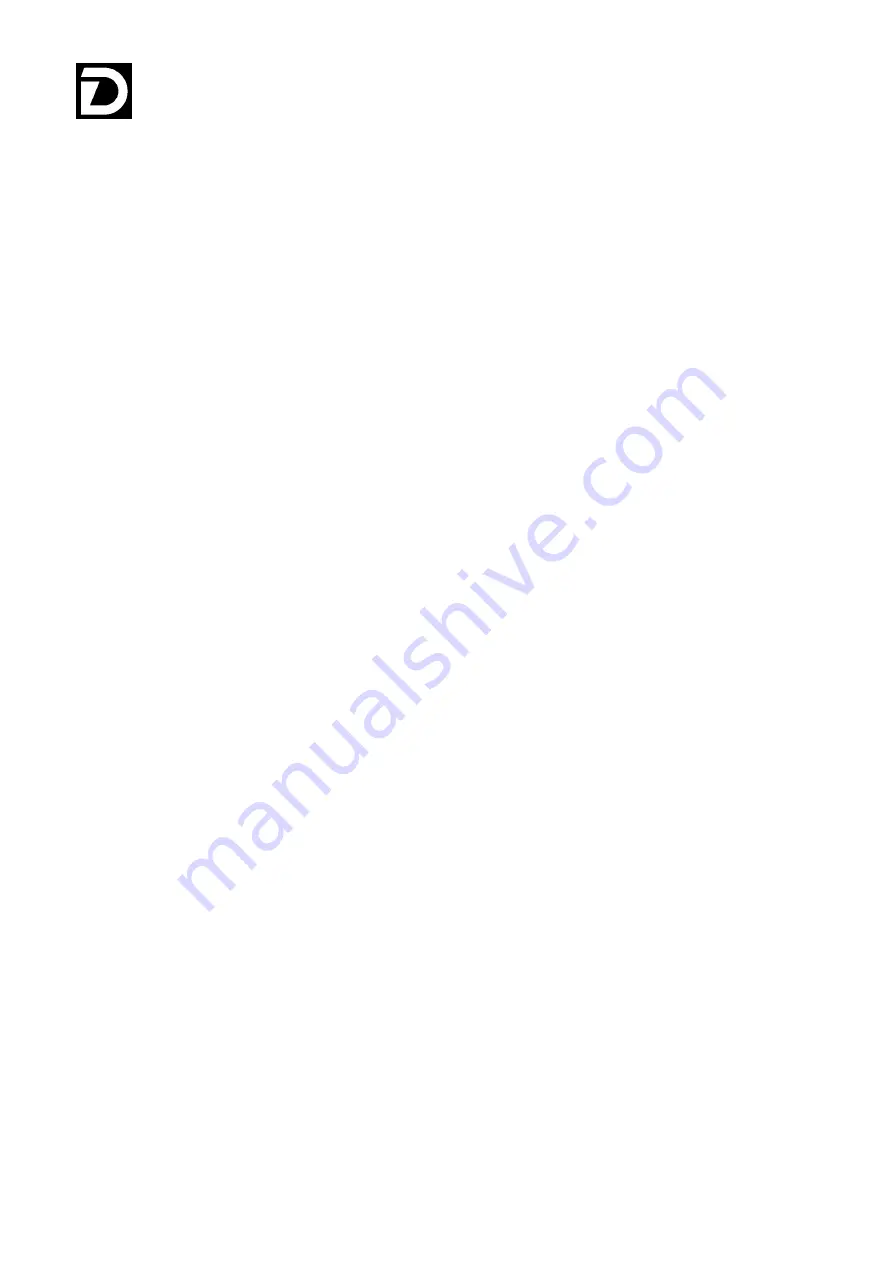
UEIK-11RS*
SERIES 52
Enables voltage reading of the valve spool position (0 / -5V).
4.3 - TRANSDUCER (Transducer signal measurement point)
89 315/107 ED
3/4
Enables reading of reference signal sent to the card.
Reading is direct, but of opposite sign, with voltage reference while
current conversion is: 4 mA = 0V 20 mA = -10V.
4 - SIGNAL MEASUREMENT
4.1 - CURRENT (Solenoid current measurement point)
Enables voltage reading of current supplied to the solenoid.
Reading conversion: 1V DC = 1A.
4.2 - REFERENCE (Reference signal measurement point)
The electronic control unit is supplied factory-set. Standard settings are:
– “GAIN” regulation: +10V (or 20 mA) reference signal
corresponding to maximum valve opening (transducer = -5V).
In open loop “GAIN” regulation corresponds to a current supply of
1 A for RSQ version and 1,8 A for RSD version, to the solenoid
with maximum reference signal.
– “OFFSET” regulation: zero
– “RAMP UP” and “RAMP DOWN” regulation: minimum
– position SW1 on V
– position SW2 on S
– position SW3 on AC
– position S1 on N
– switching frequency (PWM) = 230 Hz
7 - START-UP AND CONTROL SETTINGS
If required, settings can be adjusted as follows:
a) OFFSET CURRENT REGULATION
– Set “GAIN” potentiometer to minimum.
– Enter reference signal at maximum value (+10V or 20 mA).
– Set the “OFFSET” potentiometer so that the valve is
positioned at the start of the work zone.
6 - DEFAULT CONDITIONS
5 - INSTALLATION
The card is designed for assembly on a rack or a card holder with
interface for connector types DIN 41612 - size D - 32 pole.
It is recommended to use cable sections of 1 to 2,5 mm
2,
depending
on their length, for power supply and solenoid connections. For
other connections it is recommended to use cables with a screened
sheath connected to earth only on the card side.
NOTE 1:
To observe EMC requirements it is important that the control
unit electrical connection is in strict compliance with the wiring diagram of
par. 9.
As a general rule, the valve and the electronic unit connection wires
must be kept as far as possible from interference sources (e.g.
power wires, electric motors, inverters and electrical switches).
In environments that are critical from the electromagnetic interference
point of view, a complete protection of the connection wires can be
requested.
The overall and mounting dimension diagram in par. 10 shows four
switch banks: SW 1 - SW 2 - SW 3 and S1 which enable the card
to be set up as required.
NB. Each modification to switch settings must be carried out
with the card disconnected from the power supply. The
individual switches inside each bank must all be set in the
same position.
SELECTION OF VOLTAGE OR CURRENT REFERENCE SIGNAL
(SW 1 bank comprising three individual switches)
– select V for voltage signal
– select I for current signaI.
SELECTION OF SINGLE ENDED OR DIFFERENTIAL REFERENCE
SIGNAL
(SW 2 bank comprising one individual switch)
– select S for single ended reference signal. This condition is
obligatory in the case where the reference signal is generated
with an external potentiometer fed by the card itself.
– select D for differential reference signal. This condition is
preferable in the case where the reference signal comes from a
PLC or CNC analogic outlet.
OPEN OR CLOSED LOOP SELECTION
(SW 3 bank comprising two individual switches)
– select AC for closed loop
– select AA for open loop.
TRANSDUCER POLARITY SELECTION
(SW 1 bank comprising one individual switch)
– select N for direct operated valve types DSE3F - RPCER1/52
– select D for piloted valves.
NB. In the event of transducer malfunction, AA can be selected
to proceed with open loop operation. In this case, the ENABLE
LED illuminates and the OK relay card contacts close and the
FAULT LED remains lit to indicate alarm status.
SWITCHING FREQUENCY ADJUSTMENT
It is possible to change the switching frequency (PWM) by acting on
the trimmer PT7 (see par. 10).
The setting range is from 80 to 1600 Hz.
An appropriate switching frequency adjustment allows reduction of
the valve hysterisis value.
Clockwise rotation to increase the frequency.
8 - CARD CIRCUIT SETTINGS
b) SCALE FACTOR REGULATION
– Enter the reference signal at maximum value (+10V or 20 mA).
– Set “GAIN” potentiometer so that the controlled hydraulic
parameter reaches the maximum required value.
c) RAMP REGULATION
– Regulate the “RAMP UP” and “RAMP DOWN” potentiometers
to obtain the gradual valve operation required with a reference
signal variation.
3.6 - RAMP UP / RAMP DOWN (Ramp regulation)
“RAMP UP” and “RAMP DOWN” potentiometers, in a range from 0,03
to 7 sec., regulates the time required to achieve the supplied current
according to a step change of the reference signal up or down.
It is possible, in this way, to control the valve response time, adjusting
it to the requirements of the hydraulic circuit and the machine cycle.
Ramps can be inhibited by transmitting a 22 to 30 V DC exclusion
command to pin 16a. In this case, the ramp residual time is 10 ms.
Rotate clockwise to increase ramp time.