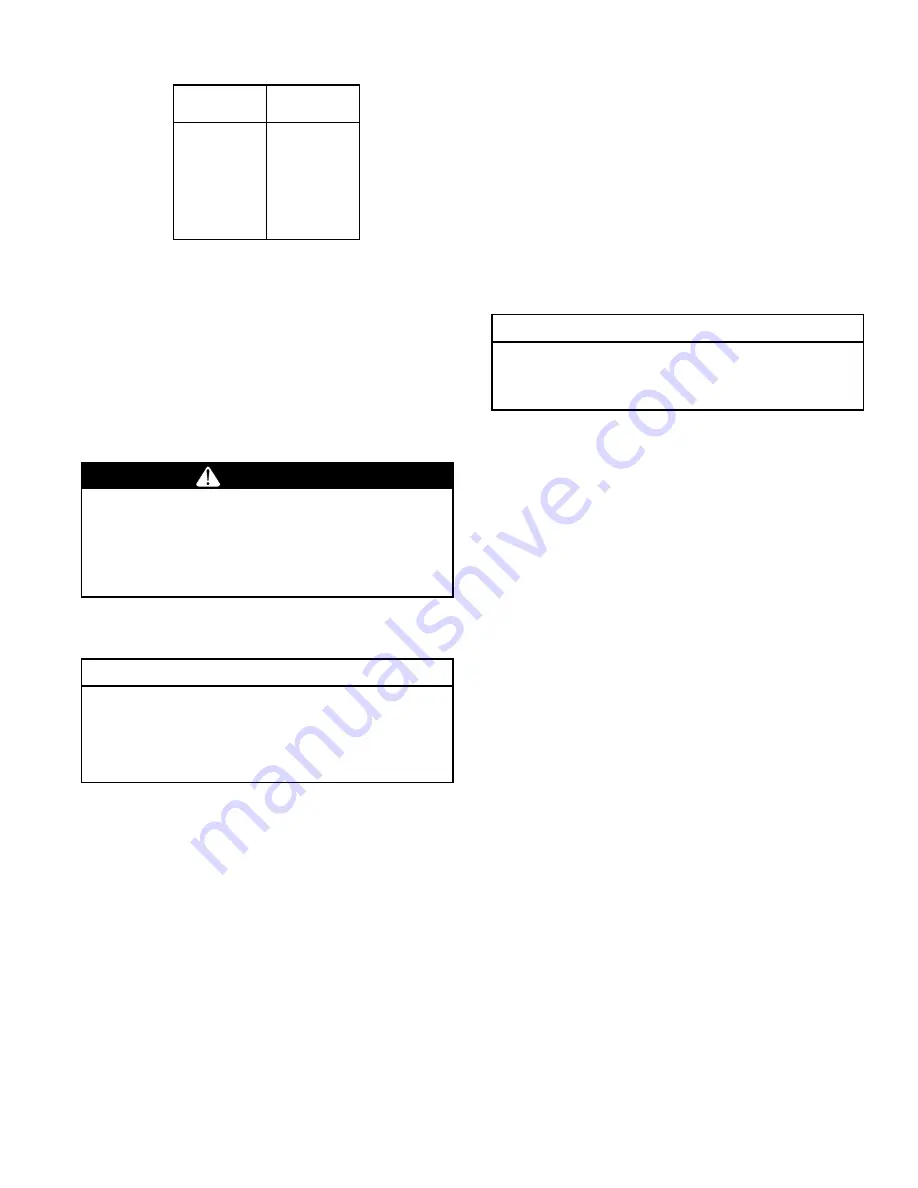
7
4.
Hold arbor tight against and symmetric with the end
of the screw (a pilot to engage in the screw hole is
helpful). Turn the nut down the screw and continue
running it over the arbor until it is completely off the
screw.
5.
Use wire, tape, cable ties, or similar to prevent the
arbor from falling through the nut.
4-6. Cleaning
Clean all parts and inspect for wear or damage.
3.
Place screw bushing (if used) and shell cap on
screw. Place load bearings on worm gear and in-
stall on screw. If working load is primarily in one
direction, the bearing locations can be swapped
from original, to increase service life.
4.
Securely tighten worm gear nut and install locking
device, if used.
5.
Fill translating tube about half full of grease (see
Section 3-1). Screw translating tube onto lifting nut.
If new nut is being used, spot drill the nut threads
for the setscrews.
Setscrews must not protrude above the surface of
the tube, to avoid interference with nylon nut guide.
Table 2
1.
Use degreasing solvent to remove grease or oil from
all parts.
2.
Use clean hot water or a soap solution for general
cleaning of painted surfaces.
3.
Dry parts thoroughly after cleaning.
4-7. Inspection (Refer to Figure 5-1)
Inspect bearings for damaged race surfaces. Inspect seals
for cut or brittle lips.
Replace any defective parts, using only Duff-Norton sup-
plied or approved parts
4-8. Assembly (Refer to Figure 5-1)
1.
Install lifting nut on screw. Hold ball nut arbor against
screw and twist on nut, being careful not to lose
balls.
2.
Install stop washer and bolt. Use high strength
thread locking adhesive on bolt.
6.
Insert worm with bearings into the shell. Be sure it
is pointing the right way to fit the drive and limit
switch. Do not install flanges yet.
7.
Insert screw with gear and bearings into shell.
Tighten shell cap to previous location, evident from
setscrew indentations, or until bearings are com-
pletely seated. Bearings should be preloaded to
provide slight drag. If parts replacement has re-
sulted in the setscrews not engaging with original
indentations, lightly spot drill actuator shell at new
setscrew locations.
8.
Center worm in housing and install bearing flanges
(with seals), with original shims. Tighten flange
screws. Tap each end of worm to seat bearings
and recheck flange screws for tightness. Worm
should turn without binding, and also without no-
ticeable end play. Add or remove shims to achieve
this situation.
9.
Pump grease into housing (see Section 3-1) until
grease oozes between screw and shell cap.
10. Be sure nylon nut guide is in place.
11. Be sure guide bushing and wiper seal are in outer
tube. Slide outer tube over translating tube and
screw all the way onto shell cap. Tube may be
backed off up to one turn to align grease fitting.
Tighten outer tube setscrews.
12. Put a few pumps of grease into the guide bushing
grease fitting. If the screw has been well greased,
only a small amount is needed in the bushing area
at this time.
13. Reinstall reducer and motor, checking for any wear
or damage in those components. Replace motor
bearings if noisy. Reinstall limit switch. Limit switch
will require readjustment (see Section 2-6) after in-
stallation of SuperCylinder.
14. Check reducer oil level after installation.
Screw O.D.
Arbor Dia.
1.0"
.88"
1.17"
.88"
1.5"
1.156"
2.25"
1.88"
2.5"
2.24"
3.0"
2.50"
WARNING
Provide adequate ventilation during
the use of cleaning agents; avoid
prolonged breathing of fumes and
contact with skin. Read & follow
manufacturer's instructions.
Note
Remove grease from unit and do not
reuse old grease.
Before installing new parts, remove any
rust preventive, protection grease, etc.
Note
It is critical that these setscrews be
spot-drilled, tightened, and secured
with thread locking adhesive.