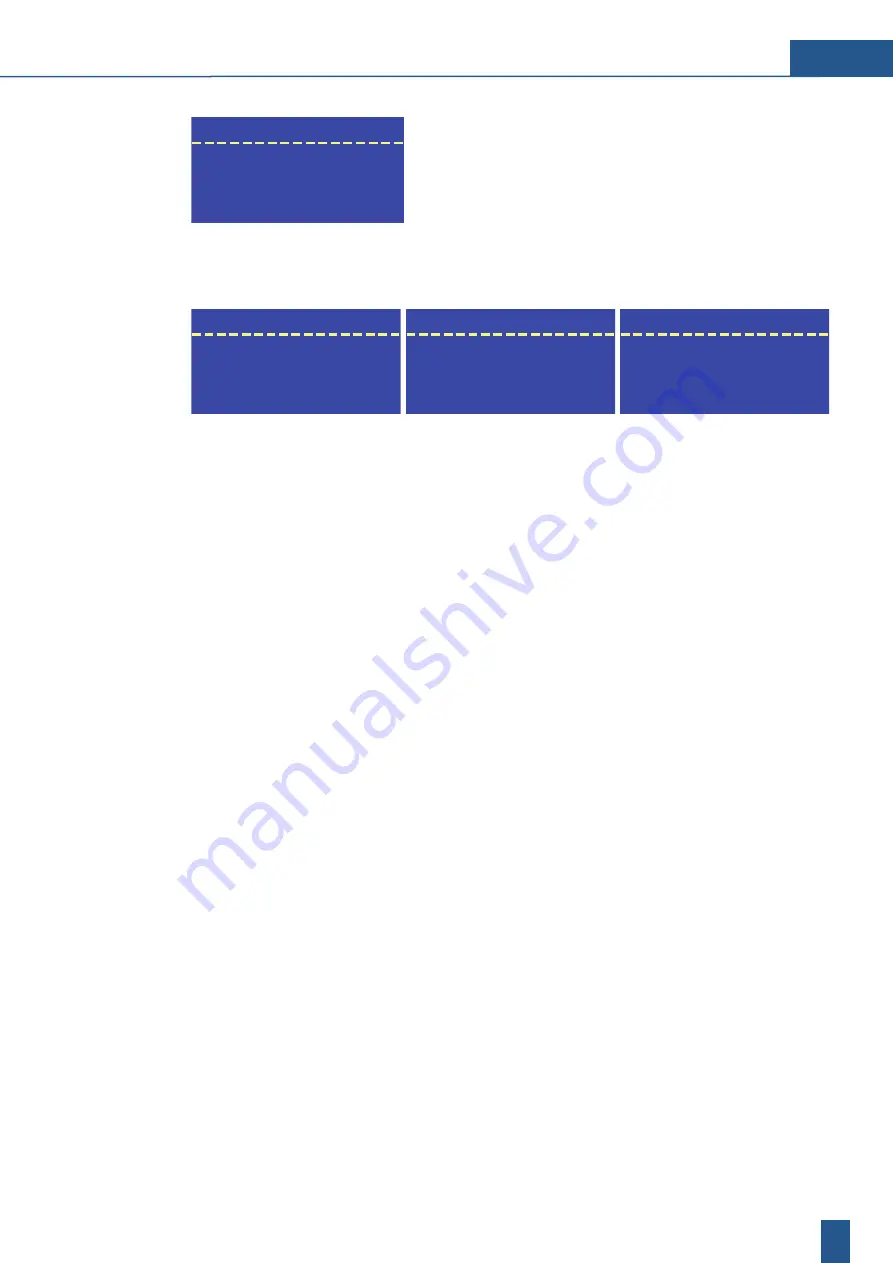
OPM BWT PERMAQ® Pico Rev. 2.0 EN
Maintenance and servicing | 8
EN
39
2) Confirm the question
agent filled in?
using the
OK
button.
Disinf. / Clean.
agent filled in?
back
DISINFECTION int.
ð
The disinfection programme starts automatically.
3) During step
S1 Charging
, open the ventilation valve on the high-pressure pump until all
the air has escaped from the pump pressure tube and only water now escapes. Close the
ventilation valve again.
DISINFECTION int.
S1 Charging
Remain. time: [ _ _ : _ _ ] s
DISINFECTION int.
S2 Reaction time
Remain. time: [ _ _ : _ _ ] s
OFF
INSPECTION MODE >
DISINFECTION int. >
DISINFECTION ext. >
Number of cycles
Number of cycles
ð
The disinfection programme continues automatically.
4) Once the disinfection programme is complete, use the peroxide test strips to check
whether all the disinfectant, which contains peroxide, has been completely flushed out of
the system. If peroxide can still be detected, restart the
DESINFECTION int
programme
without any chemical disinfectant.
5) Once no more peroxide can be detected, reconnect the permeate connection on the
device to the permeate tank.
6) Restart the device.
ð
The device is disinfected.
8.4 Chemical cleaning of the RO module
Following a hardness breach in the softener, an inadequate AS dosage or over the course of
the device service life, deposits (scaling) form on the concentrate side of the RO module,
which gradually reduces the permeate output. This undesirable process of deposition can be
counteracted to some extent by using the chemical cleaning agent Osmoclean C (liquid).
Preparing for cleaning
When a cleaning cycle is carried out for the first time, we recommend setting the step
Char-
ging
in the programme to a maximum of eight seconds.
Perform the following steps to prepare the device for cleaning:
1) Open the device door.
2) Switch off the device at the
main switch
.
ð
Wait for two to three minutes until the pressure is released.
3) Unscrew the filter housing with the supplied filter key.
CAUTION! Filter housing is filled
with water.
4) Empty and clean the filter housing.
5) Remove the old pre-filter and insert the new pre-filter into the filter housing.
6) Fill the quantity of Osmoclean C stipulated in
Table 7: Dosage of chemical clean-
ing agent [
}
000] between the filter and the filter housing.
7) Insert the housing with the pre-filter into the filter head. Ensure that it is centred correctly
during the insertion.
8) Screw on the filter housing again by hand.
9) Disconnect the permeate hose from the permeate tank inlet and guide it to the waste wa-
ter connection with the “free run-off”.
10
)
Close the device door.
11)Switch on the device at the
main switch
.