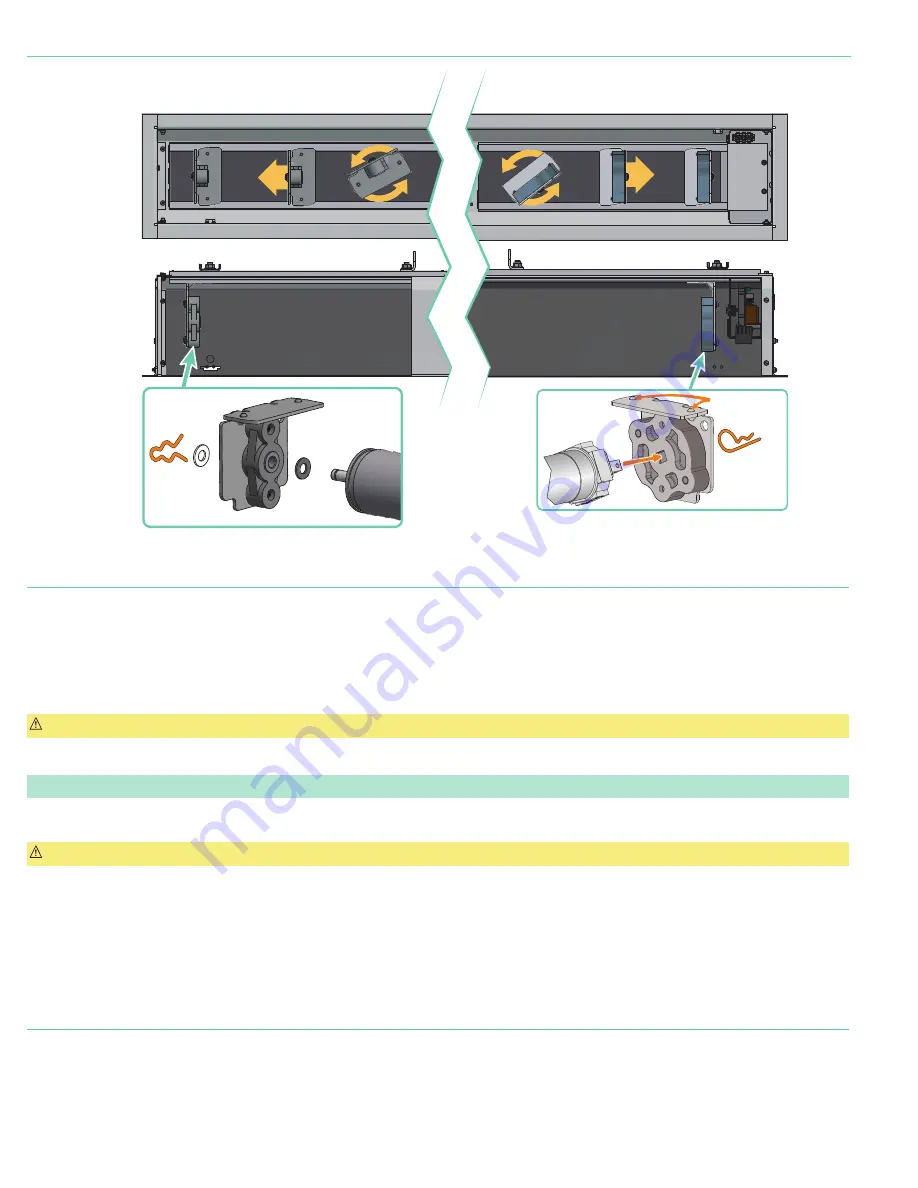
Section 4 -
Motorized Roller/Fabric Installation
1.
Remove bottom access panel
(See Section 3)
.
2.
Back out set screws from top side of motor mounting brackets
(See above)
.
3.
To engage motor end bracket flange
(above the two channels in the top of the screen housing)
, rotate bracket approximately 45° counterclockwise to allow top surface of
motor bracket to rest flat against top inside housing.
4.
Rotate bracket clockwise until it engages in channel.
5.
Engage idler end bracket in same manner as motor end bracket and slide toward opposite end of screen housing.
CAUTION:
Step 6 requires two people to perform safely.
6.
Locate retaining clips attached to instruction sheet. Lift roller/fabric assembly into screen housing and engage motor head completely into motor bracket, making
sure limit switch adjusting knobs are visible from bottom of screen housing
(Fig. 6)
.
Please Note:
If snap ring is provided, make sure it engages with motor. If retaining clip is provided instead, install to lock motor end in place.
7.
Support idler end of roller and slide mounting bracket toward roller. Insert roller pin into nylon bushing on idler bracket.
(Fig. 7)
8.
Roller idler pin goes through idler bracket. Reinstall washer and retaining clip.
CAUTION:
Failure to replace washer and retaining clip could result in separation of roller from brackets.
9.
Center roller/fabric assembly by sliding mounting brackets left or right.
10.
Securely tighten set screws on roller mounting brackets.
11.
Connect electrical plug from motor to mating socket on junction box.
12.
Attach door support bracket/brackets.
13.
Reinstall bottom access panel as previously described.
Section 5 -
Motorized Roller/Fabric Removal
Reverse the previous instructions
("Motorized Roller/Fabric Installation")
for removal of unit.
SIDE VIEW
SIDE VIEW
BOTTOM VIEW
BOTTOM VIEW
MOTOR END OF CASE
IDLER END OF CASE
Motor End
Retaining Clip
Set Screws
Motor End
Mounting
Bracket
Idler End
Mounting
Bracket
Idler End
Retaining
Clip
Figure 5
Figure 6
Figure 7
page 4 of 7
Ultimate Access E and V 220V