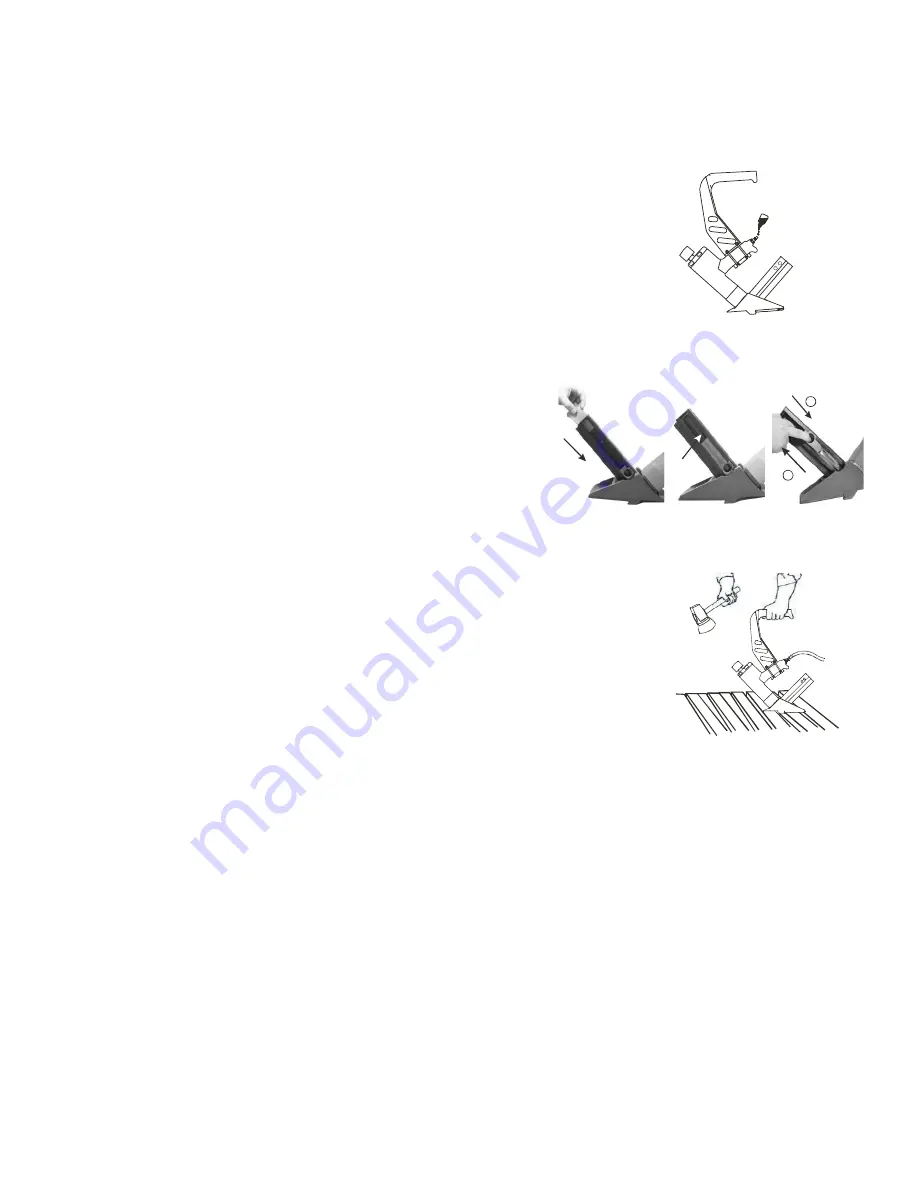
5
UNPACKING
When unpacking, check and make sure that all accessories are included. If anyone is
missing or broken, please contact your distributor. Refer to the following lists, 1 each:
Hammer
Nailer
CONNECTING THE TOOL WITH THE AIR SUPPLY
1. Determine if it is necessary to lubricate. If necessary, put 2 drops of oil
into the AIR PLUG-Key 46 (Figure 1).
If you are using an automatic in-line oiler, check and add oil if necessary.
2. Turn the air compressor on and adjust the regulator to a proper pressure
for shooting suitable fastener.
3. Connect the tool to the air supply.
LOADING THE FASTENERS
1. Load one (1) strip or up to 100 fasteners into the “T” slot in the rear
of the magazine (Figure 2A).
2. Slide the fasteners all the way forward (Figure 2B).
3. Pull the feeder shoe back behind the fasteners and allow it to slide
forward pushing the fasteners to the front of the magazine (Figure 2C).
OPERATING THE TOOL
Test the driving depth in a sample piece of wood before using.
If the fasteners are being driven too far or not far enough, adjust the regulator to provide
less air pressure or more air pressure.
1. Connect the tool to the air supply. Make sure the air pressure is in correct range
denoted in the section of Specifications.
2. Load fasteners as above the direction given in the section called Loading the Fasteners.
3. Hold the long arm and press the shoe to work surface and make
sure the fastener connection position. Strike the hammer face with a hammer to
drive the fastener out (Figure 3).
4. Lift the tool off the work piece.
REGULAR MAINTENANCE
1. Frequent but not excessive, lubrication is required for the best performance. Oil added
through the air inlet will lubricate internal parts. An automatic air line oiler is recommended
but oil may be added manually before every operation or after about 1 hour of continuous
use. Only a few drops of oil at a time is necessary. Too much oil will collect inside the tool
and be blown out during the exhaust cycle.
ONLY USE PNEUMATIC TOOL OIL. Do not use detergent oil or additives because these
lubricants will cause accelerated wear to the seal in the tool.
2. Use a small amount of oil on all moving surfaces and pivots.
3. Dirt and water in the air supply are major causes of pneumatic tool wear. Use a filter/oiler
for better performance and longer life. The filter must have adequate flow capacity for the
specific application. Consult the manufacturer’s instructions for the proper maintenance of
your filter.
4. Keep tools clean for better and safer performance. Use nonflammable cleaning solutions.
(Caution such solutions may damage O-ring and other tool parts ) only if necessary.
DO NOT SOAK.
S3 Hex key
S4 Hex key
S5 Hex key
Air tool oil
Operating instructions
Figure 1
Figure 3
2
1
Figure 2
2A
2B
2C