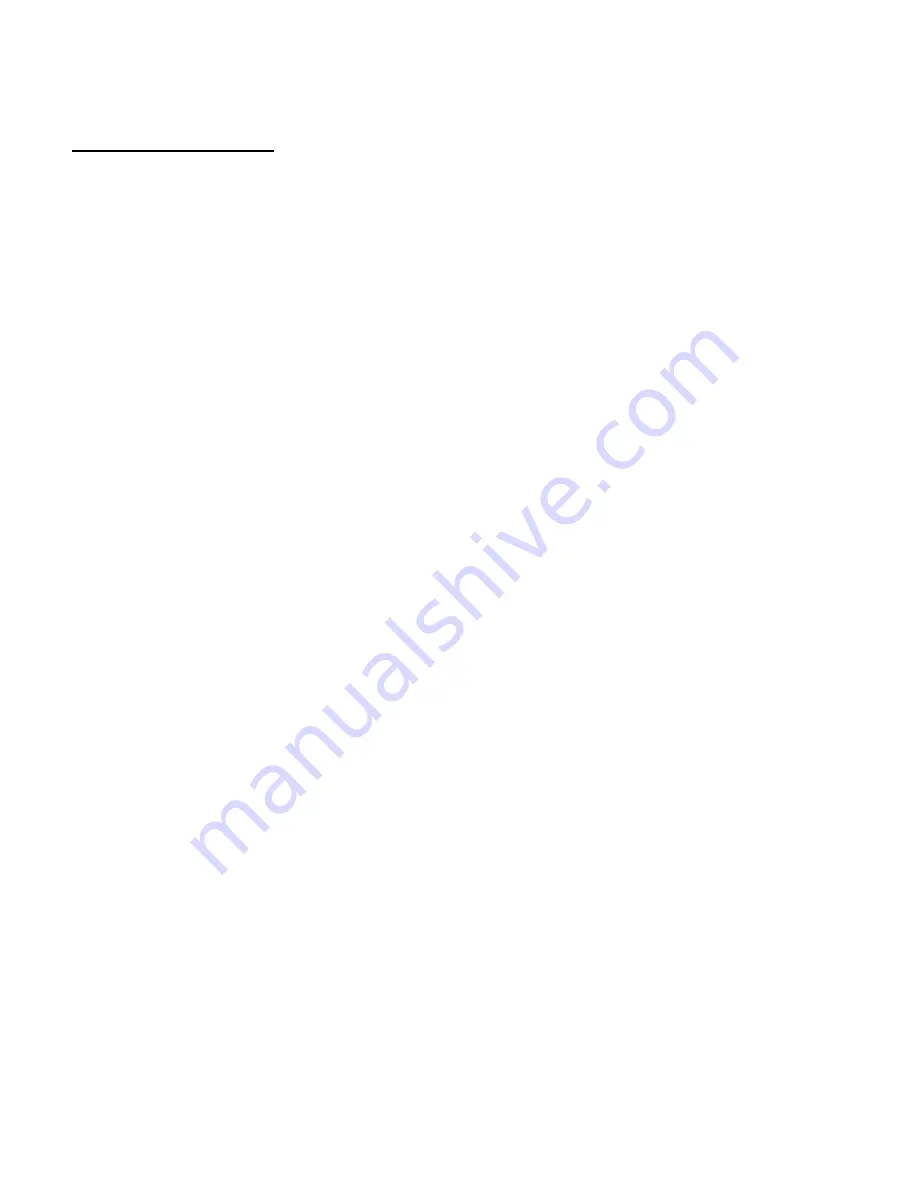
20
SECTION 5
OVERHAUL
Disassembly/Reassembly
General
Read these instructions carefully and check the
appropriate typical Cross Section Drawing with
your own assembly drawing to determine the extent
of disassembly that is necessary to remove
bearings, applying force only to the inner race when
removing from a shaft.
Match mark all parts before removing to aid in
reassembly.
When reassembling the unit, the use of new
bearings is recommended. After all machine fits
have been checked, repaired or replaced, proceed
with reassembly.
Installation of Bearings
Bearings should never be forced onto a shaft or into
a housing by blows applied to either race. To do so
is to risk serious damage to the bearings. Use
either an arbor press, or a jack and a piece of soft
metal tubing squared on both ends, if necessary.
Be careful to start the bearing true, not cocked;
otherwise it is possible to burr the shaft. A light film
of oil or other lubricant on the shaft will prove an aid
to mounting. Be sure that the shaft and bearing
bores are well cleaned before the bearing is
installed. Also, the mechanic doing the work should
be careful that particles of metal or other foreign
matter do not enter the bearing during installation.
Do not unwrap bearings until ready for installation.
When a bearing is to be pressed over a
considerable length of shaft, or over a tight-fitting
seat, it may be necessary to expand the bearing by
heating in oil. When a bearing is heated in oil, the
temperature of the oil should not exceed 93°C.
(200°F.) and the bearing should not be kept in the
bath longer than necessary to bring the entire
bearing to the required temperature.
AB-703 & AB-705 Disassembly
1. Remove unit from operation and pull off shaft
coupling hubs, or sheaves, with approved
bearing puller and remove shaft key(s) (1).
2. Remove junction box cover by removing two
screws. Disconnect brake leads inside of
junction box.
3. Remove four cap screws and lockwashers (2)
from field assembly (3) and slide entire field and
shaft assembly out of housing (4). Slide field
assembly off of bearing.
4. Using an approved bearing puller, remove
bearing (5) from each end of shaft (6). Force
should be applied only to the inner race when
removing bearing.
5. If necessary, remove bolts holding the coil to
the field assembly after match marking, being
careful not to scrape insulation off of coil Ieads.
6. If necessary, remove snap ring (7), fan (8) and
key (9) from the shaft; heat hub of fan if
necessary.
7. Clean all pieces of grease and dirt before
reassembly.