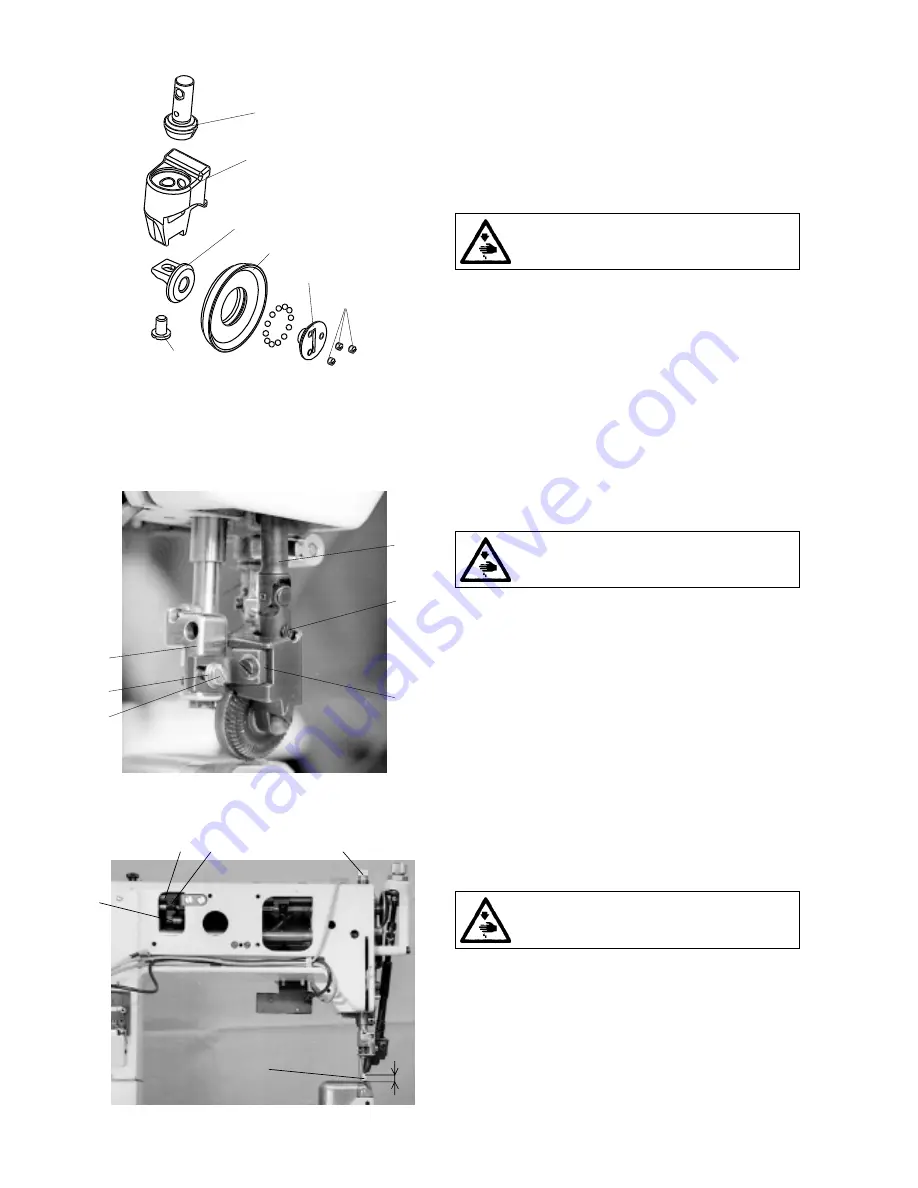
20
3.7.8.3 Setting the gear clearance
and in the mounting of the top roller
In the cone gear of the drive of the top roller, the minimum
clearance must be set. A too small clearance will increase the
friction resistance of the gear, the excessive clearance will
influence the inaccuracy of feeding. The top roller itself is
mounted on balls. With this type of mounting,it is also
necessary to set the minimal possible radial clearance.
The given clearances are set as follows:
Caution! Danger of injury!
Switch off the main switch! Before starting the setting
operation, wait until the motor stops!
Clearance in the wheel mounting
- Loosen three screws (5) /only slightly/.
- Using the screw (4) set the minimum clearance in the top
roller mounting (2) /it must easily rotate without any rubbing
and with a minimum clearance/.
- Tighten the screws (5), check the set up clearance, even-
tually, repeat the setting procedure.
Clearance in the conic gear
- Loosen the screw (1), in shifting the wheel, resp. the holder
(3) in the holder groove (6), set the minimum clearance,
the pinion (7) must be pushed up to the holder bottom (6).
- Tighten the screw (1), check the set up clearance.
3.7.8.4 Replacement of the top roller
When replacing the top roller, proceed as follows:
Caution! Danger of injury!
Switch off the main switch! Before starting the setting
operation, wait until the motor stops!
- Unscrew the screw (1).
- Unscrew the screw (3) with the washer (2).
- Remove the driven top roller with the holder (4) from the holder
(5) and from the articulated shaft (8).
- Mount another top roller in inverted procedure to dismantling.
- Set the top roller according to the par. 3.7.8.2.
3.8 Setting the top roller lift
The maximum lift of the top roller when lifting the foot with
knee lever or with electromagnet is to be A = 12.5mm.
Caution! Danger of injury!
Switch off the main switch! Before starting the
setting operation, wait until the motor stops!
- Place a cube (1) having the height of A = 12.5 ± 0.7 mm
under the top roller.
- Screw in thoroughly downwards the screw (2).
- Tighten slightly the screw (3) in such a way that the lever (4)
turns on the shaft (5) with a certain friction moment.
- Push with the screwdriver on the lever (4), until it attains
the wall inside the arm of the sewing machine. In this
position, tighten duly the screw (3).
- Check the axial clearance of the shaft (5) which should be
the least possible.
- Set the normal pressure force of the top roller.
4
5
3
2
1
A
6
3
1
4
2
5
4
3
1
2
7
5
6