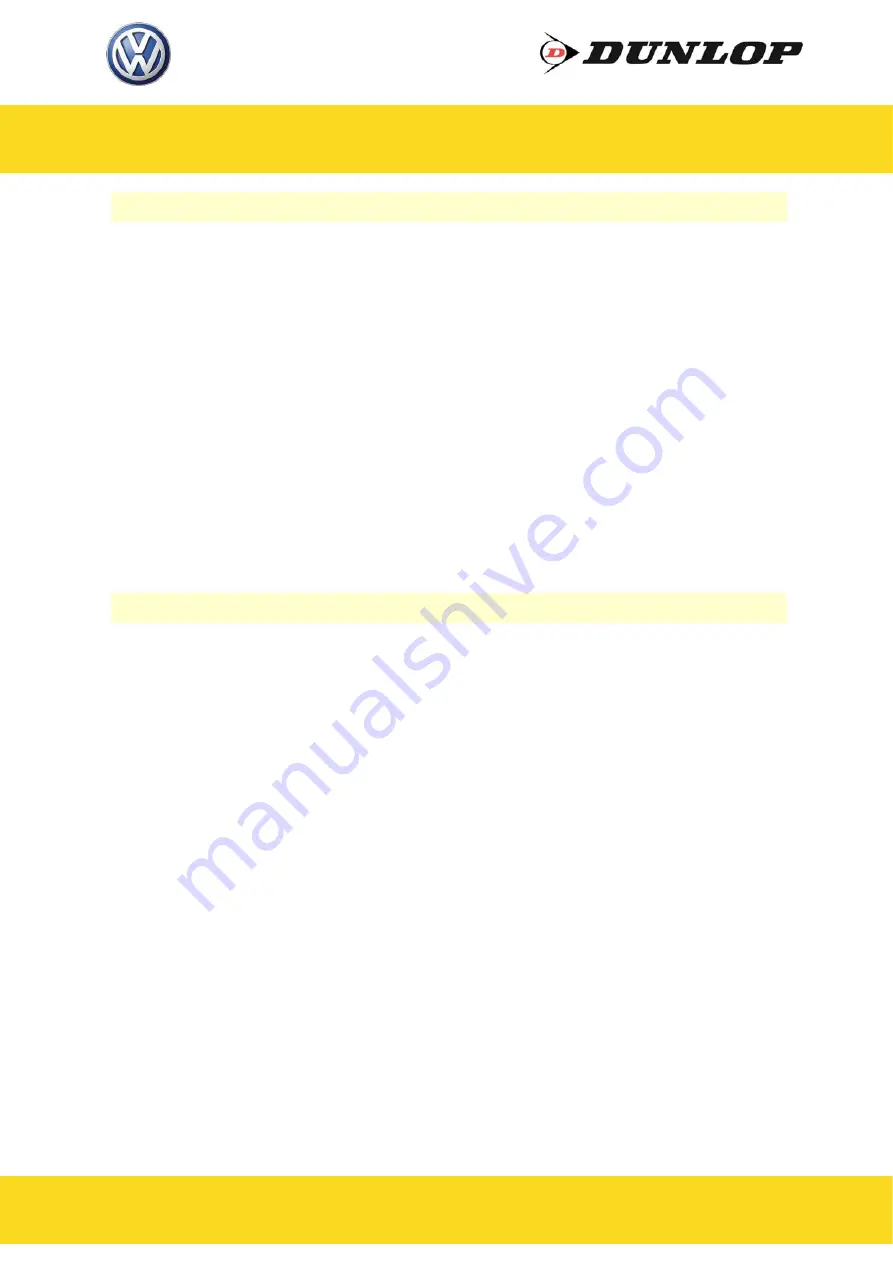
L.AMA.10.C.L
Volkswagen AMAROK
8
DUNLOP and the Flying D Device are trademarks of Dunlop International Group and are used under license by DSC Nederland B.V.
www.dunlopsystems.nl
5.2 Bump Stop Removal and fitting of Upper Bracket
i.
Remove the two bump stops - Figures 1, 2.
ii. Insert the Hexagon screw M6 x 25 till the tip is 1 mm on the topside
of the upper bracket - Figure 3.
iii. Shift the upper bracket in the slot of the bump stop and fully tighten
the M6 bolt in the middle, it’s to align the upper bracket in the
middle of the bump stop frame - Figure 4.
iv. Insert the M12 x 100 bolt with the big washer and the busing from
the outside towards the inside, it’s to secure the upper bracket.
Take care the busing won’t fall into the chassis beam - Figure 5.
v. Put the washer and the self locking nut M12 on the tip of the M12
bolt. Push the upper bracket upwards and tighten the screws. The
bushing is a bit shorter than the chassis, so the upper bracket will
remain tight on it’s position - Figures 6.
5.3 Attachment of Lower Bracket and Bellow to Axle
i. Insert the hose from the under side of the bracket through the
lower bracket (See Section 5.6 - “Tube Connection and
Disconnection, Cutting and Routing”) : Connect the hose to the
bellow by pushing the hose onto the air inlet port and tighten the
nut. Use black tubing for the left-hand bellow and blue for the right
-hand bellow - Figure 7.
iii. Manually compress the air bellow as flat as possible. Then bend the
end of the air hose and put a ty-wrap around it to maintain the
compressed state. Because we use ‘soft’ hose this is not a problem
to do - Figure 8.
iv. Secure the lower bracket to the air bellow by insert the hexagon
bolts M6x 20 with washer. Take care the bolts are only finger tight -
Figure 8.
v. Remove only the nut (Spanner 18 mm) of the bottom side of the
shock absorber and put a washer M12 on it - Figure 9, 10.
vi. Install the lower bracket (with air bellow) on the rear axle. The air
hose has to be at the front side of the axle. Push the lower bracket
to the rear till the metal strip of it touches the rear axle and secure
the original nut - Figure 11, 12.