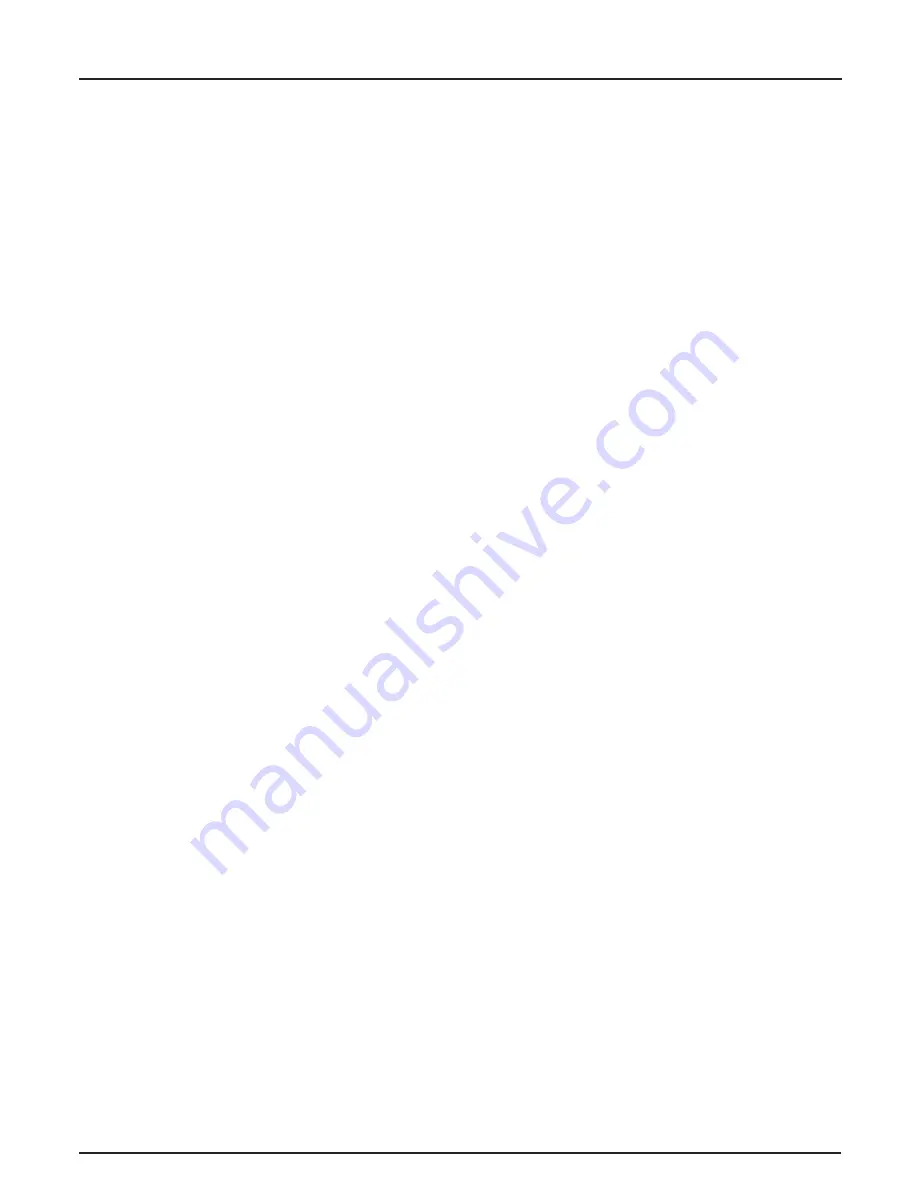
4. INTRODUCTION
5
4.1 SCOPE
AC welding machine suited to light repair and fabrication work.
4.2 SPECIFICATION
Stock no.
.................................................... 71090 ............................................... 71151
Part no.
................................................. AW164AT...................................... AW260AT
Rated voltage ................................................230V~50Hz......................... 230V/400V~50Hz
Absorbed power ................................................. 8.0kVA ........................................... 14.2kVA
Duty cycle
................................................10%@160A ................................. 10%@250A
Welding current range ....................................... 60-160A ........................................100-250A
Coupling device ................................................ Direct fit .......................................... Direct fit
Usable electrodes ........................................ 1.6mm-4.0mm ........................... 1.6mm-5.0mm
Insulation class .......................................................H...........................................................H
IP Protection class .............................................. IP21S ............................................... IP21S
Cooling device ...................................................... Fan ..................................................... Fan
Dimensions (LxWxH).................................. 470x240x320mm .....................585x325x440mm
Weight (nett)
..................................................... 16kg .................................................. 24kg
4.3 HANDLING & STORAGE
Care must still be taken when handling and lifting. Dropping this machine will have an effect
on its operation and may also result in personal injury. This machine is not a toy and must be
respected.
The environment will have a negative result on its operation if you are not careful. If the
machine is unprotected from dust and debris; components will become clogged:
And if not cleaned and maintained correctly or regularly the machine will not perform
at its best.