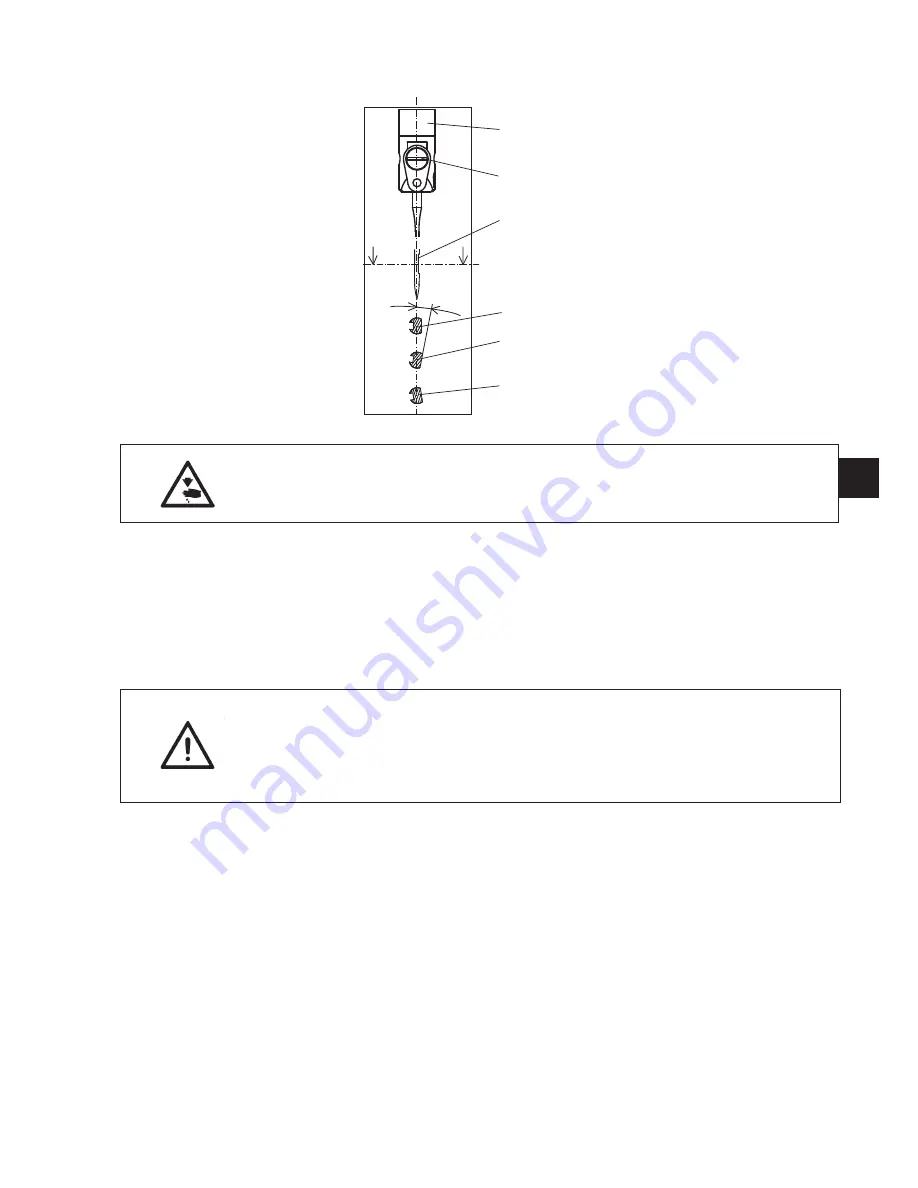
6.7
Changing the needle with single-needle machines with the hook on the right
Caution! Risk of injury!
Replace the needle with the main switch switched off and the motor
stopped.
–
Turn the hand wheel, until the needle bar (1) has reached its
highest position.
–
Loosen screw (2).
–
Remove the needle and insert a new one with the needle scarf (3)
to the right [see section (4) or (5)]. The needle may not be oriented
as shown at section (6).
–
Tighten screw (2).
Caution! Danger of breakage!
A false orientation of the needle may damage the hook point.
When changing to another needle size, the distance between hook
and needle, as well as the position of the throat plate towards its post
must be readjusted (see service instructions).
15
GB
1
2
3
4
5
6
MAX. 3°
Summary of Contents for LP 2971
Page 6: ...Notes ...
Page 32: ...Notes ...