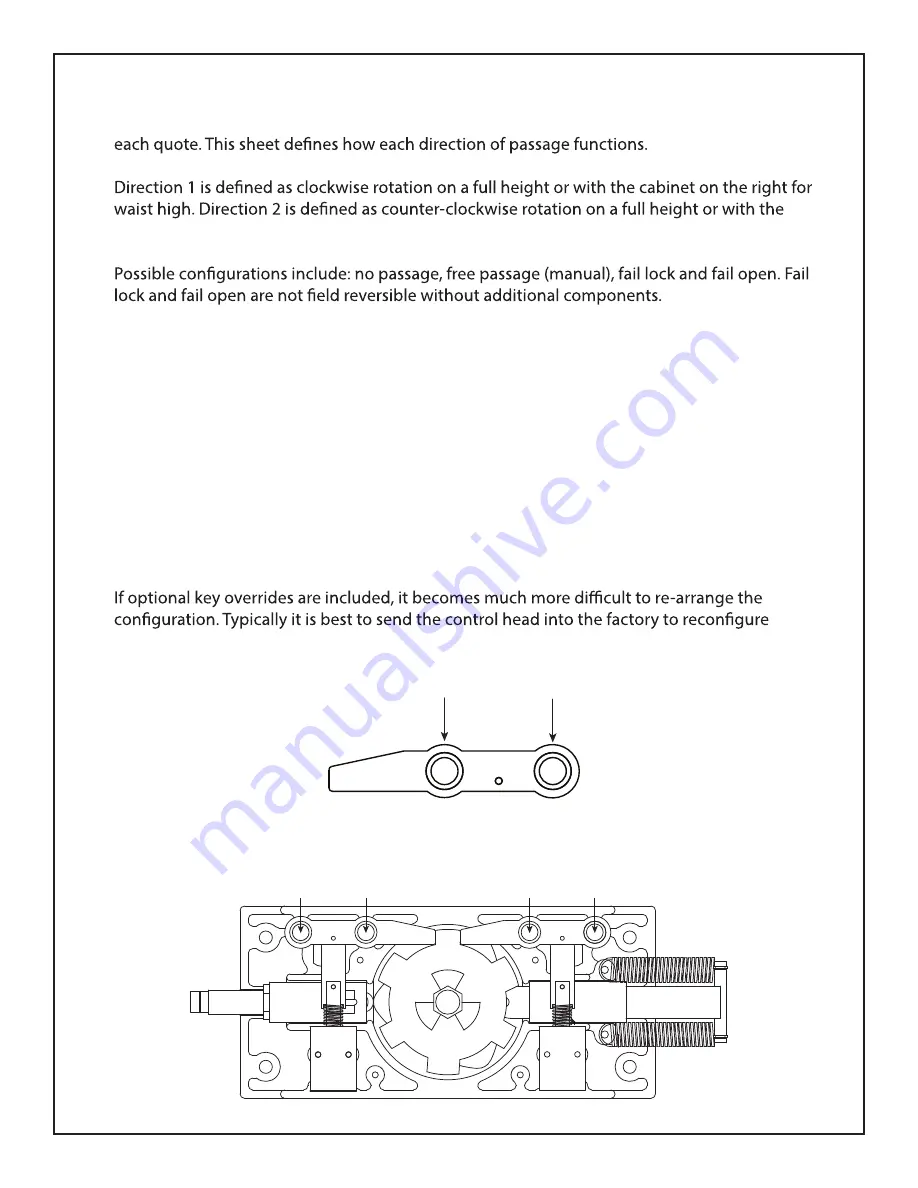
6500 Series Control Head Locking Bar Information
The 6500 Series Control Head is built to order based on a direction set up sheet sent with
cabinet on the left for waist high.
“No passage” directions include a fail lock locking bar assembly as well as an unwired solenoid.
This adds the appropriate parts to the control head to prevent it from rotating in that direction.
“Free passage” (or manual) directions remove the solenoid and locking bar assembly, allowing
the cam to spin freely.
Each direction has a pair of holes on the locking bar and control head casting. These holes
act as pivot points for the locking bar casting. The inner holes are fail lock and outer holes
are fail open. A .5“ dowel pin slides through the entire assembly to hold everything in place.
Alternate linkages and springs are needed to convert a direction’s power failure status.
any key override equipped head to ensure everything is done correctly.
Direction 1 Solenoid
Direction 2 Solenoid
Fail Open
Pivot Point
Fail Lock
Pivot Point
Fail Lock
Pivot Point
Fail Open
Pivot Point
Fail Lock
Pivot Point
Fail Open
Pivot Point
0381
Locking Bar Casting
Hardened 4140 tool steel
casting w/ oil impregnated
bronze bushings.
512-321-4426
INS-DST80S-190401
Designed Security, Inc - 1402 Hawthorne Street, Bastrop Texas 78602 - (800) 272-3555
11