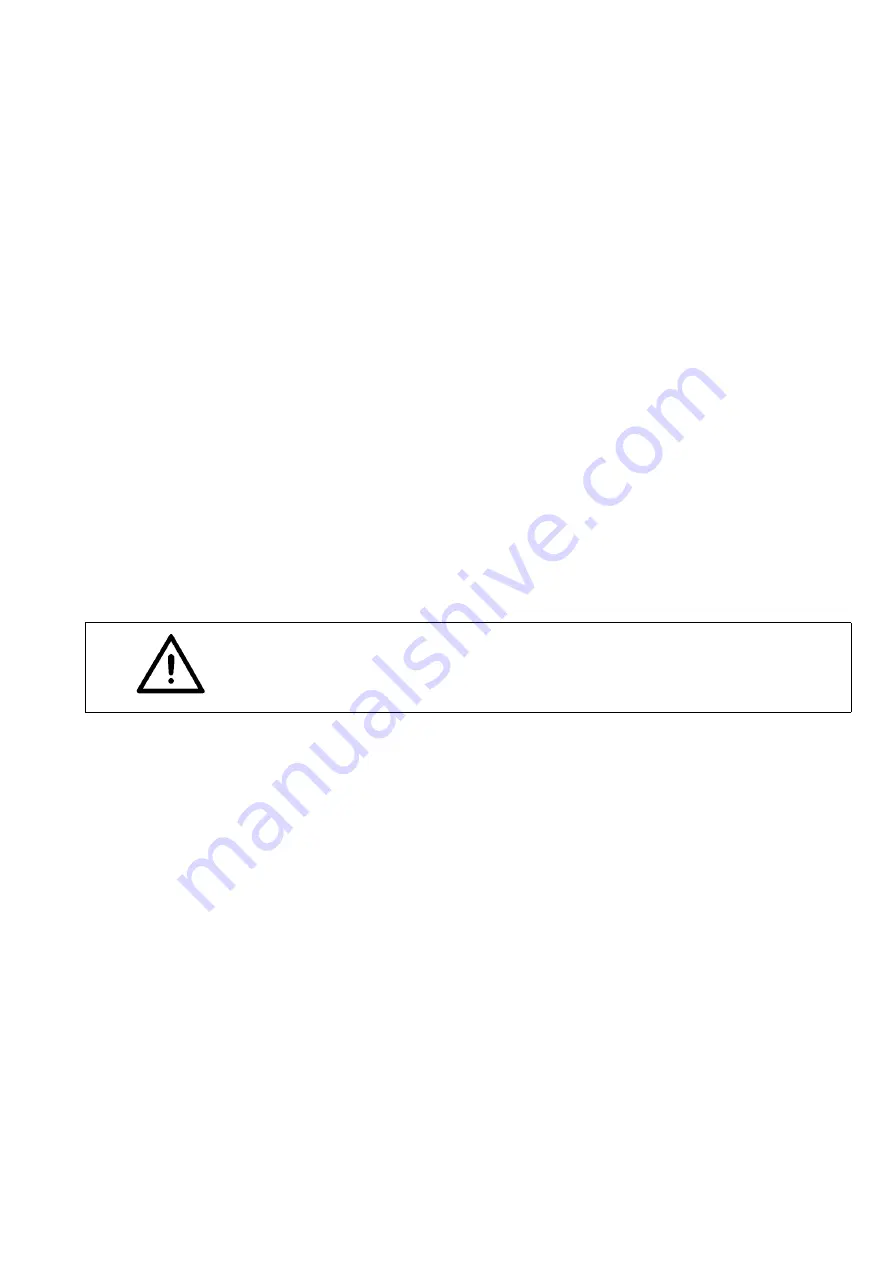
3
1
Scope of delivery
The items supplied
depend on your order
.
Before setting up the machine please check to make sure all of the required
parts are present.
This description refers to the special sewing machine whose individual
components are delivered directly and completely from
Dürkopp Adler
.
–
2
Machine head
Dürkopp Adler accessory set with:
–
1
Reel stand
–
Protective cover (not shown)
Controller parts set, complete:
–
4
Control unit
–
10
Control panel
Optional equipment
–
8
Stand with table plate
3
and drawers
9
–
7
Pedal and pedal linkage
–
6
Knee switch
–
5
Maintenance unit with connection hose
2
General information and transport packaging
If the special sewing machine you have bought is already set up, the following
transport packing must be removed:
–
Safety straps and battens on the machine head, table plate and stand.
–
Safety block and straps on the sewing drive.
CAUTION!
The special sewing machine must be set up by trained specialist
personnel.
Summary of Contents for M-TYPE 667
Page 1: ...667 Operating Instructions...
Page 4: ......
Page 10: ...6...
Page 34: ...30...
Page 36: ...Abb 1 1 2 4 6 3 5 7 8 9 10...
Page 56: ...22...
Page 57: ......