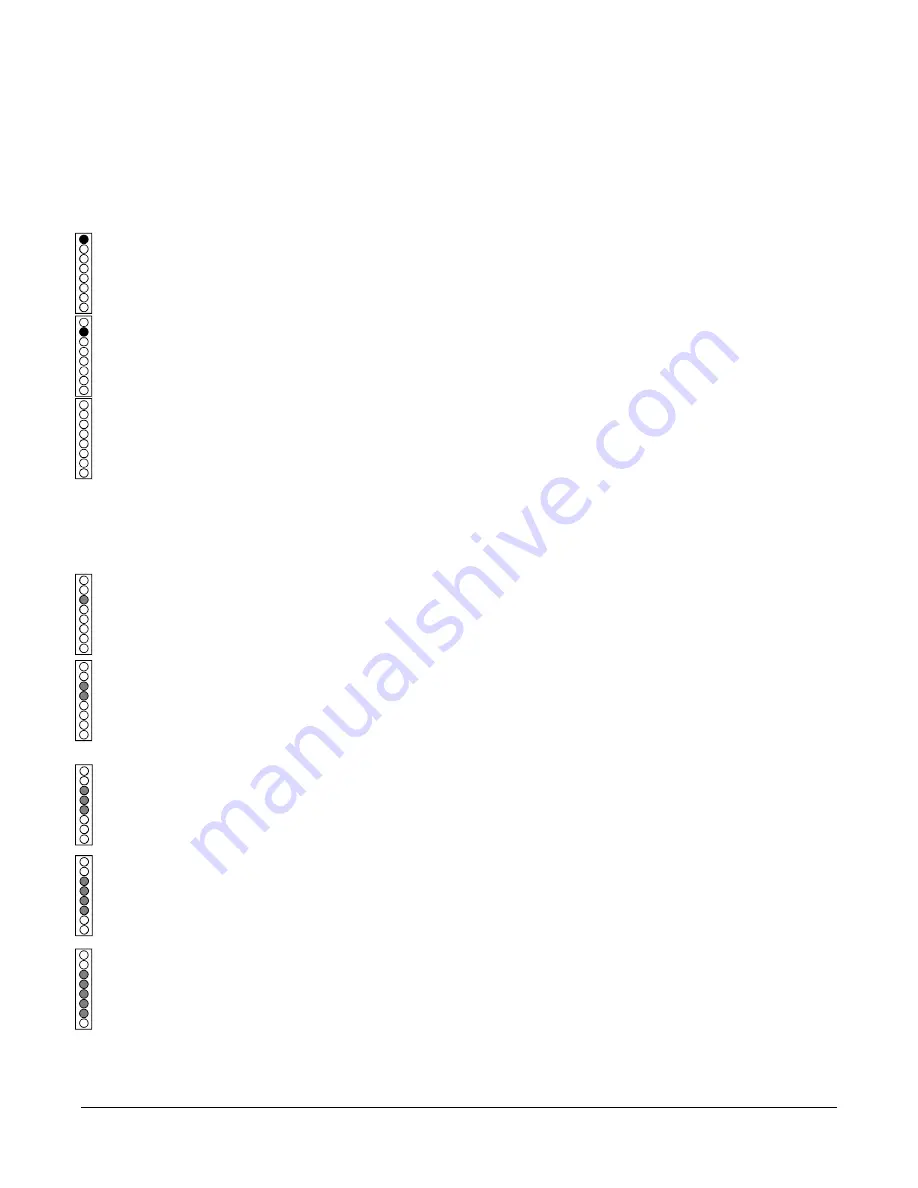
Troubleshooting
6-1
Troubleshooting
•
There are 2 red light(s) on the control panel, propane system (1 solid, 1 flashing); natural gas system (1 solid), which will indicate a
condition that has caused the unit to shut down.
•
There are 6 green lights on the control panel, which indicate the status of a sequence of functions while the unit is running.
•
When the burners are lit, all green lights should be on as well. Any green light which is not on should be considered burned out.
•
Temperature controller, pilot valve and main valve and lights go off and on as the water heater cycles.
•
The terminal strip, located inside heating module behind the RAYPAK water heater panel, must be accessed to initiate troubleshoot-
ing procedures.
No power at terminal P2 on low water cut-off
Check for 120 volt power at letter P2 on low water cut-off. If there is no power, check the following:
a)
Low water situation. Check fluid level in tank and add if necessary.
b)
Defective low water cut-off. Replace low water cut-off.
No power at terminal #2 on low gas pressure (propane system only)
Check for 24 volt power at letter NC on low gas pressure switch. If there is no power, check the following:
a)
Low gas pressure situation. Check volume level in supply tanks and refill if necessary.
b)
Defective low gas pressure switch. Replace low gas pressure switch.
No power at flow switch
Check for 24 volt power between letter C and #3 on the terminal strip. If there is no power, check the following:
a)
Pump not running.
- Check power and toggle switch on control panel.
- Check for 110 volts at pump motor. If correct power is confirmed at motor, but pump won't run, replace pump.
b)
Inadequate flow.
- Check that all valves are open in the fluid-transfer loop.
- Filter screen may be plugged. Use flush hose/valve attachment into a bucket, while pump is running, for a quick flush. Eventually the
system may have to be drained and the filter screen removed and cleaned by hand.
c)
Defective flow switch. - If a) and b) check out, the flow switch will need to be re-calibrated or replaced.
No power at out-going side of high limit switch
Check for 24 volt power between letter C and #4 on the terminal strip. If there is no power, check the following:
a)
Check switch settings. The automatic high limit should be set 10ºF higher than the set point of the temperature control.
b)
Defective high limit switch. Replace high limit switch.
No power at out-going side of flame roll-out switch
Check for 24 volt power between letter C and #5 on the terminal strip. If there is no power, check the following:
a)
Check manual reset button on the switch and reset; if tripped restart system and watch for a flame roll-out.
b)
Check for blockage in the heat exchanger in the form of foreign debris or soot build up. (See the operators manual for proper cleaning
procedure)
c)
Check entire vent system for possible blockage or restriction and correct problems.
No power at temperature control
Check for 24 volt power between letter C and #7 on terminal strip. If there is no power, check the following:
a)
Check that setting on temperature control is at desired operating temperature and the supply temperature is lower than the set point.
b)
Check well sensor (electronic), and verify that it is intact and positioned properly in its well.
c)
If a) and b) check out, replace both temperature control and well sensor.
No power at pilot valve
Check for 24 volt power between letter C and #8 on terminal strip..
a)
If no 24 volts replace Ignition Module.
No power at main burner
a)
Defective Ignition Module
- Check for power between letter C and #9 on terminal strip. If no 24 volts replace Ignition Module.
b)
Pilot failure
- If pilot has not lit but spark is present, check manual valve in the gas line and make sure its open. Verify that gas is present as far as
the pilot burner. This may involve purging air from the line and checking for plugged pilot orifice.
- If no spark was present at pilot electrodes, check pilot burner for good ground. Check condition of high voltage ignition wire and clean
pilot ignition electrodes. Replacement of pilot burner assembly and ignition wire may be necessary.