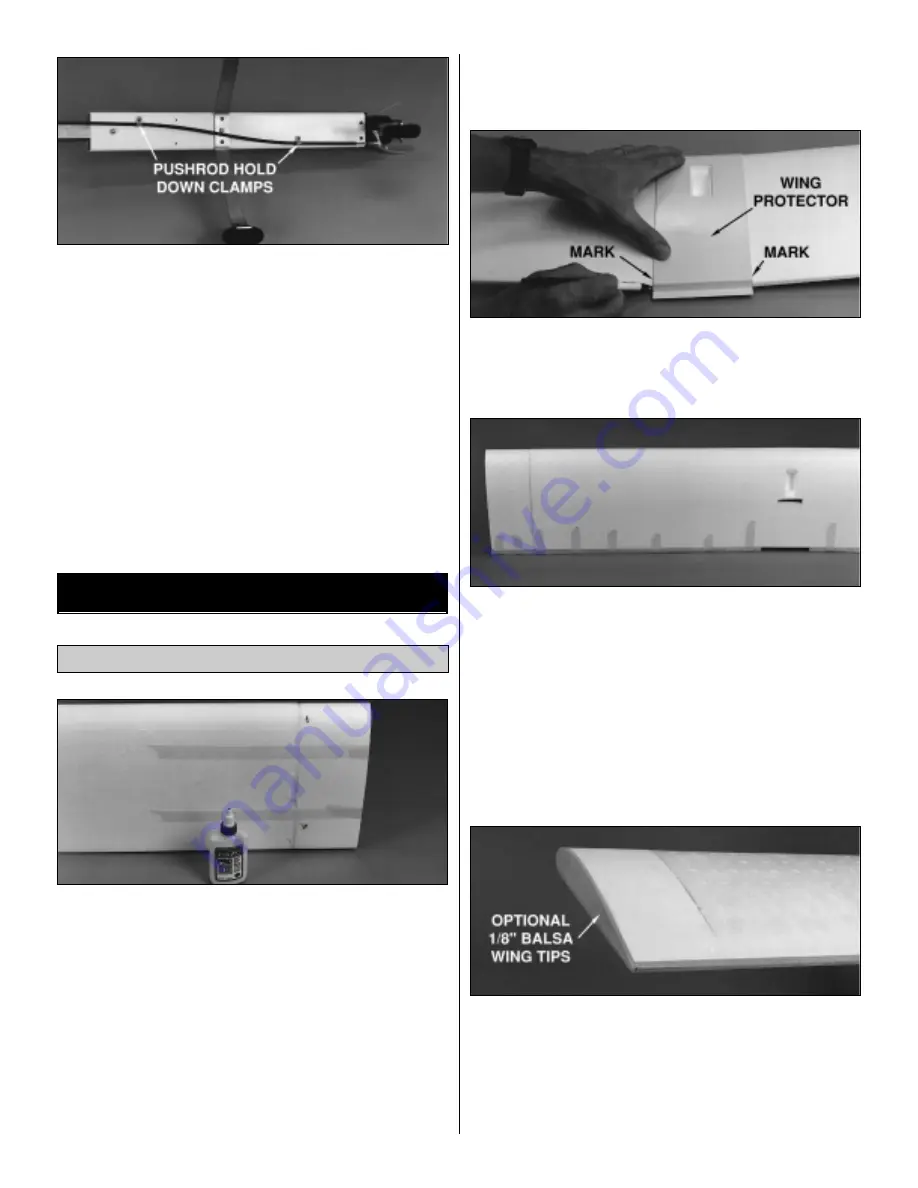
❏
3. Cut the inner pushrod tube to the correct length, then
install the last 1" threaded stud with a clevis. Position the
steering arm as shown in the photo. Adjust the length of
the pushrod so that when the rudder is neutral and the
pushrod is connected to the steering arm, the nose wheel
is also neutral.
❏
4. Turn the model over and confirm the coordination of
the rudder and the nose wheel – when the rudder moves
left, the nose wheel should turn left.
❏
1. Apply a thin film of aliphatic resin (white glue such as
Great Planes Pro) or epoxy to one of the wing tips and the
root of one of the wing extensions then join the two pieces
by clamping them together with T-pins and masking tape.
Hint: Stick the T-pins in first as they will keep the root
extension from shifting while you apply the masking tape.
Place a straightedge on the bottom of the wing across the
wing and the wing extension to make sure you have not
inadvertently built in some dihedral or anhedral to the tip of
the wing.
❏
2. Glue the other wing extension the other wing tip in the
same manner. Allow the glue to fully dry before proceeding.
❏
3. Use a hobby knife or a MultiPro to cut the hole in the
plastic wing shield for the aileron servo. True the sides of the
wing shield with a bar sander and 220-grit sandpaper.
❏
4. Place the wing shield on the wing and aligning the
hole in the shield with the hole in the wing for the aileron
servo. Use a felt-tip pen to mark the edges of the wing
shield onto the trailing edge of the wing.
❏
5. Cut the 1/4" x 5/16" x 24" balsa wing trailing edges so
they fit between the marks you made and the tip of the
wing. Use epoxy or aliphatic resin to glue the trailing edges
to the wing and hold them in position with masking tape
until the glue dries.
Note:
The 1/4" side of the trailing edges is the side that
gets glued to the wing.
❏
6. Use a sanding block to sand the ends of the balsa
trailing edges so they are flush with the wing tips.
❏
7. Optional: Trace the outline of both wing tips onto a
1/8" balsa sheet (not included), then cut the wing tips from
the sheet and glue them to the tips of the wing. After the
glue dries use a sanding block and 220-grit sandpaper to
shape the balsa tips to match the contour of the wing. The
1/8" balsa will add a little durability by protecting the wing
tips from dents and dings.
Assemble the Ailerons
Build The Wing
9