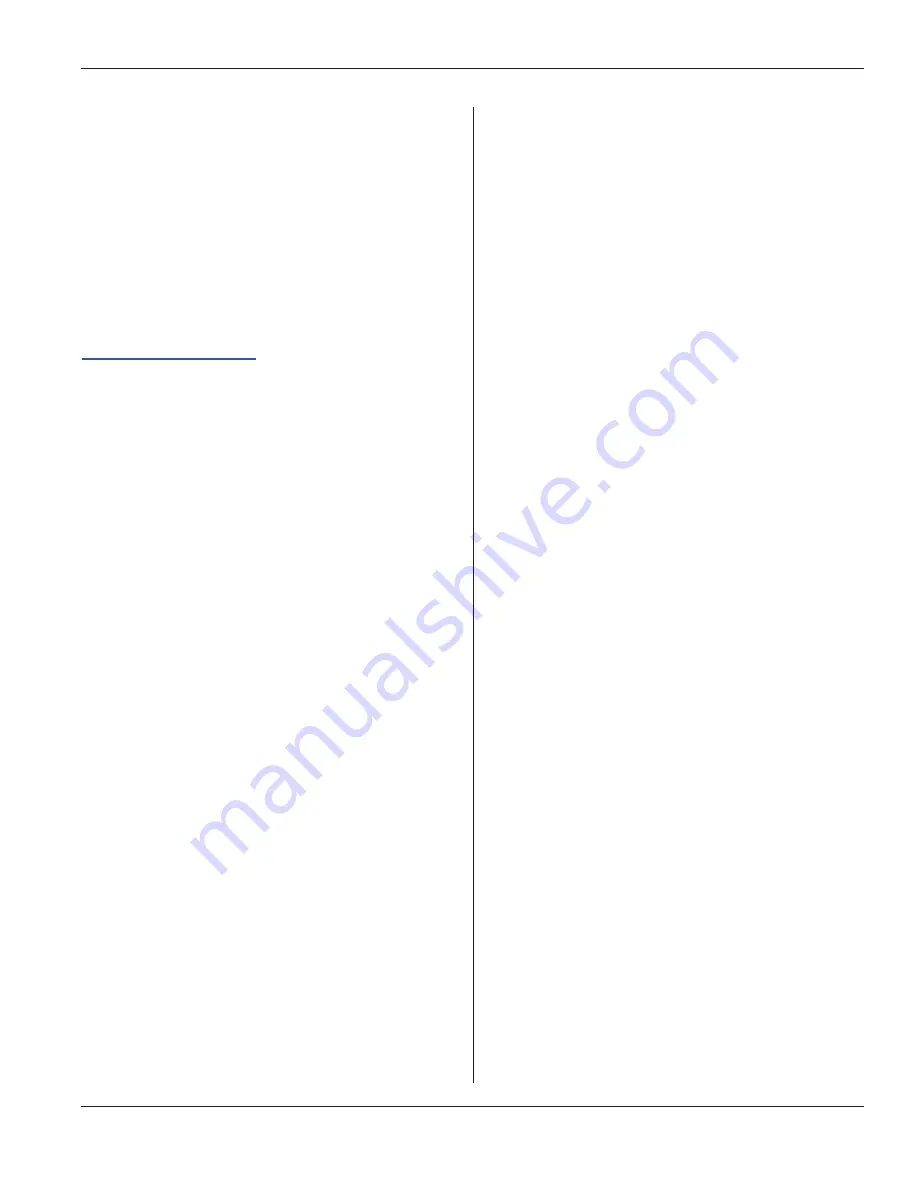
Section 6 – Automation Interface
Page 45
Dukane Manual Part No. 403-591-01
iQ Commander
TM
Using Dukane’s PC interface tool,
the Windows PC
based software, connected via a standard USB cable
(Dukane part number 200-1906), can be used to configure
and monitor the iQ Auto-Plus generators. This tool allows
the user to easily perform field firmware updates, product
setup, parameter configuration, system diagnostics, and
setting a IP address for a communications protocol.
Below is a link to download the software:
To install
iQ Commander
TM
1.
Download the installation file from (http://update.
dukane.com/) and save to the desired location on the
PC.
2.
Double-click on the installation file.
3. Once prompted, click on “Next >” on the “Welcome to
the InstallShield Wizard for iQ Commander” page. The
executable will start the installation process.
4. When the progress bar is nearly full, a new window
will appear asking to install the FTDI CDM Drivers.
This window may appear behind the iQ Commander
TM
installation window. If the FTDI CDM Driver window
is not visible, move the iQ Commander
TM
installation
window to the side to see the FTDI CDM Drivers
installation window.
5. On the FTDI CDM Drivers installation window,
click on “Extract”, “Next >”, accept the agreement,
“Next >”, and then “Finish” to install the first set of
FTDI drivers.
6. Another window will pop up asking to install another
set of FTDI CDM Drivers. Repeat step 5 to install the
second set of drivers.
7. Once the drivers are installed, Click on “Finish” to
complete the process. The user can connect a USB
cable from the PC to the AiM generator and start the
program.
Operations that can be done via
iQ Commander
TM
1. Update the
iQ Auto Plus
generator firmware.
2. Test the ultrasonic stack.
3. Scan an ultrasonic stack to determine the optimal Free
Run Frequency.
4. Weld a part.
5. Select a probe when an MPC module is connected.
6. Set weld method to Time, Energy, Peak Power, Distance,
or Position and the associated value in seconds, joules,
watts, or millimeters.
7.
Configure custom I/O.
8. Set Amplitude, Ramp Up Time, and Ramp Down Time.
9. Enable and set Trigger by Power parameters.
10. Enable and set Hold Time.
11.
Enable and set Afterburst delay and duration.
12.
Enable checking for Suspect Parts. Set maximum
and minimum values for Time, Power, Energy,
Distance, and/or Position.
13.
Enable checking for Bad Parts. Set maximum
and minimum values for Time, Power, Energy,
Distance, and/or Position.
14.
Configure advanced hardware settings including,
Free Run Frequency, Frequency Tracking,
Frequency Lock and Hold, and Frequency Limits.
Parameters that can be obtained via
iQ Commander
TM
.
1.
All parameters that are configured via
iQ Commander
TM .
2.
Real time data which includes welder state
(ultrasound active or not), frequency, power,
position, and amplitude.
3.
Weld cycle data from previous weld which
includes: Cycle Count; Good, Bad, and Suspect
Part information; Process Limit setting exceeded
or not reached if Bad or Suspect Part checking is
enabled; Weld Time; Weld Energy; Peak Power;
Weld Distance; Weld Position.