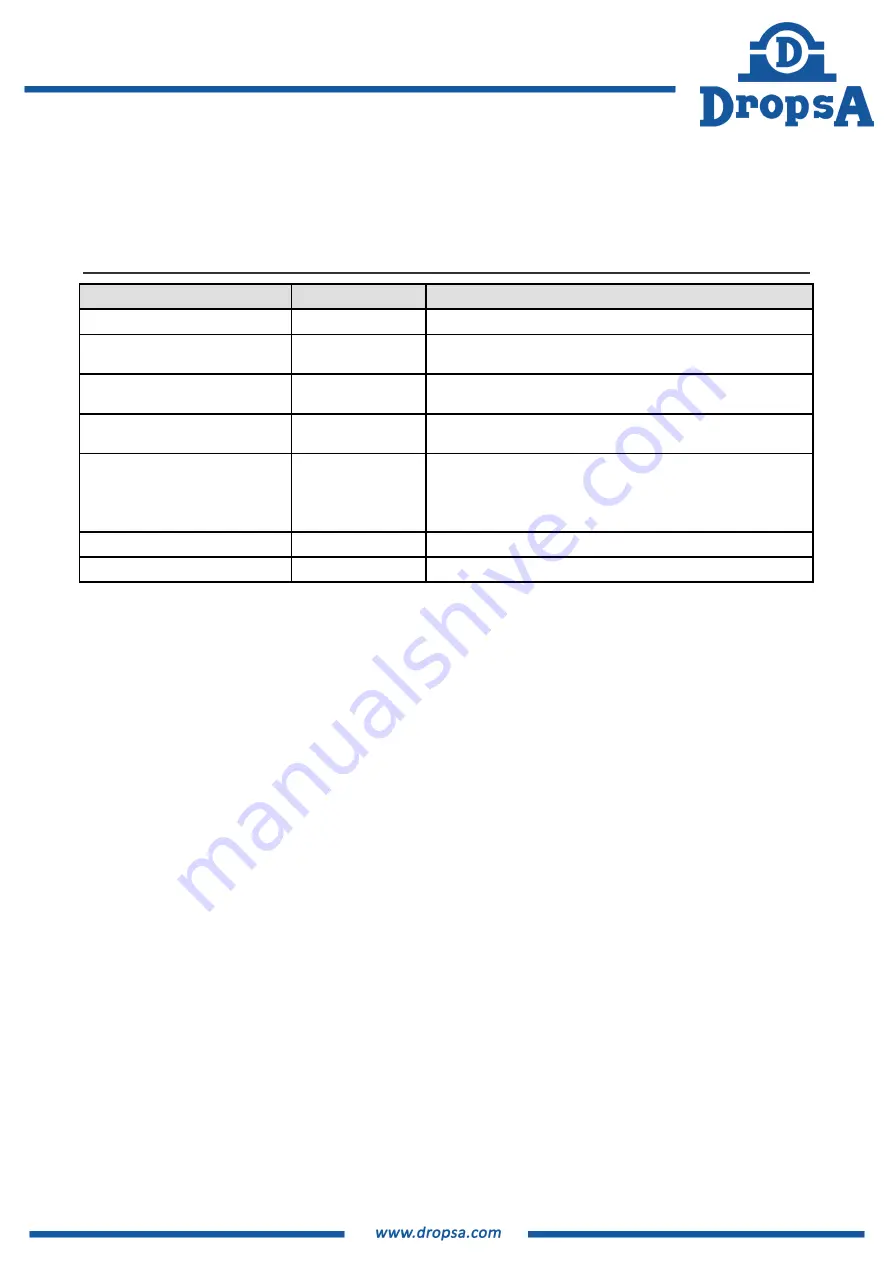
27
6.2
Scheduled maintenance
The following table lists the periodic inspections, the frequency and the intervention that the
maintenance will have to carry out in order to ensure the efficiency of the system over time.
Table 6 – Scheduled maintenance times
CHECK
FREQUENCY INTERVAL
INTERVENTION
Cleaning
Daily
Carefully remove any residues and powders and any foreign objects.
Check pressure
Daily
Check the operation of the pressure detection / reading system relative to
the grease distribution system downstream of the machine.
Check fastening
Monthly
Check the correct fastening of the machine in its place of installation
monthly, whether wall or floor mounted.
Check fixed guards
Monthly
Check the integrity of the MACHINE’s fixed guards and their fastening
monthly, particularly concerning the upper cover of the reservoir.
Attachment of the lines
After the first 500 hours
of operation
Every 1500 hours of
operation
Check the joint fittings.
Check the fastening to the parts of the machine.
Reservoir level
As required
Restore the grease level in the reservoir.
Filling filter
As required
Check and possibly replace.
6.3
Special maintenance operations
The special maintenance operations assigned to the user are indicated below, to be carried out as
necessary.
6.3.1
Replacement of the pumping element
In the event of low pressure in the grease distribution circuit downstream of the machine or a lack
of or partial lubrication, the pumping element on the relative lubrication line must be replaced.
Therefore, operate as follows.
1.
Empty the reservoir
in order to avoid lubricant spills
2.
Position the electrical
disconnect switch
on the machine’s power supply line to
O
– OFF
or
remove the wall plug.
3.
Always ensure the absence of pressure
in the grease distribution system downstream of the
MACHINE
.
4.
Disconnect the piping
for grease distribution from the pumping element being replaced.
5.
Unscrew and remove
the pumping element being replaced, using an appropriate wrench.
6.
Position the
new pumping element
.
7.
Tighten the pumping element
with a suitable torque wrench to a tightening torque of
70 Nm
.
8.
Reconnect the piping
and tighten it correctly and solidly.