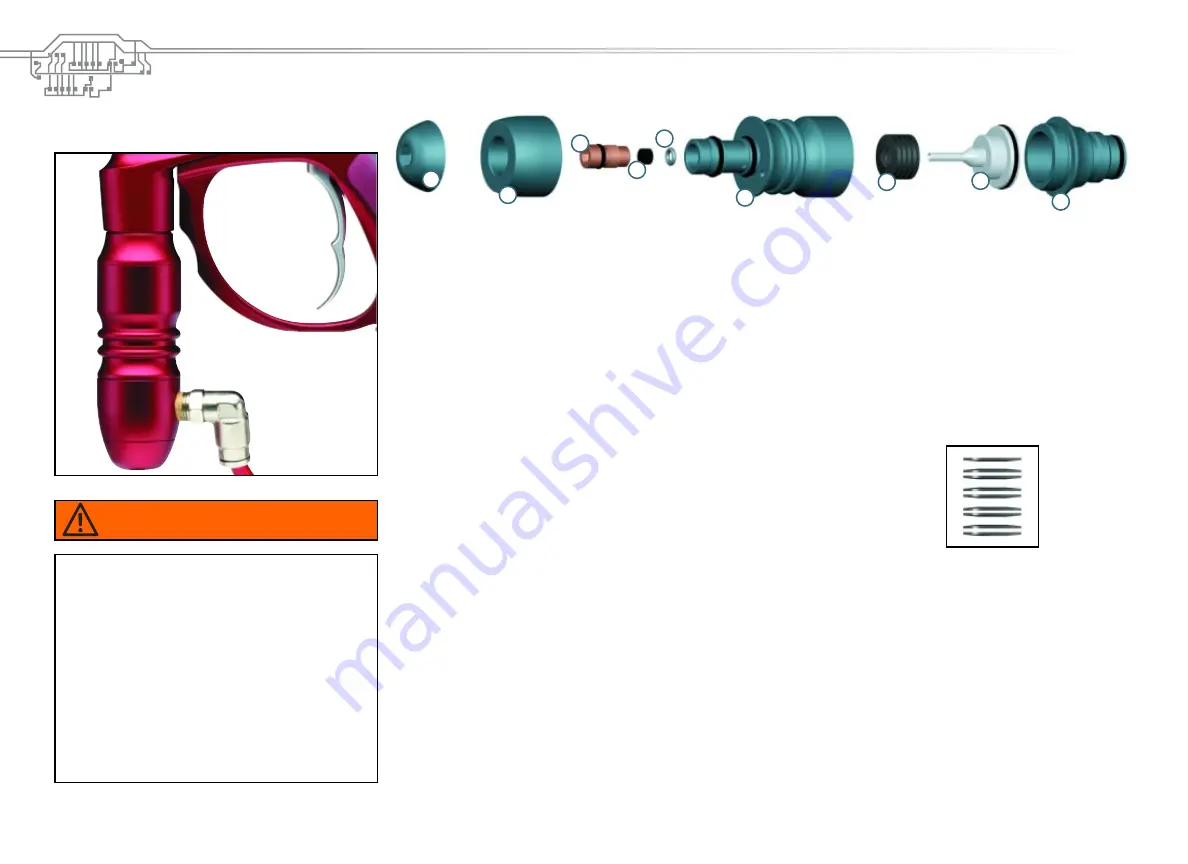
HYPER
2
IN-LINE REGULATOR
- Adjustments and Maintenance
• The Hyper
2
can hold a small residual charge
of gas, typically 2 shots. Always discharge
the marker in a safe direction to relieve this
residual gas pressure.
• Always remove the regulator from the
DM5 before servicing.
• Improper stacking of shims will cause
failure of the regulator and possible
damage to the DM5.
• Excessive dirt and debris can affect
the Hyper
2
’s performance and increase
the need for servicing.
W A R N I N G
USAGE
Carefully connect your air hose from your bottle or air system to the Hyper
2
In-Line. The Hyper
2
In-Line is set by the factory to
approximately 170psi. This pressure should give you a velocity of approximately 285fps.
ADJUSTMENTS
The output pressure of the Hyper
2
In-Line is adjusted by turning the brass seat housing. The seat housing screw is located up
inside the bottom of the reg. A 3/16” Allen wrench will be needed for this operation. By turning the housing counter-
clockwise, you will increase the output pressure of the reg to the marker. By turning the housing clockwise, you will decrease
the output pressure of the reg.
After each adjustment of the output pressure of the Hyper
2
In-Line, you will need to cycle your marker a few times. This will
allow your marker and air system to stabilize at their new operating pressure. The Hyper
2
will need a break-in period of about
2,500 shots to let its seat form to the piston and reach its optimum performance.
The Hyper
2
has nine components
1
Retaining cap
6
Reg body
2
Swivel
7
Shims
3
Seat housing
8
Piston
4
Seat
9
Reg cap
5
Piston o-ring
Disassembly of the Hyper
2
In-Line is easily done with 3/8” and 5/16” Allen wrenches.
MAINTENANCE
To ensure top performance from the Hyper
2
, maintenance should be performed every four months or sooner, depending on
the severity of playing conditions. Cold, wet weather will shorten the effective life of the grease. Heavy dust or fine sand can
infiltrate the Hyper
2
and prevent the piston from moving smoothly and/or cut the o-rings.
1
Make sure the inlet and outlet ports and connecting fittings are free of all dirt and paint.
2
Examine all o-rings for nicks or cuts.
3
Carefully inspect the seat for excessive wear that might cause spiking and over-pressurizing.
4
Clean any accumulated dirt out of the air chambers and passages.
5
Keep the piston o-rings and spring pack generously greased to allow smooth velocity adjustment and prevent
erratic velocity spikes and drop off.
6
Clean off all old grease that may be contaminated with dirt; reapply fresh grease to the piston and other necessary areas.
7
Be sure to reassemble the internal components and shim stack
(see figure 2)
in the proper order and direction.
8
See diagram for assistance.
W
W
W
.
D
Y
E
M
A
T
R
I
X
.
C
O
M
1
2
3
4
5
6
7
8
9
Figure 1
Figure 2
Shim Stack
Summary of Contents for DM5
Page 1: ... ...