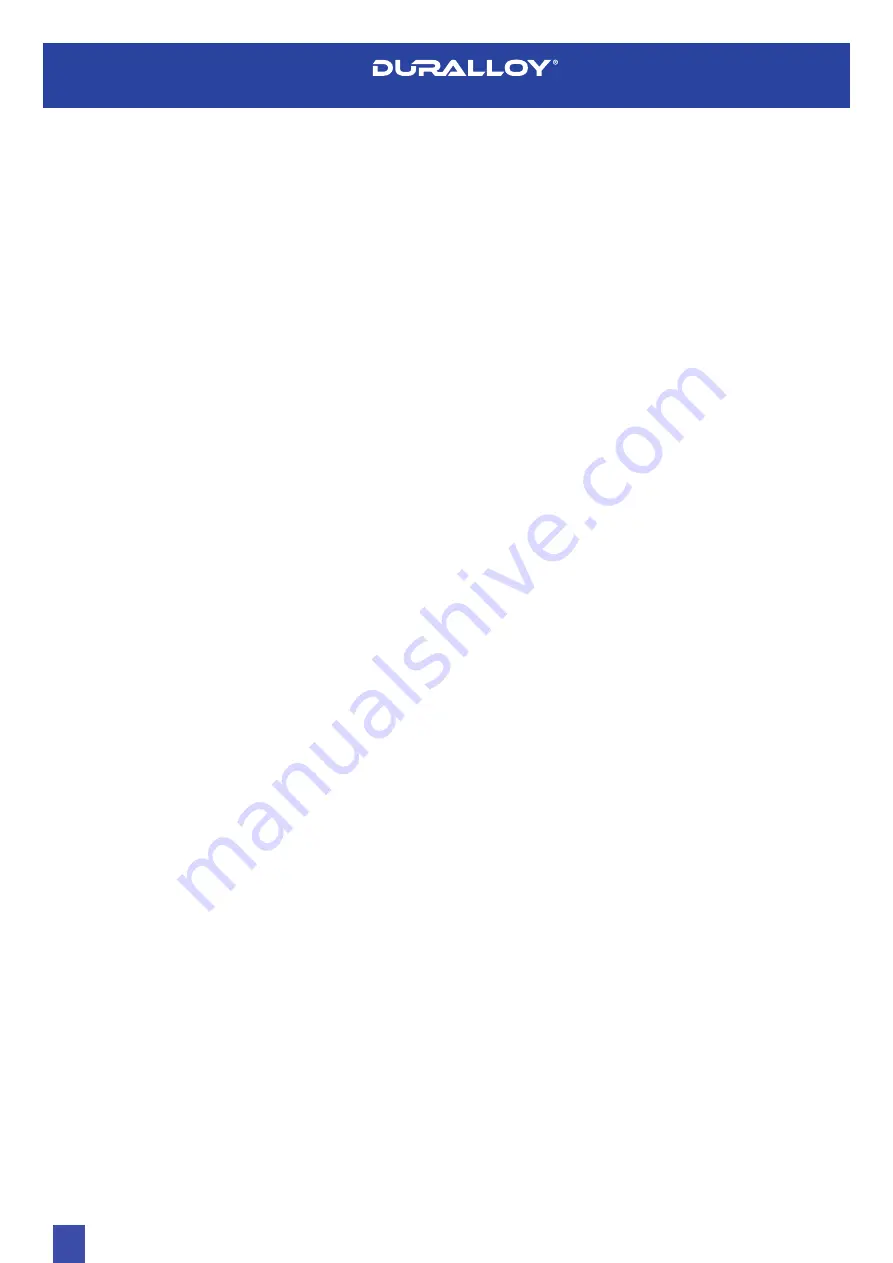
TIPS & TRICKS
Duty Cycle Rating
welding arc that sets the heat. The wire speed feed simply
controls the rate at which the welding wire is fed into the weld
pool. For any voltage position setting, there will be a specific
corresponding ‘sweet spot’ in the wire feeding speed that will
give the smoothest and most stable welding arc. The correct wire
feeding speed for a given voltage setting is affected by welding
wire type and size, shielding gas, welding material and joint type.
It is recommended to set the welding voltage as desired and
then slowly adjust the wire speed until the arc is smooth and
stable. When reaching this point, if the penetration/ heat input
is too much/ not enough, adjust the voltage setting and repeat
the process.If the operator is not able to achieve a smooth and
stable arc with the desired heat input for the weld, it is likely
that a change in wire size and/or shielding gas type is required
(assuming all other factors are correct).
Wave Control
This setting changes the MIG waveform to simulate changing
the inductance of the welding circuit. Inductance controls the
rate of the current rise and fall as the welding wire contacts the
workpiece (known as a short circuit). More inductance increases
the short circuit time and decreases the short circuit frequency
rate. This causes a wider and more penetrating arc, useful for
thicker weld joints. Less inductance will create a narrow more
focused arc. This effect can also be used to fine tune the arc to
produce less splatter. Wire speed, wire size and type, shielding
gas will all change the effect that the inductance setting has
on the welding arc. Inductance change will have no practical
effect on MIG spray transfer process (as opposed to short circuit
process), MMA or TIG welding process.
Arc Force Control
An MMA welding power source is designed to produce constant
output current (CC). This means with different types of electrode
and arc length; the welding voltage varies to keep the current
constant. This can cause instability in some welding conditions as
MMA welding electrodes will have a minimum voltage they can
operate with and still have a stable arc. Arc Force control boosts
the welding power if its senses the welding voltage is getting too
low. The higher the arc force adjustment, the higher the minimum
voltage that the power source will allow. This effect will also
cause the welding current to increase. 0 is Arc Force off, 10 is
maximum Arc Force. This is practically useful for electrode types
that have a higher operating voltage requirement or joint types
that require a short arc length such as out of position welds.
www.duralloy.net.au
|
1300 369 456
6
MULTIMIG 200 PFC MV
OWNER’S MANUAL