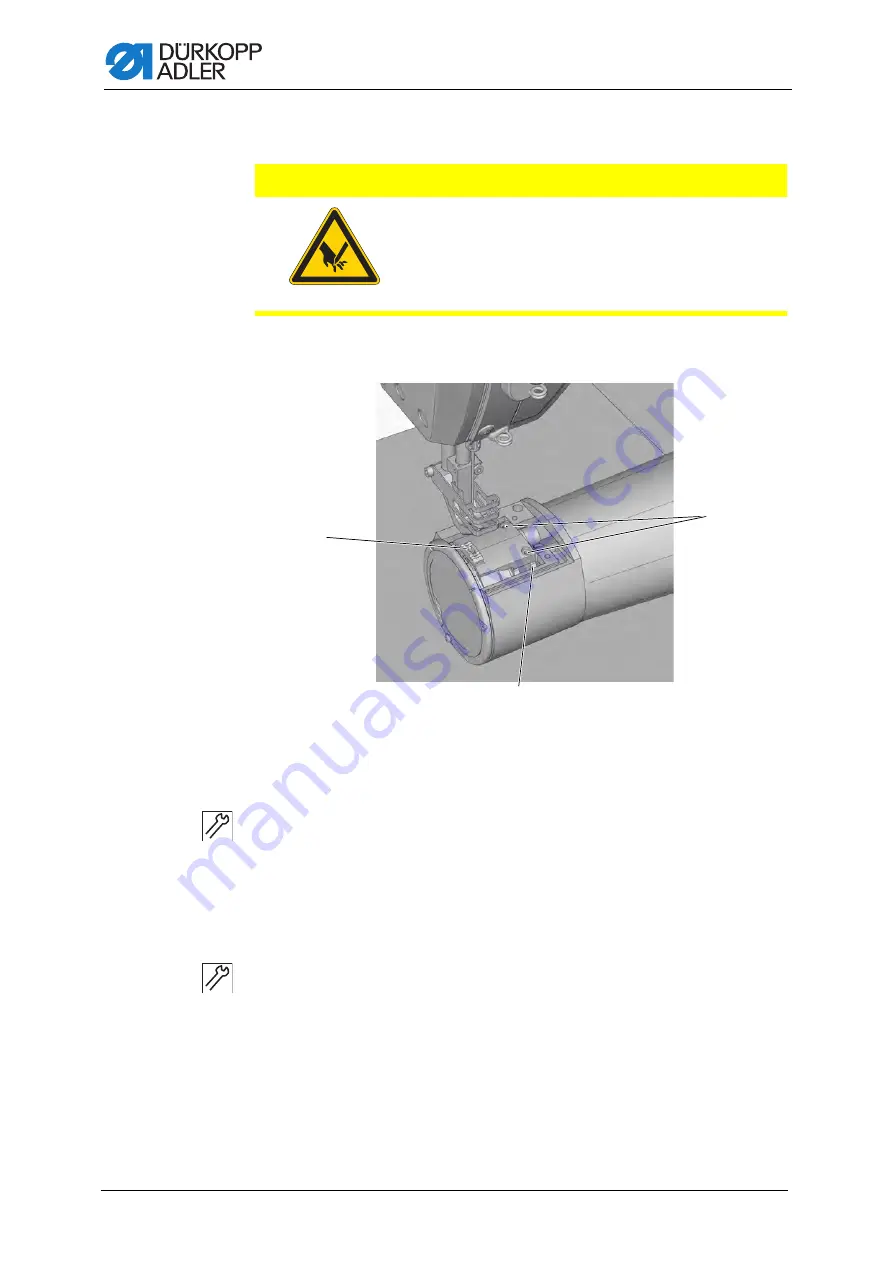
Working basis
20
Service Instructions 969 - 06.0 - 03/2019
3.3.8 Disassembling and assembling the feed dog
Fig. 8: Disassembling and assembling the feed dog
Disassembling the feed dog
To disassemble the feed dog:
1. Disassemble the throat plate (
2. Loosen the screws (3).
3. Remove the feed dog (1) from the feed dog carrier (2).
Assembling the feed dog
To assemble the feed dog:
1. Insert the feed dog (1)
2. Slightly tighten the screws (3).
3. Assemble the throat plate.
4. Set the feed dog (1) so that it has an equal amount of play on both
sides when inside the throat plate.
5. Tighten the screws (3).
CAUTION
Risk of injury from sharp and moving parts!
Puncture or crushing possible.
Switch off the machine before disassembling
the feed dog.
(1)
- Feed dog
(2)
- Feed dog carrier
(3)
- Screws
③
①
②
Summary of Contents for 969 Classic
Page 1: ...969 Service Instructions...
Page 6: ...Table of Contents 4 Service Instructions 969 06 0 03 2019...
Page 10: ...About these instructions 8 Service Instructions 969 06 0 03 2019...
Page 92: ...Programming 90 Service Instructions 969 06 0 03 2019...
Page 106: ...Decommissioning 104 Service Instructions 969 06 0 03 2019...
Page 108: ...Disposal 106 Service Instructions 969 06 0 03 2019...
Page 119: ...Appendix Service Instructions 969 06 0 03 2019 117 21 Appendix Fig 76 Wiring diagram...
Page 120: ...Appendix 118 Service Instructions 969 06 0 03 2019...
Page 121: ......