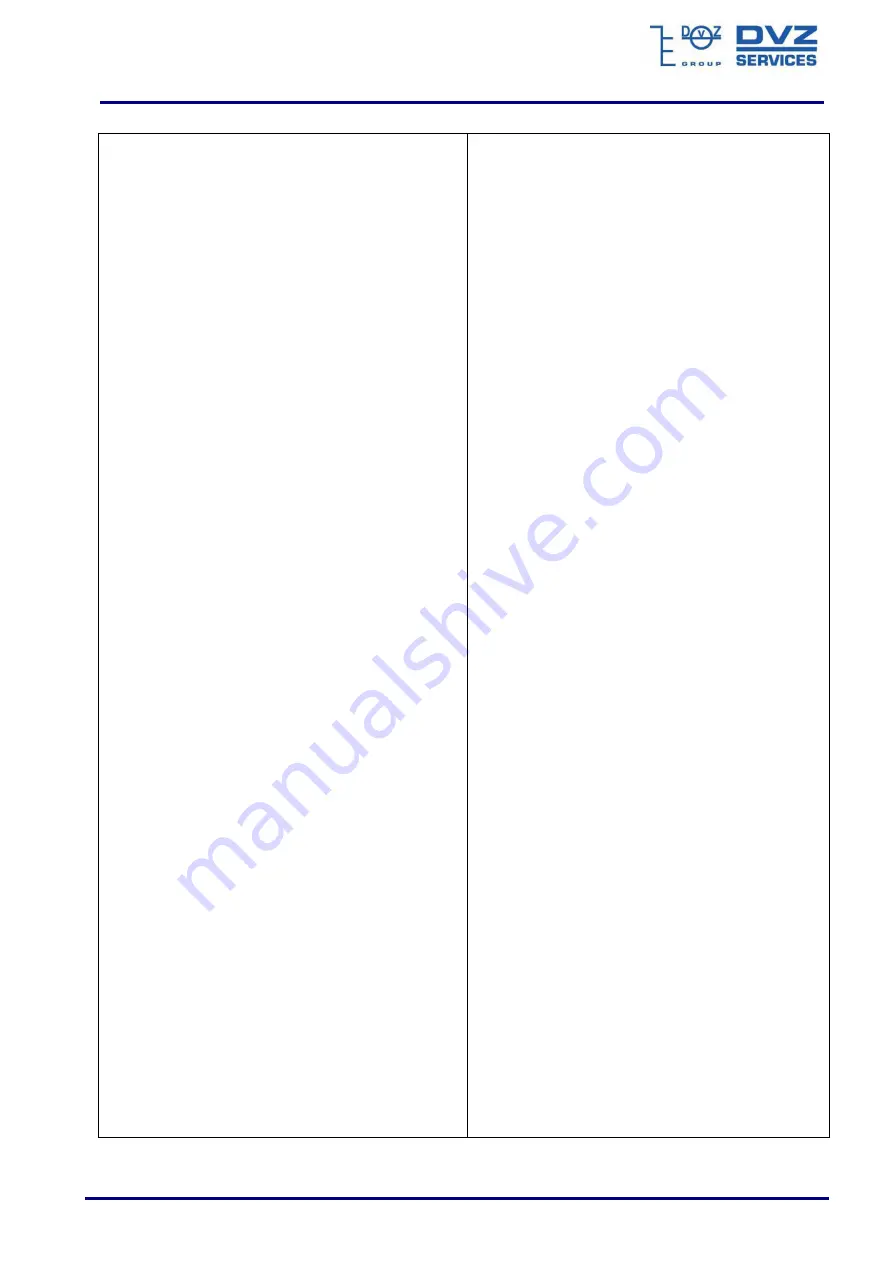
Issue: 18.10.2011
DVZ-SKA-”BIOMASTER”-PLUS – Pump P2
Page 4 of 6
SKA-PLUS-ANNEX P5-Eng
installation of compensators) must be taken to keep any
thermal stress occurring in the pipework away from the
pump.
Cleaning the pipework before connection
The suction pipework, the gate valves and shut-off valves
must be flushed and/or cleaned before installation of the
pump.
Items left over from installation, such as screws, nuts,
welding beads, metal items, etc. will damage the internal
elements of the pump. Any damage caused by such items
is not covered by our warranty. Flange gaskets must not
protrude inwards. Blanking flanges, plugs, protective film
and/or protective paint on flanges and seals must be
removed completely.
Installation of auxiliary pipework for accessories
All auxiliary pipework for feeding the shaft seal and, where
appropriate, the double shell casing for heating and
cooling the pump, must be connected without stress or
leakage.
The pipes for the quench liquid in the case of a single-
action mechanical seal with quench (type G0Q) and the
sealing liquid in the case of a double-action mechanical
seal (type G0D) should be installed with as large a flow
cross-section as possible. The quench or sealing liquid
emerges at the uppermost connection of the mechanical
seal.
In order to ensure self-venting, the pipes must be installed
with a gradient, with low flow resistance and kept as short
as possible.
The formation of air pockets or gas bubbles must be
prevented. Venting connections must be provided if
necessary. The heating/cooling liquid outlet must be
connected at the uppermost connection of the double
shell casing, if fitted.
Commissioning/Decommissioning
Preparation for commissioning
Filling the pump with liquid
ATTENTION:
The pump must not run dry! The pump
must be filled with liquid for initial start-up and after
prolonged standstill periods.
Just a few revolutions without liquid may cause damage
to the stator. For this reason, prior to start-up, the suction
casing must be filled with water or pumping liquid, in
order to lubricate the stator and the rotor. After a
prolonged standstill, i.e. if it is to be assumed that the
liquid remaining in the pump has evaporated, or after a
repair, the filling process must be repeated.
After filling, the pump self-primes. Venting is not required,
as a liquid/gas mixture can be easily handled.
Releasing the pump
In the event of a re-start or after a prolonged standstill,
it should be ensured that the pump is rotated easily by
the drive unit. If this is not possible, e.g. because of the
high degree of adhesion between the rotor and the sta-
tor, it is possible to provide assistance using an appro-
priate tool on the hollow shaft behind the shaft seal.
ATTENTION:
The hollow shaft must not be damaged
during this process.
Control of the direction of rotation
The normal direction of rotation of the pump is anti-
clockwise, looking from the drive towards the hollow
shaft. The suction connection is located on the shaft
seal side, therefore the shaft seal is balanced. In spezial
cases, e.g. with vacuum suction or when pumping media
that will not bear gas inclusions, the pump operates in
the clockwise direction, in which case the suction and
delivery sides are exchanged.
ATTENTION
: The direction of rotation of the pump must
correspond with the rotation arrow on the pump name
plate. Incorrect direction of rotation can result in damage
to the pump. To check the direction of rotation, briefly
activate the on/off switch of the motor.
Commissioning
Start-up
Prior to start-up, all shut-off devices installed in the
suction and discharge pipes must be open.
Drive
Switch motor on.
ATTENTION
: Be aware of product-specific peculiarities
of the drive. Please refer to the manufacturer’s operating
instructions.
Checking the pump performance
When the drive reaches its operating speed, suction and
discharge pressure must be checked using a vacuum
gauge and a pressure gauge.
The motor must not be overloaded. The power
consumption can be checked by means of an ammeter.
The temperature and viscosity of the pumping liquid
must be checked against the order data sheet or
performance test report.
Protection against dry running
If there is an interruption in the flow on the suction side
of the progressive cavity pump, the thermal energy in the
pump elements caused by dry friction and flexing work is
not sufficiently transferred. This leads to the thermal
destruction of the stator elastomer within a very short
space of time. A range of dry run protection devices,
suited to the specific operating conditions, is available
for the protection of the pump elements.
Decommissioning
Shut-down
Switch the motor off.
Measures for prolonged shut-down periods
If a longer shut-down period is planned and there is a
danger of frost, the pump must be drained. In order to
do this, remove the screw plug from the suction casing.
The pump must then be preserved.
Summary of Contents for Biomaster PLUS Series
Page 15: ......
Page 16: ......
Page 17: ......
Page 19: ......
Page 21: ......
Page 22: ......
Page 23: ......
Page 24: ......
Page 25: ......
Page 26: ......
Page 27: ......
Page 28: ......
Page 29: ......
Page 30: ......
Page 31: ......
Page 32: ......
Page 33: ......
Page 34: ......
Page 35: ......
Page 36: ......
Page 37: ......
Page 38: ......
Page 39: ......
Page 40: ......
Page 41: ......
Page 42: ......
Page 43: ......
Page 44: ......
Page 45: ......
Page 46: ......
Page 47: ......
Page 48: ......
Page 49: ......
Page 83: ...Issue 16 08 2010 Instruction Manual DVZ SKA BIOMASTER PLUS Page 33 of 39...
Page 89: ...Issue 16 08 2010 Instruction Manual DVZ SKA BIOMASTER PLUS Page 39 of 39...