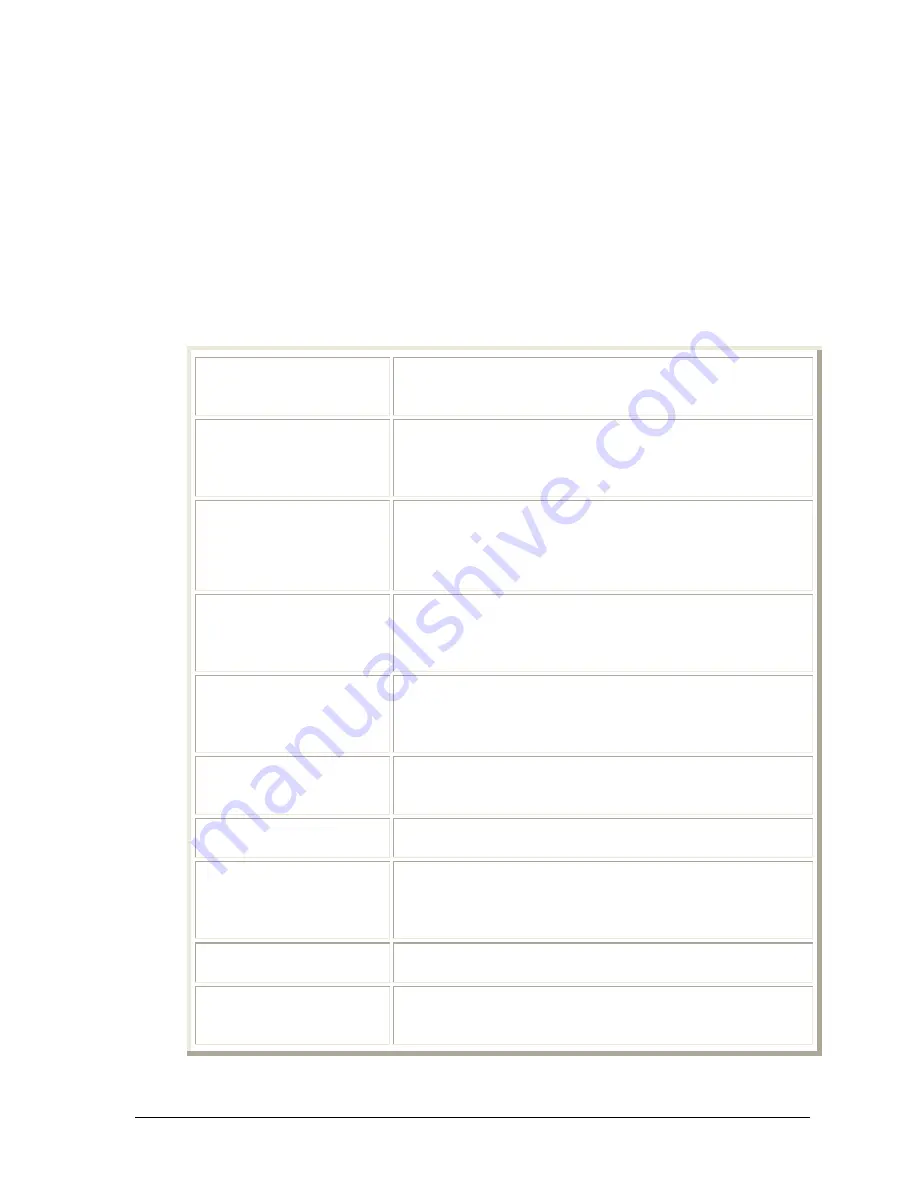
1
February 2007
Part No. 891817 Rev A
1. INTRODUCTION
1.1. Equipment
Covered
This manual describes the installation and operation of the Wayne 700 Series Small Fleet
Pump & Meter.
Any questions concerning the installation and operation of the pump that are not covered in
this manual should be referred to your authorized Wayne service personnel or Wayne
Technical Support (1-800-926-3737).
1.2. Technical
Information
Models
720: Pump and meter/register combination
730: Pump only
700R: Meter/register only
Application:
For dispensing low viscosity petroleum fuels - diesel,
including biodiesel blends up to 20%; kerosene; and
gasoline with up to 15% ethanol - from aboveground storage
tanks. Not for refueling aircraft.
Performance:
Up to 20 GPM (75 LPM) – 60 Hz motor. Up to 62 LPM –
50 Hz motor. Minimum dry vacuum – 15” of mercury.
Note: Actual flow rates received will depend upon the installation conditions
and the pump accessories such as the meter, hose size and length, nozzle
type, etc.
Register:
Model 700R meter/register. Included with model 720.
4-wheel register with manual reset knob. Displays up to
999.9 gallons. 7-digit (with tenths) non-resettable
accumulative totalizer. Optional liter measure.
Meter:
Model 700R meter/register. Included with model 720.
Phenolic nutating disc measuring chamber in aluminum
housing. Ac/- .5% at full flow. Adjustable
calibration. Die-cast aluminum housing.
Pumping Unit:
Self-priming, direct-drive rotary vane pumping unit. Cast
iron housing. Sintered iron rotor with eight carbon graphite
vanes.
Motor & Electrical:
1/3 HP, 1725 RPM, intermittent duty motor with thermal
overload protection. 115VAC, 60 Hz.
Junction Box:
Meets UL 87 requirements. Weatherproof o-ring seal. AC
auxiliary line for optional solenoid valve control. External
motor switch in separate internal compartment. Die-cast
aluminum construction.
Strainer Assembly:
Combination strainer and spring-loaded check valve with
pressure relief assembly. Cast iron housing.
Anti-Siphon Valve:
Integral vacuum breaker in meter discharge. Duckbill
design. Copper tubing returns any drips back to tank through
fitting in the strainer base.