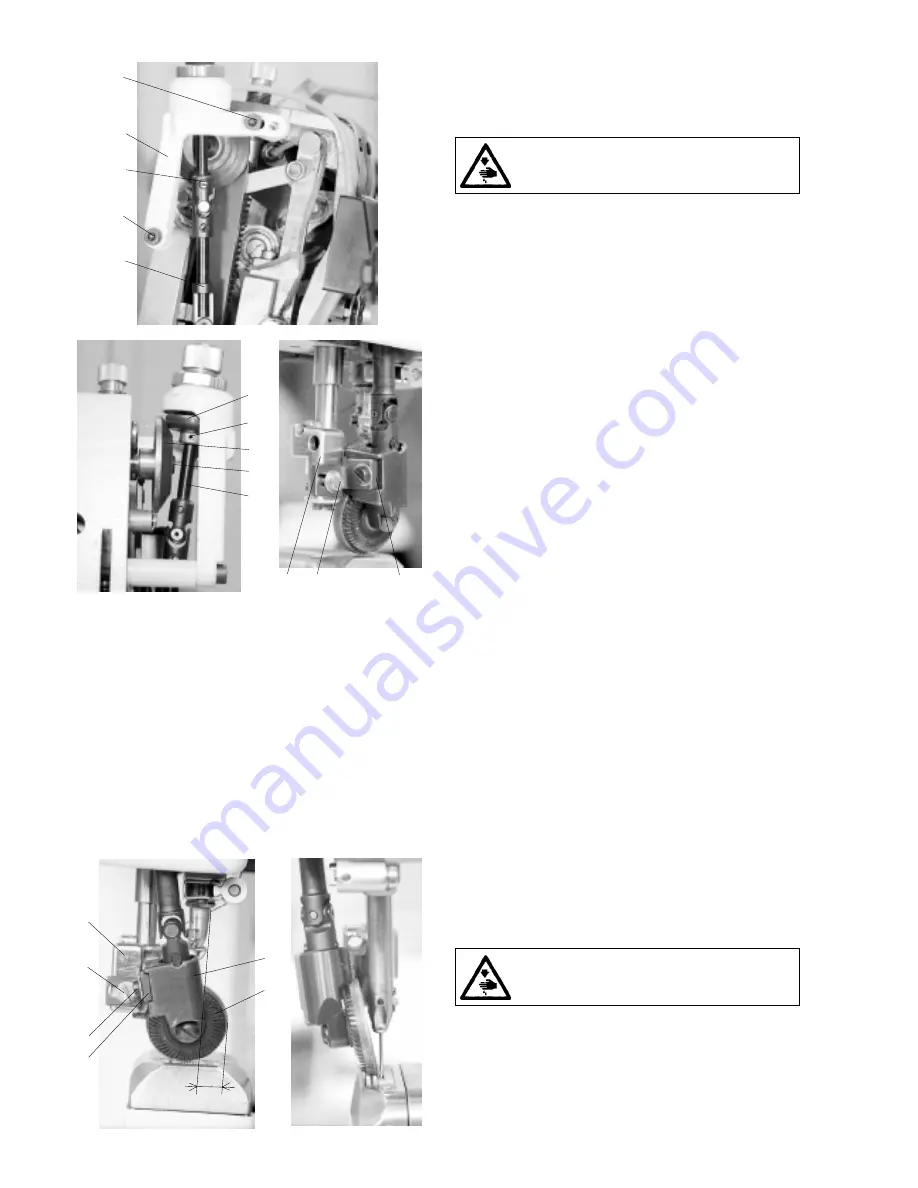
18
3.6.7 Replacement of friction wheels of the drive
conversion unit
The worn friction wheels (1 and 2) of the drive conversion unit are
to be replaced. This is done as follows:
Caution! Danger of injury!
Switch off the main switch! Before starting the setting
operation, wait until the motor stops!
- Remove the front guard.
- Loosen and unscrew the screw (3) from the holder of the wheel
(4) and remove it from the holder (5).
- Loosen the screws (6 and 7) of the holder (8) and remove the
holder (8) with the telescopic shaft (9) and the driven wheel
from the machine.
- In pulling it out, remove the telescopic shaft (9) from the holder
(8).
- Loosen and unscrew the screw (10) and remove the shaft (11)
with the friction wheel (12) from the telescopic shaft.
- Press out the pin (13) from the shaft (11) and the wheel (12).
- Replace the wheel (12) by a new one and proceed to a reassembly
(an inverse procedure to the dismantling).
- Loosen the screw (14) of the conic friction wheel (15).
- Remove the wheel (15) and replace it.
- Proceed to a reassembly (an inverse procedure to dismantling).
3.6.8 Top roller
3.6.8.1 Selection of the top roller diameter
The machine can be supplied with two types of top roller,
namely with the diameter of 25 mm and with the diameter of
35 mm. The suitability of the diameter used depends on the
type of sewing and on the concrete technological operation.
There are in general valid the following principles for the
selection of the wheel diameter:
ø
25 mm - for sewing small radii
ø
35 mm - for sewing straight sections or big radii
- for sewing with great passages to thicker materials
3.6.8.2 Forward, rearward and side setting
The top roller must be in a defined position in relation to the
needle:
a)view (see Fig. 1) - the value X depends on the diameter of
use top roller (
ø
25 - 6.5 mm;
ø
35 - 10.5 mm), it is measured
from the the needle bar up to the roller edge when turning
the handwheel to the 180
°
of the scale against the indicator
b)view (see Fig. 2) - the wheel edge must fit with the edge of
the needle operture at the spot of the needle punch.
These values are to be set as follows:
Caution! Danger of injury!
Switch off the main switch! Before starting the setting
operation, wait until the motor stops!
- Loosen the screw (1).
- By shifting the holder (2) with the top roller (3) in the groove of
the holder (4) set the required value X and tighten the screw(1).
- Loosen the screw (5)
- By shifting the holder (2) in the holder (6) set the bottom edge
of the roller to the edge of the needle operture.
- Tighten the screw (5).
9
7
10
8
6
3
5
11
14
15
13
12
4
X
3
2
6
5
1
4
obr. 2
obr. 1